The dyuritic sleeve is an accepted name for a rubber-fabric sleeve characterized by increased strength. The name comes from the ambiguous Latin word durus - tough, strong. The frame structure of the product provides a combination of strength and flexibility. The internal section remains unchanged when twisting, bending. Due to these advantages, the dyurite sleeve has a very wide application in many fields.
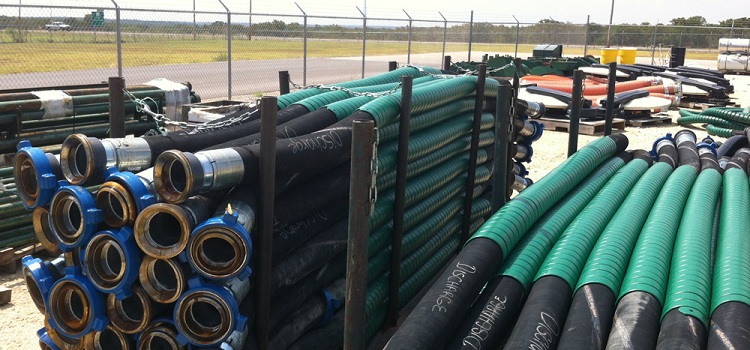
The dyurite sleeve is characterized by high strength, durability and can be used in a wide variety of construction, manufacturing and household sectors.
Content
Duritic sleeve: areas and application features
A flexible sleeve is made like a sandwich. Its internal and external coating is made of rubber of sufficient thickness and density. A layer (or several layers) of rubberized fabric is laid between them. The presence of dispersed mineral inclusions in any of the three layers of the structure is permissible. But their size should not exceed 0.3 mm. The same size limit is acceptable for bumps on the inside.
Durits are used as flexible pipelines in systems:
- air;
- hydraulic;
- oil;
- fuel, etc.
They are able to function in the temperature range from -55º C to + 100º C. The operational properties of such a sleeve determine its widest distribution, starting from the aviation and military industries and ending with the sphere of everyday life. It is impossible to imagine a special technique that can do without this product, unpretentious and reliable.
Important! The flexible sleeve should be stored exclusively in darkened rooms, where the temperature regime is observed in the range of 5-15º C. Under proper storage conditions, the product does not lose its consumer properties for a year and a half.
Corrugated sleeve
Corrugation has found application both in ventilation systems, transportation of bulk solids, and in special equipment. This is facilitated by its particular flexibility as a hollow tubular channel. Corrugated sleeves by the nature of the working environment are divided into classes:
- B - for gasolines, fuels and oils;
- B - for industrial water;
- G - for gas;
- KSh - for solutions (concentration - up to 20%) of inorganic acids and alkalis;
- P - for nutrients.
Corrugated sleeve MBS (oil and petrol resistant) is produced, equipping for extra strength with a metal spiral and an inner frame made of textile. Soft cuffs are placed at the ends of such a hose. The design is used for injection and absorption of gasoline and kerosene, jet fuel, diesel fuel and oil-based oils. Suction is carried out at a working vacuum of at least 0.08 MPa. The injection is carried out at a working pressure of not more than 0.8 MPa. Operation is permissible at temperatures from -50 º С to +90 º С.
Oil and petrol resistant hoses are provided with at least three-fold safety margin against bursting by hydraulic pressure.The MBS sleeve does not accumulate static electricity, so it is used for the transport of flammable liquids.
Flexible hose for ventilation
The ventilation sleeve is used:
- in air conditioning and ventilation systems;
- in vacuum systems;
- for supplying and removing hot and cold air;
- in auto repair shops to remove exhaust fumes and vapors.
A flexible ventilation hose has several advantages over a rigid duct:
- reduces vibration;
- has a small mass;
- differs in simplicity of installation, which does not require special skills and special tools.
In ventilation systems, the use of a flexible sleeve allows you to quickly and efficiently:
- to remove smoke, vapors and gases;
- remove dust;
- to bring out the exhaust air;
- draw chips, sawdust, abrasive dust into a special bag;
- work with granules used in various sectors of the economy.
Gas hose
The dyurite sleeve is also used for welding. Using it, gas is supplied to the welding equipment under high pressure for welding and cutting metals.
Hoses (gas flexible hoses) for welding equipment are divided into three classes, depending on what needs to be supplied to the torch or torch. A gas welding hose of class 3 is intended to supply oxygen at a pressure of 20 atm; it is customary to paint it blue or black. Class 1 hoses - red (for acetylene, butane, propane). Class 2 - black or black with yellow (for liquid fuels, mineral spirits). They are designed for pressures up to 6.3 atm.
In conditions of the tropics and subtropics, hoses can be operated at temperatures from -35 º C to +70 º C. In cold climates, the temperature range is wider: from -55 º C to +70 º C.
