Plastic has long ceased to be perceived as fragile, literally disposable material, suitable only for the production of toys and other small things. Now, modified plastic has no worse properties than metal, and sometimes it is more preferable. Large-diameter polymer pipes are used even in areas requiring increased responsibility - when laying oil and gas pipelines, heating and sewer systems.
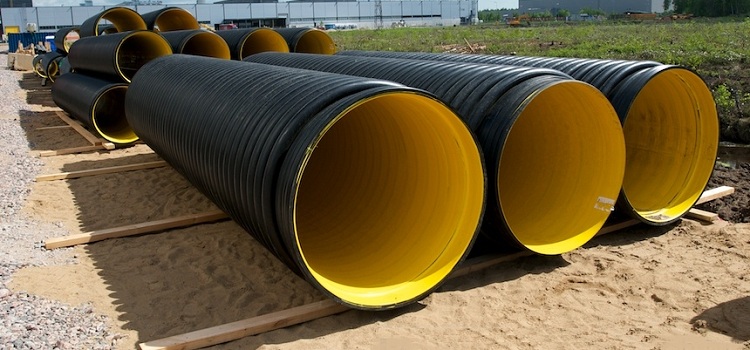
Pipes of large diameter made of polymeric materials are able to compete with steel when arranging highways of varying complexity
Content
Where are large diameter plastic pipes used?
The category of large diameter pipes includes products with the following dimensions: their diameter is from 500 to 1200 mm (there are also products with a diameter of up to 2000 mm). These varieties of plastic products gained immense popularity due to their good technical characteristics, durability and low market value. The use of large-diameter pipes has become relevant in the following areas of industry and supply:
- replacement of domestic water systems that were previously used exclusively concrete (or asbestos-cement);
- replacement and reconstruction of old cast-iron or steel water and sewer communications: in this case, polypropylene plastic pipes of large diameters are most often used, since this material guarantees the absence of deposits on the walls of the system due to its smoothness;
- supply and transportation of media under high pressure - both in domestic use (pressure systems) and in industry. Plastic pipes are widely used for transportation from oil and gas fields, even by sea: in this case, the pipeline is collected on land and then flooded;
- laying of underground utilities - thick-walled plastic is extremely durable (in this indicator, plastic significantly exceeds fragile concrete), therefore it is quite capable of withstanding soil loads;
It is interesting! Depending on what stiffness class the product belongs to, the pipeline can be immersed to a depth of 2 to 16 meters.
- installation of storm, household or drainage sewers in areas with multi-storey buildings or private buildings, in industrial zones.
Large-diameter pipelines are equally successfully used in all areas where transportation of liquids and other media in large volumes is required.
Varieties of oversized plastic pipes
Plastic pipes are classified by type of plastic. There are three types of materials from which products for plastic pipelines are made:
- PVC pipes. This category of plastic products is used only in two cases - as the basis for sewer systems and as the outer layer for waterworks.Restrictions on the use of PVC pipes are due to the fact that over time this material begins to release toxic substances.
- Polypropylene pipes. Products with sufficiently rigid walls that are resistant to temperature extremes, so they are widely used even when installing heating systems. They have soundproofing properties, and are also chemically inert to aggressive substances and acids. This quality makes them suitable for operation in large-scale sewer systems.
- Polyethylene pipes. Plastic pipe made of polyethylene tolerates low temperatures, which is why it is often used in the northern regions. When interacting with hot environments, the structure of polyethylene changes irreversibly. For the needs of heating and other areas associated with the high temperature of transported media, a modified type of polyethylene is used - PE-S, or cross-linked polyethylene.
