The laying of most communications is not complete without electric-welded galvanized pipes, characterized by a corrosion-resistant coating. Many standards have been developed for the production of metal products of a similar pattern, so that each of them meets all the technical requirements and the expected workload. An electric-welded thin-walled pipe, in the presence of a protective layer, will last about one and a half times longer than similar communications made of ordinary metal. This is what makes the most popular among construction companies and home masters of water pipes with galvanized coating.
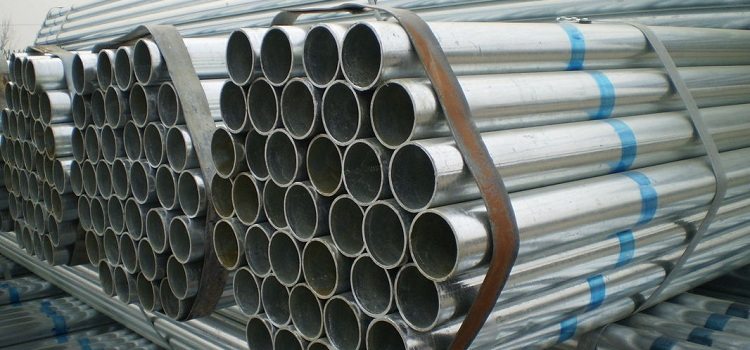
Galvanized pipes are resistant to corrosion, therefore their service life is longer than that of ordinary steel pipes
Content
Characteristics of electric-welded galvanized pipes
The name "galvanized electric-welded pipe" confirms that when molding products from rolled metal, welding of the seam and galvanization of the outer and inner layers are used.
The most convenient method for joining seams of metal products is electric welding. Such products are quite reliable during operation, and the seam itself is checked by a special scanner. The connected edges of the products are securely welded, which guarantees resistance to external loads and internal pressure of the transported medium.
There is an extensive demand for products in the following areas:
- laying all kinds of communications, including heating, sewage and water supply systems;
- the construction of metal structures and bases for hangars and awnings;
- arrangement of outdoor advertising (banners, billboards, billboards);
- transportation of liquid media in various fields of the chemical and oil industries.
Welding and forming pipes el \ welded are governed by the requirements:
- GOST 10705-80;
- GOST 10704-91;
- GOST 10705-91.
According to this standardization, the dimensions of galvanized products with a straight seam vary between 10 mm - 530 mm, and their assortment is indicated in the GOST tables.
Attention! The same GOSTs apply to galvanized pipes as to products from ordinary ferrous metal, TUs of pipe production comply with GOST 10705, the assortment and maximum deviations are in accordance with GOST 10704.
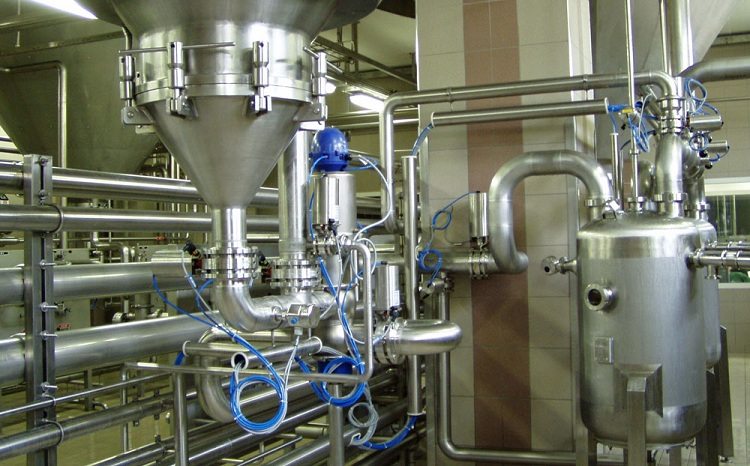
The properties of galvanized pipes allow them to be used to transport various aggressive liquids, for example, in the chemical industry
Production of galvanized pipes
When producing electric-welded galvanized pipes, low-alloy steel is most often used, supplemented with an admixture of manganese and chromium in a small amount. For ordinary communications, their content ranges from 2.5%, and with increased load - up to 10%. An increase in the content of other metals increases the strength of the gas pipeline, where internal pressure is possible up to 16 MPa.
