Metal pipes, despite the widest distribution of polymeric materials, continue to be in demand. Metals are used for the manufacture of parts and assemblies in devices, mechanisms and assemblies. Construction is interested in load-bearing metal structures. Insulation and reinforcement, transportation of various gaseous, liquid and granular substances require the use of metals.
Content
Steel pipes: classification, advantages and disadvantages, scope
Steel pipe products are classified according to a number of characteristics, for example, according to a specific technical characteristic that determines consumer qualities:
- manufacturing method;
- the presence of perforation;
- wall thickness;
- diameter (internal section);
- external coating.
According to the manufacturing method, steel pipe products are distinguished:
- seamless (hot and cold formed);
- welded (water and gas, straight and spiral);
- soldered.
According to the wall thickness of the product refer to:
- thin-walled;
- normal
- thick-walled.
Metal pipelines made of steel in the form of a section are:
- teardrop-shaped;
- square;
- round;
- oval;
- rectangular;
- Hex.
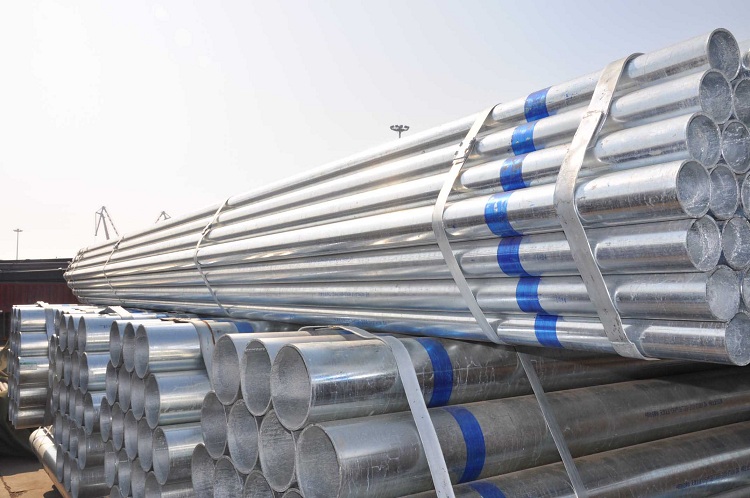
Steel pipes can have different cross-sectional areas, the most widely used are ordinary round products
Based on the presence of an external anti-corrosion coating, steel products can be attributed to:
- un galvanized;
- galvanized;
- chrome plated etc.
Good to know! The use of anti-corrosion coating can significantly extend the life of pipes in any conditions.
Highlighting the advantages of steel pipelines, they are characterized by:
- high resistance to mechanical stress;
- high coefficient of thermal conductivity;
- a sufficiently long period of operation, reaching up to fifteen years.
- low coefficient of linear expansion, which allows them to be used in heating systems;
- ability to withstand high pressure and temperature of the working environment;
- breadth of assortment.
Corrugated steel pipes combine the advantages inherent in steel with newfound ones, characterized by:
- flexibility and ductility;
- resistance to mechanical influences from the outside and from the inside. Successfully cope with a working pressure of 40 atm and above;
- frost resistance;
- the smoothness of the inner walls, excluding siltation, the formation of mold and fungi;
- simplicity of installation and the possibility of hidden installation;
- environmental friendliness.
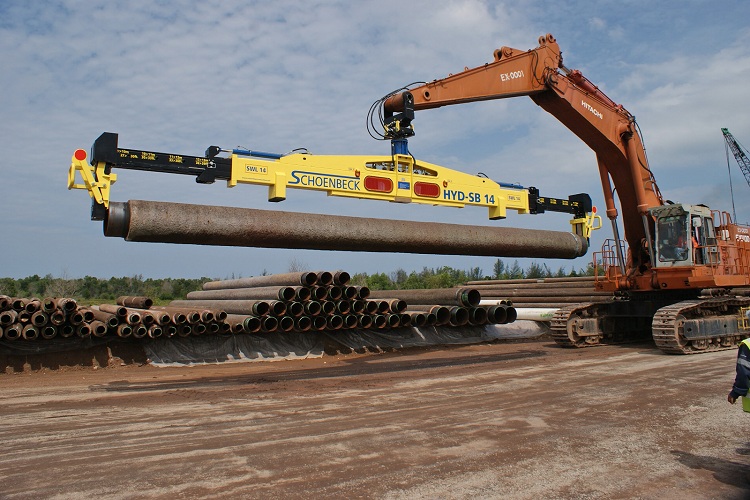
A significant drawback of steel pipes is their weight - equipment is needed to work with such products
The reliability of steel structures is associated with a number of disadvantages:
- abrasive wear;
- heavy weight, which makes it difficult to transport and carry out any work;
- high cost and significant costs for installation, maintenance and repair;
- low frost resistance;
- susceptibility to corrosion;
- roughness and a tendency to accumulation of sediments, significantly reducing the throughput of pipelines.
