Profile pipes are widely used in modern construction. Their cross section can be square, rectangular and oval, which allows you to assemble light and durable metal structures for tasks of any complexity. In view of this, welding of profile pipes requires the contractor to have certain skills in performing such work. Only then will the final product - communication networks, stairs, gates and other structures be truly reliable.
Advantages and types of metal shaped pipes
These products are made of carbon steel or stainless steel. The cross section of the pipes varies in the range of millimeters, and the wall thickness is millimeters.
The popularity of these products is due to many factors. Among them:
- affordable cost;
- low metal susceptibility to deformation;
- relatively small mass. Compared to plastic counterparts, the weight of these products is, of course, more, but, as practice shows, this is not critical;
- uniform wall thickness;
- durability and excellent reliability during the service.
In addition, the use of metal shaped pipes allows you to create a design with the required technical characteristics. And it does not matter how unusual and complex it is. In any case, the life of the system will be very long. An additional argument in favor of this choice is that the welding of a profile pipe is an objectively inexpensive and simple process.
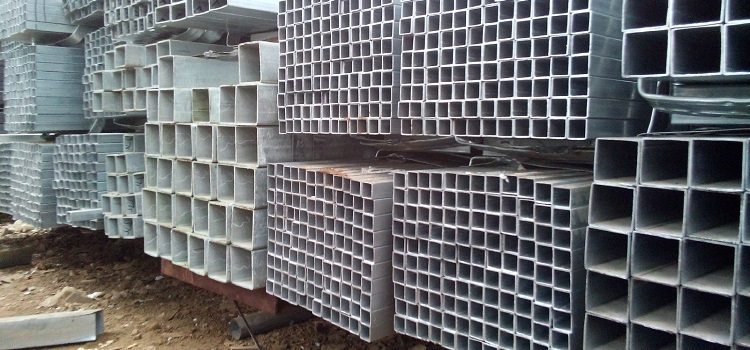
Profile pipes are available in a variety of sizes and serve both as the basis for buildings and for simple structures such as fencing
Today in industry, the following types of these products of the metallurgical industry are used:
- seamless hot and cold formed pipes;
- cold-deformed electric welded;
- electric welded.
Welding methods
Welding of steel profile pipes is carried out by the following known types of welding: electric arc, gas, contact and semi-automatic (welding by inverter).
Electric arc welding. The high demand for this method is due to its simplicity. This factor allows you to form a high-quality seam even in hard to reach places. Arc welding of profile pipes is done by T-joint, butt, lap or at any angle available.
Helpful advice! Long-standing welders recommend a lower weld position. However, you must proceed from your conditions: you can use a vertical or horizontal seam.
To perform the work you will need a welding machine and electrodes. It is advisable to have at your disposal a device that allows you to fix the pipes in the required position. It is also necessary to stock up with sandpaper and buy a metal brush. And of course you can’t do without a mask and gloves.
The choice of electrodes must be approached very carefully. If they are excessively large in diameter, you risk burning through the pipe, and a small thickness will not provide sufficient weld strength. The electrode must:
- to maintain a steady smooth burning of the arc;
- inhibit the course of oxidative processes.
Welding profile pipes of the same cross section is performed by non-consumable electrodes in an environment where argon acts as a protective gas. With regard to their diameter, the following recommendations exist:
- welding of thin-walled profile pipes with a thickness of up to 2 mm should be performed with electrodes of Ø 1.5 mm;
- with a wall thickness of up to 3 mm, professionals advise using electrodes of Ø 2 mm;
- for metal with a thickness of 4-6 mm, you will need Ø 4 mm electrodes.
After fixing the parts to be welded on the table or on a fixture specially created for this, remove lubricants and dirt from their surface. To fix the structure, pinpoint the metal. The basis of the process begins after leveling. Lead the welding arc at a speed sufficient to melt the edges, but the metal should not have time to flow inward. This is a general recommendation. And to learn how to choose the right speed will only practice.
Welding of thin-walled steel profile pipes is carried out in one step. To connect the thicker metal and boil all the layers, it will take several passes. Reducing stress in steel and making several seams allows the cutting of edges. The welding mode depends on the voltage, as well as on the strength, polarity and type of current. The initial data for calculating the current strength is the thickness of the electrode. The range of values for this parameter is: ampere. When working with thin-walled metal profile pipes, direct current of reverse polarity is recommended.
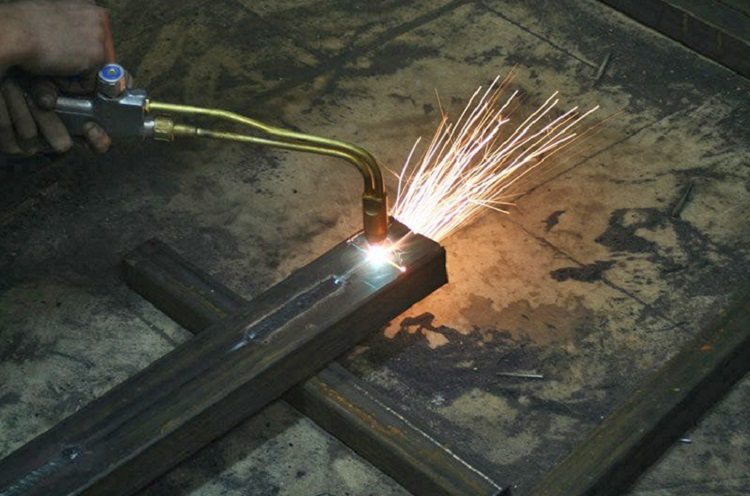
Gas welding is used mainly in industrial facilities and it requires experience in conducting such work from the master
Welding is accompanied by the formation of slag, the presence of which reduces the strength of the seam. Therefore, it should be periodically knocked down. The seam cleaning is performed after it cools down. Places heated to high temperature rust faster. This factor makes it necessary to treat the seam with its subsequent coating with an anticorrosive layer.