To increase the strength of electric-welded products and extend their life, not only galvanization is used, but also coated with bitumen and polymers. The combination of alloying components, sufficient wall thickness and reliable welding put these pipes among the most durable solid metal products. To increase the life of the pipe, the electric-welded pipes are coated with a thin layer of galvanization, which does not exceed 35-40 microns.This increases corrosion protection and improves the quality of water flowing through pipes - the presence of rust is reduced to a minimum.
The surface treatment of pipes by the composition of zinc is produced by 5 methods:
- Cold galvanized (similar to staining).
- Hot coating method (deposition).
- Thermal diffusion galvanizing.
- Galvanic application.
- Thermal spraying of zinc.
How long the anti-corrosion coating will last depends on the zinc layer and its density. The choice of method is directly related to the diameter of the workpiece and the further functionality of the pipeline.
Cold galvanizing is the most common, as it is the most affordable way to apply a corrosion-resistant coating. Electro-welded galvanized tubing is treated with a specialized primer based on zinc powder. However, this application is not highly resistant to mechanical stress. When processing pipes, it is imperative to comply with safety procedures due to the harm of solvents containing highly dispersed zinc. Processing of products in several layers increases the service life of highways. Apply the product under normal conditions for construction work. The proportion of powder and primer varies from 1: 1 to 3: 1.
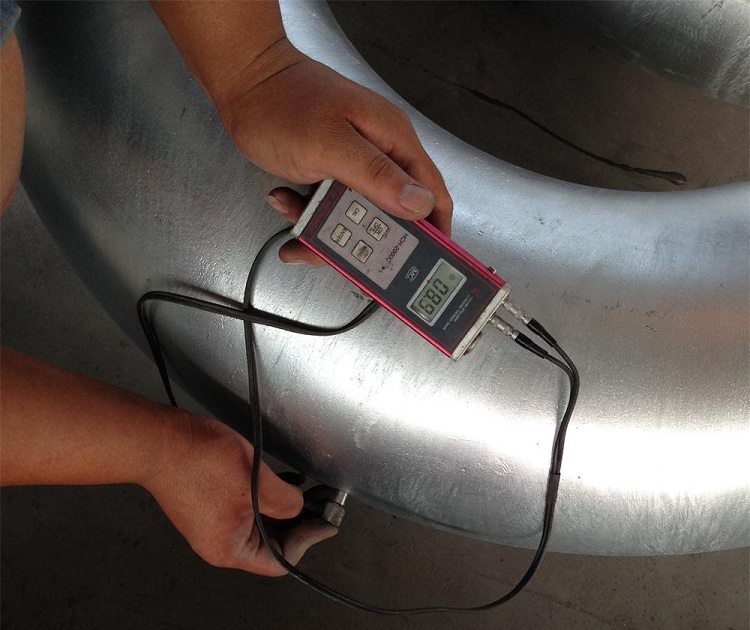
Regardless of the method of applying the zinc layer, its thickness should not exceed the standards established by GOST
Hot-dip galvanized products are also in great demand, and in pipe production such processing remains the leading one. But the method is classified as conditionally harmful production due to the chemical treatment of molten zinc at temperatures up to 4800 ° C. The method requires significant energy costs, therefore, cannot be economical. Dry metal products (most often pipe fittings and wire for construction work) are immersed in a container with hot zinc alloy, designed to protect them from rust.
Thermal diffusion galvanization (TDS) has been used for at least a century - it was developed in Britain at the beginning of the twentieth century. Over time, it was replaced by more advanced methods of metal processing, but it was not removed from the production of hardware. The essence of the technology is to obtain a protective layer on the metal surface using the deposition of zinc atoms at rates above 4500 ° C. The resulting alloy of iron and zinc is quite reliable, it is controlled by GOST R 51163-98 and other technical standardization (ASTM B633 and ASTM B695). The coating layer depends on the processing time, its important advantage is the penetration into the thread or holes of fittings for products of complex configuration.
