Flexible polymer corrugated pipe has become an integral accessory for cable routing. The device of modern electrical, telephone, computer and television networks cannot be imagined without the use of DCS pipes for laying communications with a voltage of up to 1000 V. The distribution of these elastic products is explained by the fact that they simultaneously provide reliable protection of the laid networks and the amazing simplicity of their arrangement.
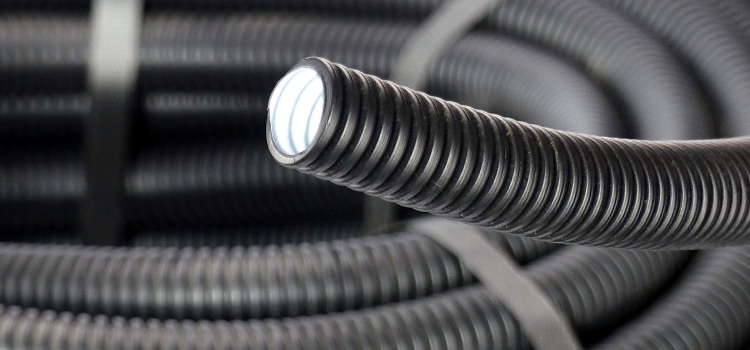
When laying electrical networks, it is customary to use non-combustible pipes in which the cable is laid
Content
Classification of polymer pipes for electrical networks
Flexible corrugated pipes, widely used in the installation of networks to protect the cable line, are distinguished by the material of manufacture:
- self-extinguishing PVC (polyvinyl chloride);
- flexible HDPE (low pressure polyethylene);
- LDPE (high pressure polyethylene). It is used as an external corrugation in two-layer products. Used for concealed installation if the structure is made of non-combustible materials;
- PP (polypropylene), indispensable for cable installation in monolithic construction;
- possessing increased moisture resistance of PA (polyamide).
Cable laying using a polymer pipe is possible in an open, half-hidden and hidden way. By design, pipes are distinguished:
- single-layer (single-wall), with a common wall for the outer and inner surfaces;
- two-layer (double-walled), corrugated on the outside and with a smooth inner surface.
Variant of execution matters:
- light pipes. Thin-walled and flexible, compactly placed on any bends and bends. Find application inside buildings, as well as under paneling of ceilings and walls;
- reinforced (heavy). Thick-walled and high-strength products for outdoor and underground structures, concrete foundations and concrete-cement screeds.
Helpful information! Corrugated pipes for laying cables can be produced with broaches - metal probes. Such a steel cable hooks onto a cable to pull it out from the back.
Products with a diameter of 16-63 mm are produced, as a rule, in bays, packed in heat-shrinkable plastic film, with a length of 15 m, 20 m, 25 m, 50 m and 100 m.
Benefits of using polymer pipes for cable
The use of a plastic protective sheath during the installation of cable pipelines is associated with good characteristics of polymeric materials that differ:
- sufficient strength to physical exertion;
- resistance to climatic effects, ultraviolet radiation, corrosion (in addition, condensate does not form and does not accumulate), chemically active substances;
- non-toxicity and environmental safety;
- ease of installation and laying, convenience and ease of installation, which does not require complicated special equipment and high professionalism;
- wide enough temperature range of application;
- the relatively low cost of performing work that does not require the use of welding;
- profitability, unpretentiousness in service and long terms of operation.
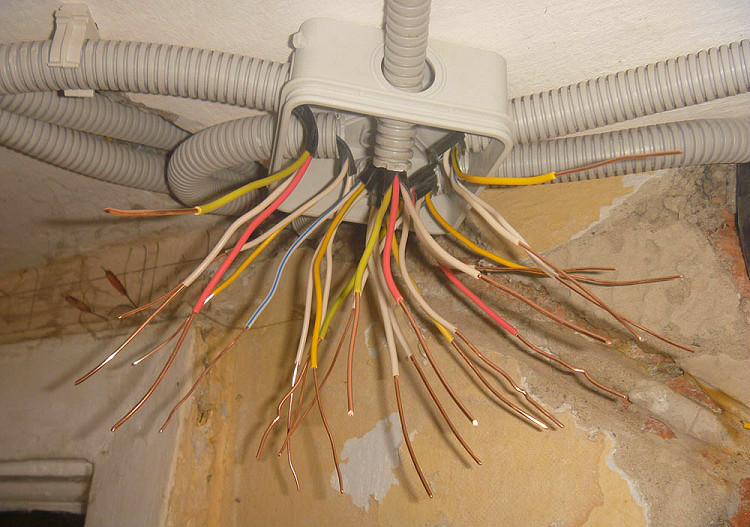
Using a corrugated pipe, it is very easy to install the mains without any special skills in this area
The use of HDPE pipes
For laying the cable underground, PND pipes of the following types can be used:
- halogen free;
- smooth walled rigid;
- double-walled, with a smooth inner shell of LDPE;
- light corrugated;
- heavy corrugated.
