Polypropylene water pipes widely used for installation of water supply systems, both cold and hot. They have a long service life, are environmentally friendly, are characterized by low hydraulic resistance and resistance to the formation of growths on the inner surface. Such pipes are durable and resistant to corrosion, and welds are of high quality and tightness.
Content
Features of the choice of polypropylene pipes
The choice of elements of the water supply system is based on the conditions of their operation, temperature conditions and operating pressure. There are several varieties of polypropylene pipes for water supply: single-layer and multi-layer, with an aluminum or fiberglass layer. Product specifications are reflected in the marking:
- PN25 - most commonly used in heating systems.
- PN20 - pipes for heating and hot water.
- PN16 - for hot and cold water supply.
- PN10 - for cold water systems.
If the temperature of the passing liquid is more than 90 ° C, then polypropylene pipes with the markings PN20 and PN25 are used to install the water pipe with their own hands. Their structure includes a reinforcing aluminum or fiberglass layer: blue corresponds to cold water, red to hot.
For systems up to 10 m long, PP pipes with a diameter of 20 mm, 10-30 m long - 25 mm, more than 30 m - 32 mm are used. If the water supply network requires a riser, then its diameter should be 32 mm.
For installation of water pipes from polypropylene pipes It is important to choose high-quality products on which there should be no influx and roughness.
Single and multi-layer products
Single-layer polypropylene pipes are represented by such types: PPH, PPB, PPR and PPs. PPH pipes are made of homopolypropylene and are used in cold water supply, ventilation and industrial pipelines. For underfloor heating systems and the production of impact-resistant pipes and fittings type of PPV is used. PPR pipes are made from a special type of polypropylene, which can evenly distribute the load on the pipe wall.
Note! When PPR pipes are open, products must be protected from ultraviolet rays by a special sheath.
The type of PPs pipe is made from a non-flammable material that has a maximum working temperature of 95 degrees.
Multilayer reinforced pipes have lower temperature elongations than single-layer ones. Products that are reinforced with aluminum foil are smooth and perforated. Perforation has the form of a grid with small holes. Before welding into the socket, the outer polymer layer and the aluminum shell are removed with a special tool.
Piping Options
The first step in installing PP pipes for a water supply system is to draw up a detailed diagram of the wiring, fastening and connection of pipes. Unnecessary details and bends should be avoided.
There are two ways to organize the installation of polypropylene water pipes - open and closed. The second option is more complicated and requires accurate calculation and execution. In this case, the number of joints is minimized, and access to junctions is organized.
The advantages of open type wiring are ease of installation, ease of maintenance, the ability to replace parts of the system if necessary.
The piping is serial (tee) and parallel (collector). With serial wiring, the installation of a water pipe from polypropylene pipes with your own hands is carried out from the main highway to the places of water consumption. From the main riser pipelines of cold and hot water. Tees are used to divert to water-consuming points.
Along with ease of installation and material saving, such a system has a drawback - when repairing one device or a consumer, it is necessary to disconnect the entire network.
The collector system has one input with several pins. Consumption points are independent, but this increases the labor and installation costs.
Mounting Hardware
To install a pipeline from polypropylene pipes, you will need a machine with nozzles for welding plastic pipes, a puncher, a grinder, a device for cutting products and chamfering. In addition, an adjustable wrench, level and elbow, sealing material required for a threaded connection may be required.
Nozzles do not always come with a welding machine. They come in different diameters corresponding to pipes and fittings: 1.6; 2.0; 2.5; 3.2 cm, etc.
Polypropylene pipes are cut with special scissors, but in the case of a small amount of work, you can use a conventional hacksaw for wood.
Important! Regardless of the tool used, the cut should be most perpendicular to the axis of the pipe.
Permissible deviations from perpendicularity are given in the table.
Table 1
Pipe diameter, cm | Tolerance, mm |
20 | 8 |
16 | 7 |
12,5 | 6 |
11 | 5 |
9 | 4 |
6,3 | 3 |
4 | 2 |
3,2 | 2 |
2 | 2 |
When installing a water supply system, it is important to comply with safety requirements. Work with a grinder or other cutting tools should be carried out in safety glasses. During wall gating or welding, a respirator must be worn.
Necessary auxiliary elements of the system
When performing installation work, not only polypropylene pipes for water supply are required. Couplings, corners, bends, tees, plugs, crosspieces, clips and clamps may also be needed. A previously created pipeline scheme will help to acquire the required number of elements. When choosing it is important to consider their sizes, diameters and other characteristics. Better pick fitting one manufacturer, the same as the PP pipe.
Couplings are used to connect straight pipe sections or when switching to products of a different diameter. With the help of corners, you can organize obstacle avoidance and the installation of the pipeline under the necessary slope. Crosses are used at the points of cross-connection of system elements.
Helpful advice! It is recommended that you turn the inside corner of the hot water pipeline at a distance of about 30-40 mm from the wall.