Note! It is not possible to cover and describe in detail all areas of application of steel pipes. These products are used almost everywhere.
In its most general form, we can talk about two main areas of application:
- For transportation. Air and gases, water, steam and various liquids, bulk solids move through pipelines made of steel.
- In the form of metal structures. Profile products are in demand in this area.
Cast iron pipes: general properties, application of the range of cast iron products
Pig-iron products are made of gray or high-strength metal, which significantly affects their properties. Cast iron as a material is characterized by:
- long term of operation;
- sufficient frost resistance (up to - 60º C);
- non-susceptibility to damage;
- fire safety;
- strength;
- low coefficient of stretching;
- soundproofed.
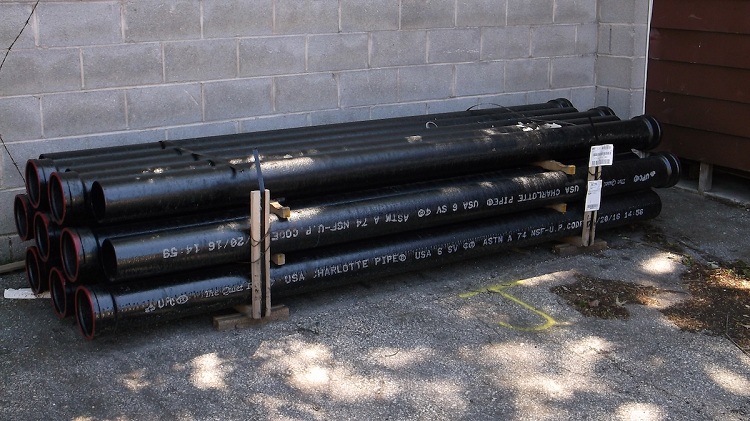
The characteristics of cast-iron pipes make it possible to use them in almost all domestic and industrial facilities
Different types of cast-iron products have inherent qualities that are noticeably different from others, which determines the scope of their application.
Pressure pipes VChShG found application in:
- drilling rigs;
- water mains;
- gas and oil pipelines;
- sewer pipelines, especially at large facilities;
- pipelines with a high pressure of the working medium (up to 1.8 MPa).
Such a wide distribution of products from ductile iron made possible by:
- high elasticity and bending strength;
- resistance to corrosion, cracking and impact loads.
Non-pressure cast-iron sewer pipes are inferior in strength to products from ductile iron, not withstanding significant loads. They find application in small objects. On the one hand, a bell-shaped PMC ends with a special extension for connection. It is used when laying sewers along with polymer pipes.
Socketless SML from cast iron containing a significant proportion of graphite. For manufacturing, centrifugal casting is used.
Important! The inner surface of the SLM pipes is equipped with an epoxy coating that prevents the formation of deposits and performs a protective function. These products are used for pumping aggressive liquids and solutions.
Describing the operational capabilities of socketless cast iron SML pipes, special attention is paid to:
- strength;
- wear resistance;
- fire resistance, incombustibility;
- sound insulation;
- resistance to corrosion and aggressive chemical environments;
- ability to tolerate a sufficiently high temperature;
- simplicity of connections with clamps.
Socketless cast iron SML products are used for the arrangement of wastewater and sewage:
- housing stock;
- production facilities;
- facilities with high requirements for noise and fire safety (educational institutions, health facilities, boarding houses and hotels).
