The RVD high-pressure hose is a flexible part of the pipeline, which is used in hydraulic communications for joining movable elements and supplying working fluids to them (machine oil, lubricants, etc.). From the name it is clear that such products are able to withstand high pressure indicators. They help to reduce vibration effects on specific parts of hydraulic structures.
Content
Varieties of WFD
The simplest, from a structural point of view, high pressure hoses are hoses equipped with a steel braid. Such products are unreinforced, however, due to the braid are able to withstand high pressure of the working environment. In addition, there are other WFDs that are worth paying attention to.
Braided sleeve. It features a high coefficient of flexibility, which allows the use of such a high-pressure hoses in almost all modern hydraulic structures. Sleeves equipped with a braid are used in pipeline structures for supplying a working medium under pressure. Such products consist of 3 main layers:
- interior;
- middle;
- external.
Note! Braided hoses are able to function in harsh operating conditions. The temperature range of such products ranges from −70 to +70 ° C.
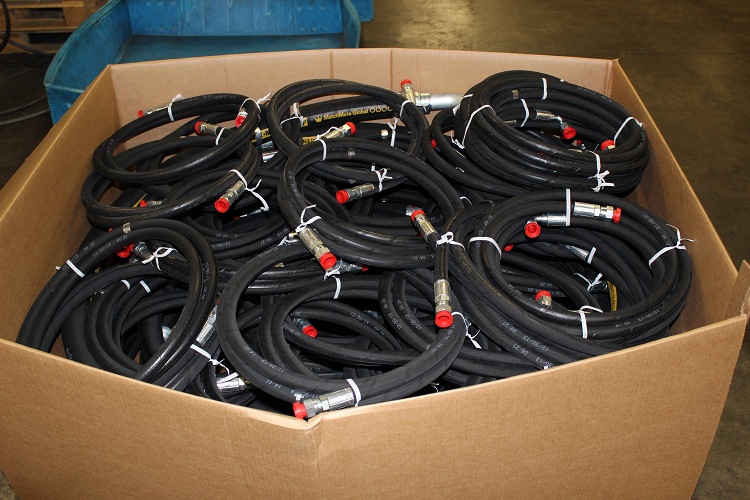
Rubber hoses consist of several layers of different materials, this gives the product high durability
Rubber spiral hose. The main function of such a device is to supply working fluids (emulsions or oils). Delivery of working fluids is carried out where their supply is accompanied by pulses. From a structural point of view, such sleeves are more complex than the previous type. Consider the main structural elements that are part of such hoses:
- external wire spiral;
- wire spiral located inside the hose;
- textile layer;
- rubber layer;
- directly textile.
The complexity of the design of this WFD allows it to carry out another important function - the removal of static electricity that occurs in hydraulic structures.
Polytetrafluoroethylene (PTFE). Such products are resistant to aggressive chemical compounds. As a rule, they are used in constructions with average pressure indicators.
Thermoplastic sleeve. The outer layer of such a product is made of materials resistant to temperature fluctuations. RVDs of this type can withstand temperatures from −40 to +100 ° C. In addition, it has high strength characteristics.
In addition, the WFD is classified into two main types:
- products equipped with metal coils;
- metal braided products.
In addition to the above types of RVD, there are others, however, they have a highly specialized operational area and are used very rarely.
Design features of high pressure hoses
Today, the most common are RVD with a braid.Sleeves of a high pressure consist of separate constructive elements. Consider the three main parts that include these devices:
- bellows part;
- braid;
- tip.
The bellows part is a flexible section of pipe that is distinguished by its ribbed design. There are several classification options for bellows corrugated tubes. Depending on the structure, the bellows tubes are divided into 2 types:
- consisting of one layer;
- two-layer.
In addition, the bellows tubes are separated by another important parameter - the shape of the ribs. Depending on the shape of the ribs, the bellows tubes can be of 2 types, namely:
- parallel;
- screw.
Braid - a structural element of most high-pressure hoses, which is a metal wire that enhances the strength characteristics of the sleeves.
Helpful information! In accordance with the standards, the thickness of the wire used to braid the high pressure hoses should be at least 0.3 mm. One braid strip, as a rule, includes from 6 to 12 wire threads.
In addition to enhancing the strength characteristics of the WFD, the braid also allows them to withstand higher pressures during operation.
A tip is a structural element of a high-pressure hose that performs connecting functions. The tip is a fitting (in some cases, a nut) and is used to connect the WFD with the rest of the communication.
Advantages of the WFD
High pressure hoses are different from ordinary pipes that are used in hydraulic communications, so you need to know their distinguishing features. Consider the main technical characteristics of high pressure hoses:
- all structural elements that are part of high-pressure hoses are characterized by good resistance to corrosion and aggressive chemicals. Due to this, they can be used in systems where various liquids act as a medium;
- the inner and outer layers of the WFD have good resistance to low as well as high temperatures. WFD can be used in difficult operating conditions;
- Another advantage of these products is a high coefficient of flexibility;
- As a rule, fittings and pressure testing of hoses, which are used in systems with high pressure indicators, are of good quality;
- the high quality of the sealing elements used in the installation of the high pressure hoses is also a guarantee of reliability;
- good resistance to mechanical stress.