Gas welding. The welded construction requires surface cleaning and fixing. If the wall thickness exceeds 5 millimeters, the beveling of the edges is performed. The flux layer applied to the surface creates a film that protects against oxidation and contributes to a more durable weld. Under the action of a high combustion temperature, supported by a mixture of oxygen and acetylene, the metal melts and fills the gap.
Good to know! Due to its high cost, this technology is less common compared to electric arc welding. In addition, according to safety standards, only professionally trained gas welders with special clearance should work with gas equipment.
Improve the quality of the seam allows a special additive. Welding of thin-walled pipes is carried out using the “right-to-left” method: the torch moves after the filler rod. Its uniform melting in combination with the same melting of the edges allows you to form a neat and reliable seam.
Thick-walled profile pipes are connected “from left to right”: the burner goes ahead of the additive. The cooled seam needs refinement. At each stage, a geometry check is performed, and the detected distortions are aligned. Gas welding is indispensable in the absence of a power source.
Contact welding. In everyday life, this method was not widely used and is practiced only by professionals. Its use is advisable in places where special equipment is installed. This complex welding is carried out due to the transmission of electric current with simultaneous pressure of the electrodes on the part. Additives are not used in this process. The edges are welded reliably and form a permanent connection due to compression and a short-term increase in temperature from the flow of current.
Invertor welding. This type of welding deserves a separate discussion.An inverter is an apparatus that performs a series of transformations of the electrical parameters of a network. As a result, an alternating current is formed at its output.
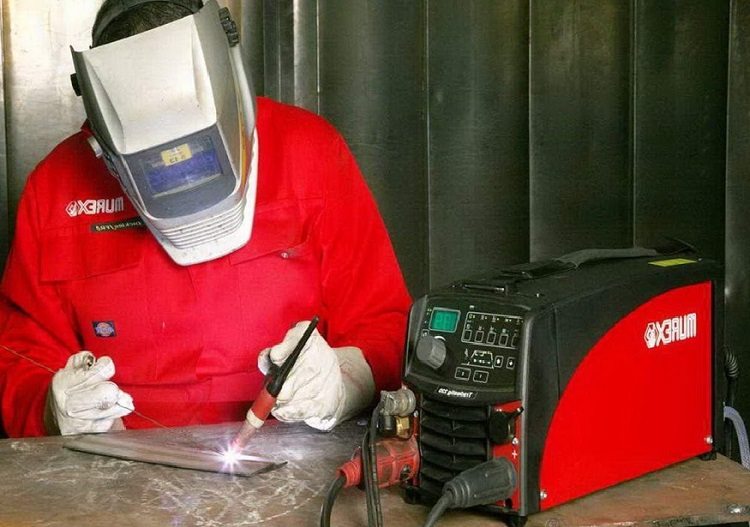
Inverter welding machine is easy to handle and high quality weld, it is easy to master and a novice welder
High quality seams and compactness - this is what distinguishes this unit from the usual welding machine. Continuing the comparison, it should be noted that the inverter circuitry prevents the sticking of electrodes, which is often observed during the operation of traditional transformer equipment. The design of this unit consists of the following units:
- network rectifier;
- surge protector;
- frequency converter;
- welding transformer;
- power rectifier;
- control systems.
The principle of the inverter is to double the voltage conversion of the external network. Initially, an alternating current of 220 Volts / 50 Hertz is transformed into direct current. For the final smoothing of its parameters, a special filter is used. Further, the inverter converts direct current into alternating current with high stabilization of amplitude (220 Volts) and frequency (50-60 Hertz).
Helpful information! The advantage of the double conversion circuit, which at first glance seems too cumbersome, is that a transformer with small dimensions and light weight can perform a reduction in the voltage of the high-frequency current.
For example, when welding with a current strength of 160 amperes, an 18-kilogram transformer will be required for units of the old model, while a voltage converter weighing about 0.250 kg is used for inverter welding.
Features of inverter welding
Ease and convenience in work are one of the main advantages of this equipment. The combination of these properties allows welding of profile pipes by an inverter even to an inexperienced welder. But still, knowledge of the features of this procedure does not hurt.
The exclusion of the sticking of the electrodes was mentioned above. For this reason, the vertical seam in inverter welding is better and faster. There are other features of using this type of equipment.
So, for example, when working with a traditional welding unit, the quality of the seam depends on the degree of stability of the combustion of the electric arc. Providing this parameter is beyond the power of every novice welder. The constancy of the welding current of the inverter equipment makes the issue of monitoring this function irrelevant.
In traditional transformer welding units, there is a relationship between input and output voltage. Thus, with significant differences in the external network, problems with ignition of the arc can occur. The inverter circuitry completely eliminates this dependence.
One of the varieties of equipment of this type is a semiautomatic welding device. The filler wire with which the seam is formed is fed into the arc burning zone automatically.
In conclusion, it should be noted that universal inverters are very popular in private workshops and car services.