Extra strength is given by reinforcing with steel wire.
HDPE products are usually divided into:
- technical (as a rule, smooth single-walled);
- electrical (as usual, double-walled corrugated).
When conducting electrical wiring in a cement floor screed or in a brick wall, a smooth black protective sheath is used.
Important! For laying various networks with voltages up to 1000 V, the cable is laid inside products with a corrugated surface. The laying method can be hidden, half-hidden or open, installation is carried out both indoors and outdoors.
The selection of corrugated PND products for laying cables in the ground occurs due to them:
- increased strength;
- elasticity;
- ability to restore the original linear dimensions;
- ease of installation;
- the duration of subsequent trouble-free operation (up to fifty years);
- good electrical insulation properties, making grounding unnecessary.
The use of PVC electrical pipes
The choice in favor of the use of electrotechnical PVC products is explained by their obvious advantages:
- the durability of the upcoming operation, due to the lack of corrosion, ultraviolet radiation, exposure to aggressive and humid environments and durability;
- practicality and economical use, since they do not require painting and additional maintenance;
- lightness, which simplifies transportation and does not create additional load on structural elements;
- tightness, providing protection of the laid cable from dust and moisture;
- simplicity of assembly of the structure - they are easy to glue, solder or cut;
- hygiene and environmental friendliness.
There are two categories of electrical PVC products:
- Smooth-walled. Smooth rigid PVC pipes for cable are used, as a rule, outside of building structures.
- Corrugated flexible. The electrotechnical PVC corrugated pipe is laid inside the ceiling (under the plaster, in the screed).
GOST divides electrotechnical PVC products into:
- medium (C);
- moderate to severe (CT);
- heavy (T);
- non-standard (N).
PA pipe application
The advantages of flexible corrugated structures made of polyamide always include:
- very high impact resistance;
- frost resistance;
- increased resistance to repeated bending;
- the inertness common to all polymers with respect to the effects of corrosion, aggressive media, and ultraviolet radiation.
The DKS polyamide pipe used for laying the cable in the ground, as well as inside and outside structures and buildings, was provided with additional useful properties:
- increased resistance to both combustion and moisture;
- resistance to gas and liquid media;
- wide temperature range of operation and installation.
Polyamide cable insulation is recognized as highly reliable for industrial equipment, electric machines, vehicles and robotics.
How to install a polymer pipe for cable
No matter where the cable is laid using polymer sheaths, in the ground, in a brick wall or in an open way, the installation technology is common.Work begins with marking the placement of structural elements, including panel boxes. According to the rule, the distance to the heating elements must exceed half a meter. For each running meter, 7-10 fasteners are procured.
Note! Upon completion of the preparation of all the elements necessary for the installation of the structure, the voltage value in the power supply is checked without fail.
Pipe preparation includes, if necessary, cutting them to obtain sections of the desired length, aligning the wires and checking the cleanliness of the inner surface. Then the cable is pulled through the necessary elements and the sections are assembled in accordance with a pre-drawn diagram. In accordance with the marking, fasteners are made. Upon completion of the installation of panel boxes, the laid cables are connected into nodes in them. In conclusion, the reliability of the insulation of the cables is checked.
Carrying out installation is associated with certain nuances:
- when holding it in a brick wall, metal brackets are used for fastening, and pouring is carried out after the system is securely fixed;
- with the alleged formation of condensate, a installation tube for collecting it is mandatory;
- preparing the wires for broaching, it is advisable to grab them in several places with electrical tape;
- when conducting the pipe through the cavity of the plate or from the floor to the wall, it is recommended to use special corrugated connectors;
- with a depth of more than two meters when laying in a trench, it is planned to install a protective layer - a concrete channel reaching 80-100 mm in thickness;
- to connect in a straight line, it is desirable to use one single piece of pipe;
- with horizontal installation, concreting into the foundation is permissible;
- the formation of creases makes it difficult to pull the cable;
- in the absence of a metal probe for broaching in the kit, it is possible to use a nylon or metal broach, which is launched into the pipe.
Laying cables using polymer pipes is always accompanied by a leak test of structures. The conditions for the use of cables, their sizes determine the choice of the most suitable products for a particular case, capable of ensuring impeccable durability.