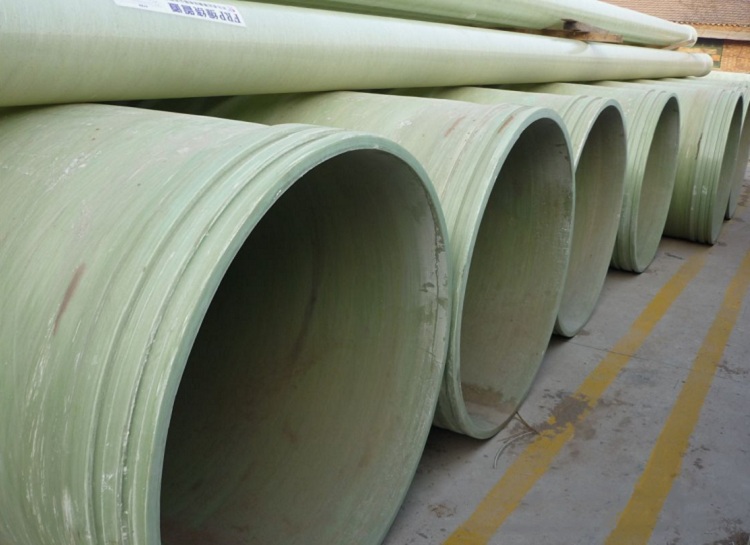
Polypropylene pipes are considered universal, they withstand heavy loads and do not require special operating conditions.
The most high-quality, reliable and versatile option among large-sized plastic pipes is polypropylene products. Sometimes polypropylene systems are reinforced, which helps to increase their service life.
The advantages of large diameter plastic pipelines
The prevalence of polymer pipes of large diameters can be explained by the presence of the following positive qualities:
Plastic does not lose its properties with constant interaction with wet environments, despite the fact that the main problem of metal products is their susceptibility to the occurrence of corrosion formations.
- a plastic pipeline can be operated without problems for as much time as concrete or metal. Some manufacturers give a guarantee for polymer products, which is about 50 years. For comparison, the warranty period of a metal pipeline is only 20-25 years;
- the heat conductivity of a large diameter plastic pipe is much lower than that of products from other materials, therefore, heat losses will be smaller;
- prices for plastic pipes are more than reasonable: depending on the diameter, stiffness class and wall thickness, the cost of one running meter of a plastic pipe can range from 20 rubles to 800 rubles;
- in the manufacture of plastics toxic substances are not used. In general, plastic pipes can be called environmentally friendly products (with the exception of polyvinyl chloride products recognized as toxic);
- almost perfectly smooth surface of the plastic, not subject to overgrowth and the formation of salt deposits and deposits. This means that the lumen of the pipe will not decrease over time, and bacteria and other harmful microorganisms will not multiply in the pipeline;
- plastic has a small weight, which simplifies and reduces the cost of transportation of large batches of pipes of large diameters.
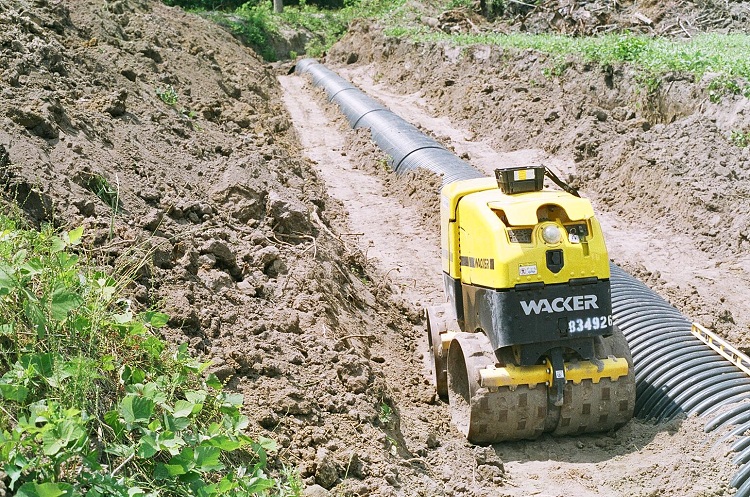
Plastic piping can be laid both underground and under water, it is able to function without fail for decades
Along with a large number of advantages, any plastic pipes have disadvantages. Among them, insufficient resistance to work in high temperature conditions. However, in recent years many improved options for plastics have been produced, capable of being used in hot water supply and heating systems.
Another difficulty is that different types of plastic require a special type of fastening (different melting points, fitting fasteners). This must be taken into account when several varieties of plastic pipes are used in the same line.
Also, when laying plastic pipelines on the ground, it should be remembered that some types of plastics gradually deteriorate under the influence of ultraviolet rays. Insulation is required for better preservation of pipelines.
