One of the main tasks that determine the quality of the pipeline from pipes with polyurethane foam insulation is the correct installation of joints. Such products go on sale with uninsulated cuts on both sides, which is necessary for ease of connection. If all work is carried out correctly, the pipeline will be reliably protected from the aggressive effects of the environment and will demonstrate a maximum service life.
Content
What is the insulation of pipe joints?
The final stage of the pipeline construction, namely the insulation of pipe joints, occurs when an insulating material - polyurethane foam - is placed in the entire open area. PPU is also used to isolate the remaining length of the structure, insulation is applied in the factory.
There are two joint filling technologies:
- Filling joints with liquid polyurethane foam.
- Installation of polyurethane shells or couplings.
Both the first and second methods can be called practical and effective. Among the advantages of shells, the following qualities can be distinguished:
- many manufacturers produce shells with various thicknesses, which allows you to choose the optimal thermal insulation for a specific climate zone. Reinforced insulation will be effective even at temperatures dropping beyond -100 degrees;
- it is the polyurethane foam type of insulation that is used most often, since this polymer is characterized by increased resistance to moisture, pressure and mechanical damage;
- when using a polyurethane shell produced in a factory, the risk of uneven filling of the liquid polymer disappears. And insulation vulnerabilities lead to premature corrosion of steel pipe under the polymer layer.
At the same time, the technology of pouring liquid polyurethane foam remains competitive and provides high adhesion to existing insulation layers.
Materials for sealing pipe joints in polyurethane foam insulation
After connecting the PUF pipes, all joints should be insulated. An important issue is the sealing of the coupling to the steel pipe. The best method of protecting the fasteners is the use of adhesive adhesive applicators, ensuring uniformity of construction and high thermal insulation performance.
Important! The kit for insulation of the joints of pipes PPU also varies depending on the type of shell of the product. For PUF pipes with galvanized shell, a casing of the appropriate material is used to protect the joint.
To seal joints, you need a list of the following tools and materials:
- heat shrink sleeve;
- metal brush;
- solvent;
- propane burner;
- permanent marker;
- drill with a diameter of 25 mm;
- adhesive tape;
- clutch crimping apparatus;
- drainage and welded plugs;
- liquid foam.
Materials for filling bare joints are not only a direct configuration. To create turns and angles, shaped products are provided: tee branches, adapters, Z-shaped elements, bends, supports, etc.
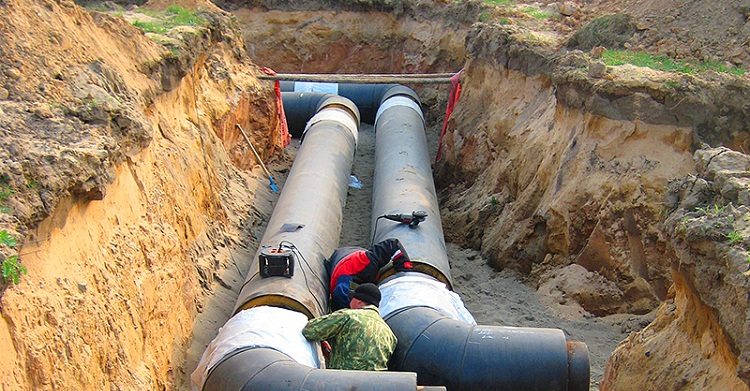
During the construction of heating mains, not only straight pipe sections are used, but also various shaped parts; their joints also require careful isolation
Installation of joints of PPU pipes
The application of a heat-shrinkable sleeve is the main stage when conducting high-quality thermal insulation. Insulation of joints on already installed PPU pipes is carried out in the following order:
- The ends of the thermal insulation are cleaned, and the surface of the galvanized or polyethylene shell is cleaned of dirt with a brush, if necessary, washed, and then dried with a gas burner. This step is necessary in order to move the shrink sleeve over a completely clean surface. To clean the surface is at a distance not less than the length of the prepared coupling. If there are any formations on the inner steel pipe, including rust, they should be brushed off with a wire brush.
- The insulation layer under the protective shell must be smoothed to a depth of 15-20 mm. Remote control wires are connected, control measurements are carried out according to the relevant instructions.