Cast iron pressure bell-shaped products, distinguished by their non-susceptibility to rust formation and the ability to withstand a working pressure of 16 atm, are designed for fifty years of operation. To prevent the occurrence of corrosion, they are coated with varnish-bitumen compositions, which contributes to an even longer service life. The PRC products are laid both on the surface and underground, equipping plumbing and sewer networks at industrial facilities.
Finned economizer cast-iron pipes for heating systems are in demand at industrial facilities and in residential buildings, where their shortcomings are not significant:
- significant weight;
- tendency to accumulate dust in the intercostal space;
- low stability relative to mechanical stress.
These shortcomings more than overlap:
- extremely long service life exceeding a century;
- corrosion resistance of both internal and external surfaces;
- high thermal conductivity combined with long-term heat retention;
- relatively low cost.
Pipes from aluminum and aluminum melts
They are used by a number of industries - chemical and petrochemical, aircraft and shipbuilding, construction.
According to the method of manufacturing pipes from aluminum and alloys there are:
- pressed;
- welded straight-seam;
- cold-deformed.
Section shape can be:
- square;
- round;
- rectangular;
- shaped.
Along the length of aluminum pipes are produced:
- measured;
- unmeasured;
- multiple dimensional.
As of manufacture:
- hardened and aged naturally;
- hardened and aged artificially;
- skipped;
- cured after hardening and naturally aged;
- annealed.
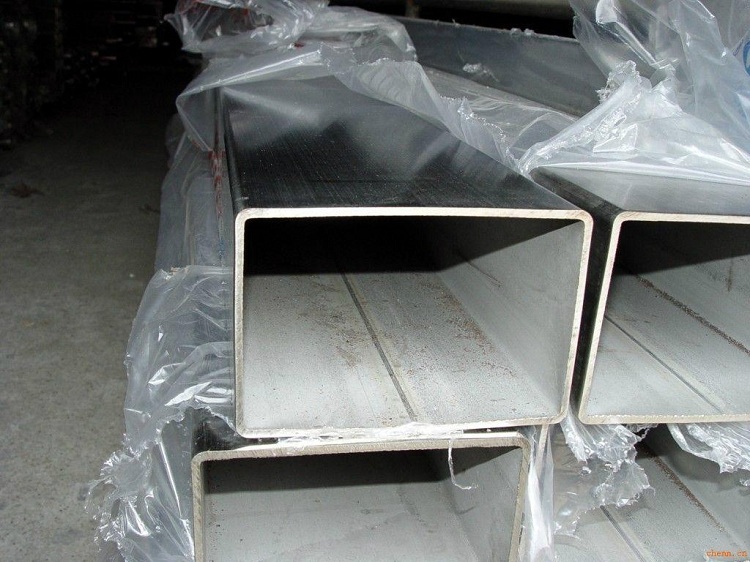
Profile pipes made of aluminum and alloys are used as the basis for structures that must be strong, but lightweight
Note! The most popular alloy obtained with the addition of copper, manganese and magnesium is duralumin. To protect against corrosion, the duralumin tube is coated with pure aluminum, turning the service life into almost unlimited.
Pipes from copper and alloys based on it
Copper plumbing products that meet international standards are made of phosphorus deoxidized metal. Copper pipes are supplied as:
- lengths of several meters (unannealed);
- tens of bays (annealed, i.e., past special heat treatment, giving softness and decreasing strength).
The arrangement of a copper water system allows you to get a long list of significant advantages:
- high level of antibacterial and antiviral protection;
- impermeability to harmful substances;
- non-susceptibility to the formation of deposits from organic and inorganic both on the inner surface and on the outer;
- if there is chlorine in the water on the inner surface of the products after an hour-long operation, an additional strong protective film is formed;
- low coefficient of thermal expansion;
- resistance to temperature changes in the range from - 200º С to + 250º С. You can safely forget about the danger of frost for a water supply system;
- plastic;
- resistance to ultraviolet radiation;
- the roughness coefficient provides a throughput exceeding the capabilities of polymeric materials;
- durability (service life exceeds fifty years);
- corrosion resistance.
Bronze and brass pipes, due to their high cost, are used in technical devices and installations, where their high performance makes it possible to neglect the price factor, less often in the domestic sphere.
The assortment of metal pipes is extremely large, and it continues to grow, as new alloys with unique advantages constantly appear.