Galvanic galvanizing is an interesting process involving water and electrodes, known to many from school physics lessons. The electrochemical method is used for most metals and other materials that are difficult to cover with a protective layer according to another formulation. The main advantage is the aesthetic appearance of products that are smooth and shiny. It is not used for ordinary products, but the taps, valves and faucets of high quality used in apartments and private houses do just that.
Thermal spraying of zinc is carried out in a high pressure gas stream, which allows you to process a large volume of pipes of large diameter. A coating forms, somewhat reminiscent of flakes of lighter metal on the surface of products. Pipes often receive additional anti-corrosion treatment in order to use comprehensive protection of communications laid in difficult climatic and environmental conditions. Products with such protection are applicable even in environments in contact with seawater and chemicals.
The main range of galvanized electric-welded pipes: selection criteria
In the production of welded products from strip (sheet metal) 3 methods are used:
- hot rolled;
- cold deformation;
- hot-rolled;
- electrowelded (straight-seam and spiral-seam).
Electric welded billets made of carbon steel grades 15XM (10, 20, 35 and 45) are produced in this denomination:
- round electric pipe;
- profiled square products;
- flat oval pipes;
- rectangular electric-welded pipes (rectangular section).
According to the purpose (functionality) of the product are classified:
- general purpose;
- special purpose.
Important! Conventional electric-welded galvanized pipes are applicable on not-so-critical communications sections or in structures with a slight load.
When calculating the batch weight, such indicators as wall thickness, running meter (measured and unmeasured length) and diameter are taken into account. The coefficient K = 1.03 is used, since the weight of galvanized pipes increases slightly, the standard is about 76x3.5 - 6.45 kg / linear meter.
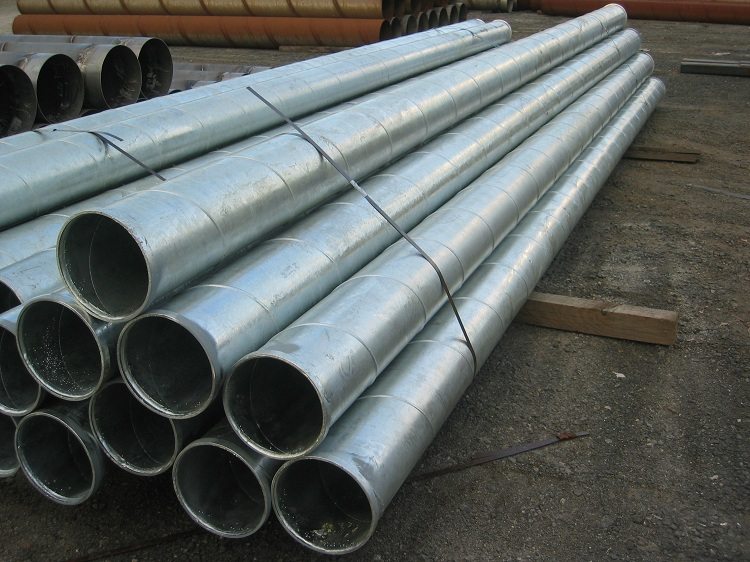
Electric-welded pipes come in two types - straight and helical; the second type is considered more reliable
The assortment is taken into account:
- especially thin-walled;
- thin-walled;
- thick-walled;
- especially thick-walled.
Electric-welded water and gas pipes are regulated by GOST standards:
- Resistant to corrosion (11068-81).
- Electric-welded straight-seam (10704-91).
- Steel square section (8642-68).
- Welded rectangular (25577-83 and TU 14-105-568-93).
- Oval (8642-68).
- Flat oval (8644-68).
Electric-welded galvanized straight-seam pipes are available in 5 different classes, depending on the scope:
1st class - laying of water and gas pipelines, heating systems, as well as external structures of pipes and shaped metal.
2nd class - oil pipeline or gas pipeline, high pressure pipeline (hydraulic and chemical enterprises).
3rd class - in communications with increased thermal stress (chemical industry, food industry).
4th class - car building and heavy machine building, high-load building frames.
5th grade - products of an unmeasured dyne for a special order.
All these parameters are taken into account when choosing and ordering customers of longitudinal welded galvanized pipes for their field of application. The volume of the batch is discussed with managers, and the availability of the assortment is checked according to the tables.