Diameters and stiffness classes of bulky plastic pipes
One of the main indicators that you should rely on when choosing plastic pipes of large diameters is their stiffness class. This concept is based on acceptable the depth of the pipeline. The inner diameter of the product also depends on the stiffness class.
The assortment of oversized pipes includes the items shown in the table.
Table 1
Plastic pipe stiffness class | The maximum possible depth of laying in the ground, no more | Product Diameters |
Products for elevated pipelines | — | 500 mm, 880 mm, 1400 mm |
SN2 | 2 m | 600 mm, 900 mm, 1500 mm |
SN4 | 2-4 m | 680 mm, 970 mm, 1600 mm |
SN6 | 4-6 m | 700 mm, 1000 mm, 1800 mm |
SN8 | 6-8 m | 780 mm, 1170 mm, 2000 mm |
SN12 | 8-12 m | 800 mm, 1200 mm, 2200 mm |
SN14 | 16 m | 850 mm, 1300 mm, 2400 mm |
The choice of plastic pipes depends on the characteristics of the system. The main task of a large pipe is to withstand the maximum pressure of the transported medium. When choosing a product with an optimal diameter, information about how much medium should be transferred in the system over a certain period of time is important. Using a pipe of too small a diameter can cause a rupture of the walls of the product, and too large a decrease in pressure in the overall system.
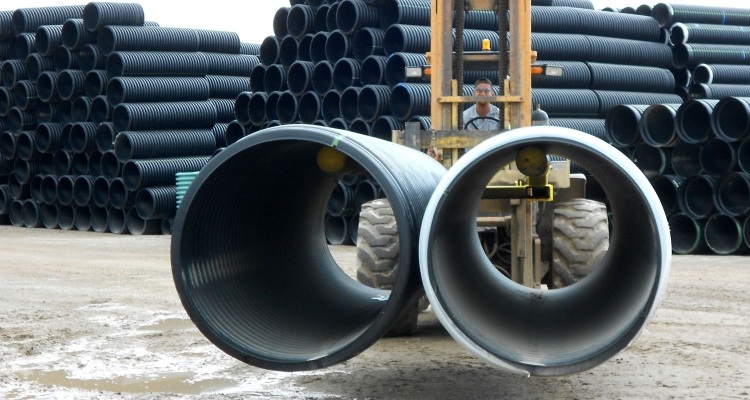
The diameter of the pipes is an important parameter on which the operability of the trunk constructed from them depends.
Another factor influencing the choice of a plastic pipe is the constant temperature in the system, since all types of plastic have different temperature limits.
How are large diameter pipes installed?
Oversized pipelines require increased strength of the joints, which is quite difficult given the large diameter of the products.
Methods of connecting pipes are divided into detachable and one-piece. The first method involves the possibility of dismantling the connection if necessary and reassembling it. With the integral method, the reuse of parts becomes impossible, the connection reaches the strength of the monolith (the deviation in strength at the junction at the junction is not more than 10%). One-piece connection most often involves welding, which is carried out using special industrial welding equipment and electrical couplings.
Important! One-piece joints are used when maximum pipe strength and minimizing any chance of leakage are required. For example, it is planned to use the system under high pressure.
Butt welding is performed according to this technology:
- The ends of the pipes are securely fixed in the welding machine.
- The sections of the segments are prepared for welding, heated using a special heating plate.
- The segments are connected, the seam location is leveled and becomes completely invisible.
Electrofusion welding is performed using fittings having an integrated heating element in their design. Thanks to this part, the plastic is uniformly melted from the inside, which ensures complete tightness of the connection.
In some cases, plug-in connections can satisfy all system requirements. They will also have a sufficient level of reliability. Removable mounting is carried out using flanges or bell-shaped parts.
The socket and flange connection method is advisable in cases where a pressureless sewer or sewage pipe is mounted.
A product such as a large diameter plastic pipe can rightly be considered the material of the future. Plastic products are gaining more and more popularity in various spheres of consumer services and industry.The properties of polymers are improved annually, therefore, perhaps within a short time, plastic will appear on sale that can become a complete replacement for heavy metals.