Good to know! On a gas (like any other) sleeve, marking is mandatory, indicating the manufacturer, class, internal (working) diameter and the highest working pressure.
The sleeve is hydraulic
Hydraulic hoses are used in systems of various devices and mechanisms. Their design is subjected to high pressure, therefore, it has certain features. The outer, thicker layer of the sleeve is made of especially durable, wear-resistant rubber. If necessary, the outer layer is supplemented with a thermal protective corrugated coating, polymer or metal. Between the inner and outer layers of the rubber coating, several layers of metal wire (or textile) are wound, interspersed with a thin rubber film. Metal wire gives the hose greater strength and rigidity.
According to the method of winding wire, hoses are divided into two types:
- Coiling, when the wire is wound in even rows.
- Braided, when the coils are wound, crossing with the previous layer. Hoses of this type are more durable, withstand more pressure.
The thickness of the rubber layer, the number of layers of wire in the manufacture of the hose are set based on its scope.
How to choose hydraulic hoses
When choosing hoses or hoses for hydraulic systems, you need to follow a few simple rules:
- know exactly the value of the working fluid pressure in the hydraulic system for which the dyurite sleeve is selected. As a rule, markings should be present on the sleeve itself. If available, it immediately becomes clear whether the sleeve is suitable or not. If there is no labeling, you have to contact a consultant;
- pay attention to the operation in which temperature range the hose is designed. A very unpleasant nuance is possible when the product is intended for use in high pressure conditions, but is not suitable for use at elevated temperatures;
- take into account the composition of the working fluid;
- the product must not be damaged or cracked. It should be washed so that small particles accidentally adhering do not lead after connecting to a hydraulic system malfunction;
- choose the right length. Normal operation will become more difficult if the connecting hose or sleeve is excessively sagging or its tension is excessive.
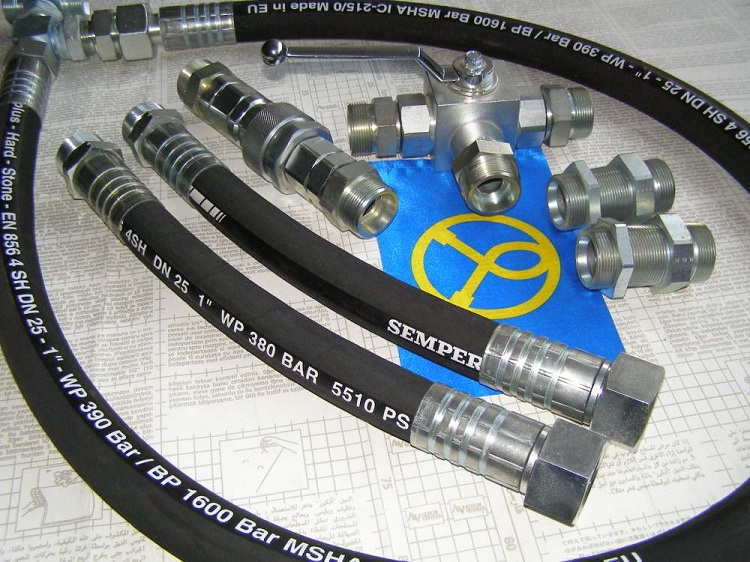
Sleeves vary in many respects, and when choosing a hose, you need to take into account all the characteristics of the products and the conditions in which they will be used
Carefulness in the selection of hoses will pay off the time spent. The products will last long and reliably without unexpected breakdowns.
How to install or replace hydraulic hoses
Proper installation of the hose will not be accompanied by any complications, if you do not allow violations of the process technology. Replacement (or installation of a new one) is carried out in several steps:
- Ensure that the product has the appropriate specifications (or is completely identical to the replacement).
- Check for damage and cracks on the product itself, as well as on o-rings and fittings.
- Prevent the formation of loops and unnecessary bends, significantly reducing the specified life of the part;
- A special line on the hose guides how it should be installed without twisting.
- The ends of the hose are inserted into the fitting at a smooth angle, otherwise entering will shorten the life of the hose.
- If the hose comes in contact with heating mechanisms, it should be insulated. But it is advisable to avoid such a neighborhood.
Important! After installation, the hydraulic system must be purged to remove air. This operation is carried out according to the instructions contained in the technical documentation of the unit or machine.
Dyuritovy sleeves - unpretentious and reliable design. They confidently pressed hard pipe connections. Flexible pipe connections are successfully used:
- in gas supply and water supply systems;
- in road construction, municipal, mining and other special equipment;
- in means for transporting flammable liquids and mixtures (liquid fuel, industrial oils, water-oil emulsions);
- in units and equipment of aviation, engineering, metallurgy. oil and gas and defense industries.
In order for dyuritic hoses to last as long as possible, you must follow the simple rules related to the installation and operation of the products.