Such products are popular in various operational areas. Let's consider some of them:
- metallurgy;
- oil industry;
- chemical production;
- construction industry.
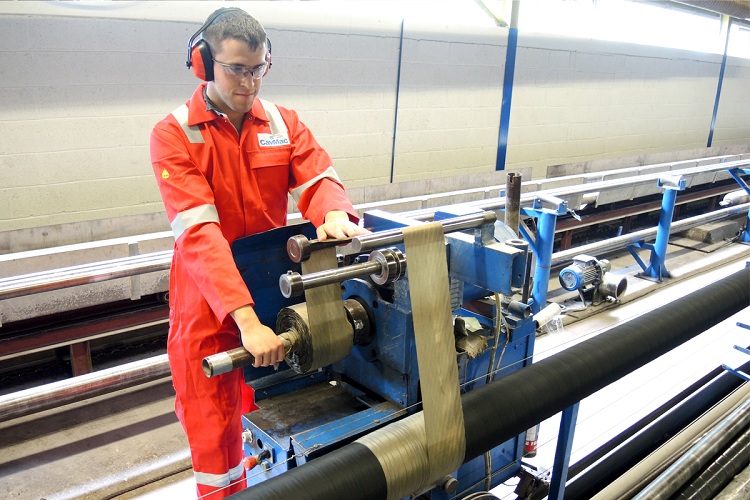
The production process for hoses includes several stages, the sequence of which is strictly followed
The manufacture of high pressure hoses is a serious event, which takes place in 4 stages:
- Preparatory stage.
- Crimp.
- Tests of the WFD.
- Application of special marking.
Preparation for the manufacture of high pressure hoses
Before proceeding with the manufacture of high pressure hoses of the high pressure hoses, it is necessary to carry out preparatory work. Preparation for the production of high pressure hoses includes:
- selection of structural elements for such hoses;
- setting up production equipment.
Important! Connecting elements (fittings) for high pressure hoses are selected depending on the cross section of the product. The choice of transition elements and various adapters also depends on this geometric parameter.
Next, focusing on the dimensions of the fitting, select special parts - cams for crimping.After preparing the crimping cams, the crimping press is set to the desired diameter. The next stage is the preparation of the edging machine and the cutting of the high pressure hose. This is a necessary process by which products of the required length are obtained. The slice made with the help of such a machine turns out to be as even as possible, which is very important for further manipulations. If necessary, the ends of the WFD are additionally cleaned.
Then it is necessary to remove the outer layer, which consists of rubber, from the hose. Removing the rubber layer is carried out before braiding by means of a special machine, which is called debarking. Not all hose types require rubber stripping (for example, for 2SN hoses).
In parallel with the removal of the rubber layer, a nipple-type coupling is assembled. Further, this connecting part is put on a high-pressure hose, and then fittings of the required sizes are inserted, selected earlier for a particular RVD. At the end, the crimping cams are installed in the crimping apparatus. Thus, preparatory work for the production of high pressure hoses is carried out.
Crimp
After the preparatory work is behind, you can proceed directly to the production of high pressure hoses of the WFD. The main stage in the manufacture of these products is crimping, which is carried out on special equipment, namely crimping machines. Before crimping, it is recommended that the equipment be checked for serviceability. To date, there are two options for crimping RVD:
- longitudinal method;
- transverse method.
Longitudinal. This option of crimping RVD is used, as a rule, in more developed European countries, however, it also occurs in Russia. The longitudinal production method allows you to get both varieties of these products (braided and wound). Production technology in this case involves the use of a coupling that has annular teeth. Ring teeth are located on the back of the part, which allows you to firmly fix the hose when crimping.
A high sealing rate is achieved by mechanical action on the hose. WFD obtained by this method are usually used in hydraulic structures, which are characterized by high pressure.
Transverse. Domestic production of high pressure hoses in most cases involves the use of the second method - the transverse. This method allows the manufacture of braided products. The technology of this method involves the preparation of special crimp couplings, which are pre-processed on the machine. This treatment allows you to remove the layer of rubber from its surface. After that, a direct transverse crimp is performed. Crimp type cams, in which the hose is fixed, compress it and as a result, a pattern resembling steps is formed on the surface of the hose.
Helpful information! The WFDs, which are obtained by the transverse method, differ in democratic cost and are used in structures where the working medium is under pressure not more than 12 MPa.
Testing and marking
Tests are a necessary step in the manufacture of high pressure hoses. This is due to the fact that finished products must be checked for quality. This check allows you to timely identify low-quality hoses. High pressure hoses must comply with existing state standards.
Before testing, as a rule, finished products are inflated. This is necessary in order to clean them from dust, dirt and other foreign elements.After purging the hose, it is connected to the necessary test equipment, which is responsible for supplying a working medium under a pressure that is approximately 2 times higher than the normal operating one. During testing, oil or water is used as the working medium. If the hose has withstood the necessary pressure and there are no cracks or other defects on it, then it is considered suitable for use. After checking, the hose is again cleaned with air.
At the last stage, special markings are applied to the sleeves. After marking, finished products are sorted and packaged for storage or transportation.