- The surface of the polyethylene sheath is degreased on both sides of the joint. The solvent should be treated with a surface at a distance of 150-200 mm from the edge. After the initial solvent treatment, the polyethylene is cleaned with sandpaper, then processed again.
- Next, the position of the coupling is marked along the axis of the joint. With a permanent white marker, marks are applied to the surface corresponding to the edges of the coupling. Prepared, cleaned and degreased surfaces should extend 20-50 mm beyond the intended edges of the coupling. Chalk should not be used for marking.
- The shrink sleeve is unpacked so that the outer part of the packaging film is located on the surface of the shell of the PUF pipe. No substances must enter the inside of the coupling. If liquid or dirt gets on the coupling, its inside is degreased, cleaned and degreased again.
- A hole with a diameter of 25 mm is drilled at a distance of 150 mm from any edge of the coupling.
- The surfaces of the shells at the junction, prepared for insulation, are heated by a propane burner to a temperature of + 30-50 degrees. While the surface remains warm, a flexible mastic tape with an indent of 10-15 mm from the edges is glued to it. After making sure that the adhesive tape is fixed tightly, you can remove the protective film from it. Particles of dirt and dust on unprotected tape are not allowed.
- The sleeve is put on the pipeline section in accordance with the set marks. The edges shrink when heated by the burner: it should be heated in circular smooth movements. It is impossible to overheat the coupling, the appearance of gloss on the surface testifies to it. With proper shrinkage, the coupling will follow the contour of the shell, the surfaces will fit snugly, without raising the edges. The shape of the finished coupling is barrel-shaped.
- After the coupling cools down, pressure testing is performed to ensure additional tightness.
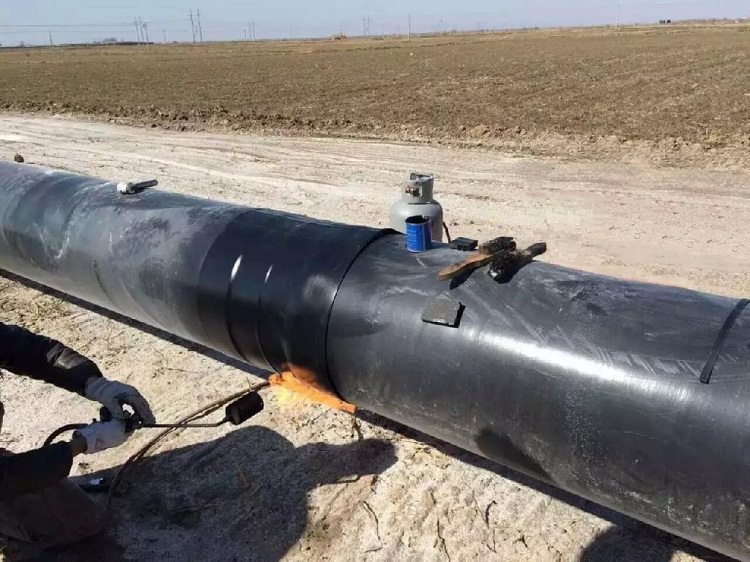
Working with a heat-shrink sleeve requires heating the polyethylene to a sufficient temperature, this operation is performed by a gas burner
Important! If the air temperature at the time of the work is lower than 0 degrees, a gas burner passes at a distance of 30 cm from the shell surface to warm the polyethylene to a temperature of + 30-50 degrees.
After testing, it is required to drill a second hole at a distance of 150 mm from the other end of the coupling. PPU in liquid form, previously diluted from two components in a clean container, will be poured into these holes. Upon completion of the thermal insulation with foam, the holes are clogged with drainage plugs until the solution solidifies.
The final phase of work on insulation will be the removal of drainage plugs and cleaning the surface of the coupling from excess PUF. Holes are machined with a conical cutter.The holes are welded with plastic plugs at a temperature of +240 degrees.
The shell mounting method is used if filling is not possible for some reason. Their fixation is achieved using longitudinal or transverse locks. After conducting any type of insulation of the joints, the operation of the system is possible only with a successfully completed integrity check of the wires.