Reliable fastening PP pipes to the wall made by clips, fixing the riser - metal clamps with gaskets made of rubber. Their connected ends are bolted with nuts to increase rigidity. Clips can be used both on straight sections and in corner joints. If the pipelines are located one above the other, then there are double clips for their fixation.
Welding connection of polypropylene pipes
Before starting work on PP pipe welding nozzles of the required diameter with Teflon spraying are put on the welding machine, the temperature regulator is set at 260 ° C, the device turns on and heats up. The process is carried out in stages.
First, marking is applied to the pipe, along which it is cut into pieces of suitable length. The ends to be joined are stripped. For stripping pp pipes sandpaper or a special tool can be used. The marker indicates the depth of entry of the pipe into the fitting. A gap of 1 mm must remain between the polypropylene pipe and the fitting.
A fitting with a pipe is placed on the heated nozzle of the device, the heating of which should begin simultaneously. The exposure of parts depends on their diameter.
table 2
Diameter cm | Time s | |
reflow | cooling | |
1,6 | 5 | 120 |
2,0 | 5 | |
2,5 | 7 | |
3,2 | 8 | 240 |
4,0 | 12 | |
5,0 | 18 | |
6,3 | 24 | 360 |
7,5 | 30 | |
9,0 | 40 | |
11,0 | 50 | 480 |
Further, the parts are pushed onto each other without turning in an axial line. The solidification of the joint also depends on the diameter. In this case, the parts to be welded must be fixed. At the last stage, the presence of gaps and gaps is checked.
For polypropylene pipes, the welding machine is quite expensive, so if necessary it is better to rent it.
Steps for installing a water supply system
Before starting the installation of new pipes, the water supply is shut off and the old system is dismantled. The room is freed from equipment and materials that are not useful during work.
Pipes are cut into pieces of the required size, and the chamfer is removed on the upper part of their ends. According to German DVS standards, its angle should be 15 degrees, and the recess should be up to 3 mm. The state standard regulates a depth equal to 1/3 of the thickness of the pipe and a slope of 45 degrees.
Note! When installing a water supply system, separate branches are first assembled. They are subsequently combined into a single system.
Then the ends of the pipe are cleaned of dirt and degreased. Using welding equipment for polypropylene pipes, it is connected to the fitting. In this process, it is important not to overheat the parts, since their melting and deformation will not allow further connection.
Using clips, pipes are attached to the walls. On flat areas between adjacent parts, the distance should not exceed 1 m. Elements of equipment and fittings are fixed rigidly with clamps. Sealing of compounds is carried out with a fum tape.
Possible errors in the performance of work
If the polypropylene pipe is not fully inserted into the fitting when they are combined, a certain gap remains between the inner part of the fitting and the pipe end. In the finished pipeline, this place is a section with a larger inner diameter and a smaller wall thickness than the primary pipe.
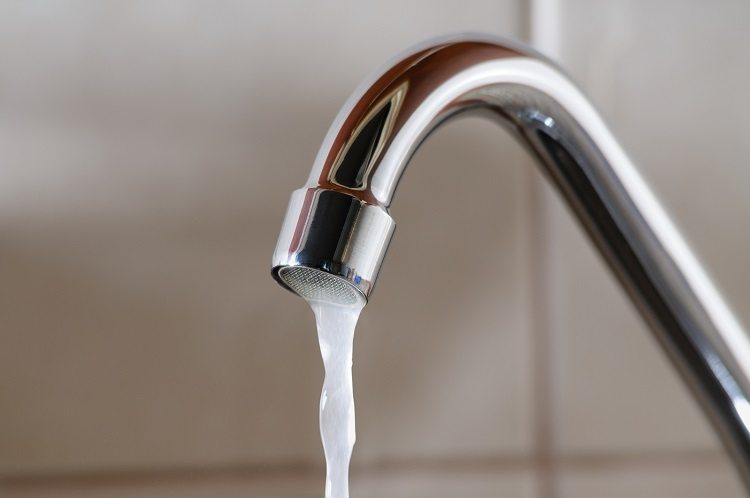
In improperly mounted pipes, the pressure will be low, and the pressure of the water in the tap will be low
For this reason, the operational design pressure of such a section will be lower than that of the rest of the pipeline.
Also important is the force with which the polypropylene pipe and fitting are combined when heated. If it is used excessively, large grata is squeezed out between the end of the pipe and the inside of the fitting. This creates an obstacle to the movement of fluid in the finished plumbing system.
Before starting operation, the water supply system is checked for leaks. It is subjected to pressure that is 1.5 times higher than the nominal (however, no lower than 0.15 MPa). The system is filled with water and with the help of a pump it rises, controlling its value with a manometer. Particular attention is paid to the joints. If any joint gives a leak, then it is cut out and a new element is installed, after which the verification procedure is repeated.
Design and water pipe laying can do it yourself. Technical characteristics of polypropylene pipes make it possible to establish a high-quality system with a long service life.