Laying the pipeline in the trench is one of the stages of the complex process of laying the pipeline. The success of this stage depends both on the observance of the technology during the previous operations, and on the correct choice of pipes, and taking into account their features during the installation and installation itself. Properly laid pipes in the trench is the key to the continued successful operation of the system.
Content
- 1 Classification of pipeline laying methods
- 2 The sequence of operations when laying large diameter pipes in a trench
- 3 Laying concrete, reinforced concrete and ceramic pipes in a trench
- 4 The choice of polymer pipes for home piping
- 5 The advantages of using polyethylene pipes
- 6 Installation of engineering networks with HDPE pipes
- 7 The use of welding during the installation of polypropylene pipes
- 8 Possible problems when laying polymer pipes
- 9 Pipeline insulation
Classification of pipeline laying methods
The laying process largely depends on how the pipeline system is laid. There are three main laying methods depending on the location of the pipeline:
- Aboveground.
- Underground.
- Underwater.
Laying methods are also selected depending on the impact of factors such as:
- soil structure;
- diameter of the pipeline;
- work methods;
- traffic intensity.
The combination of the above factors determines the method of laying the pipeline:
- Open.
- Hidden.
- Closed (trenchless).
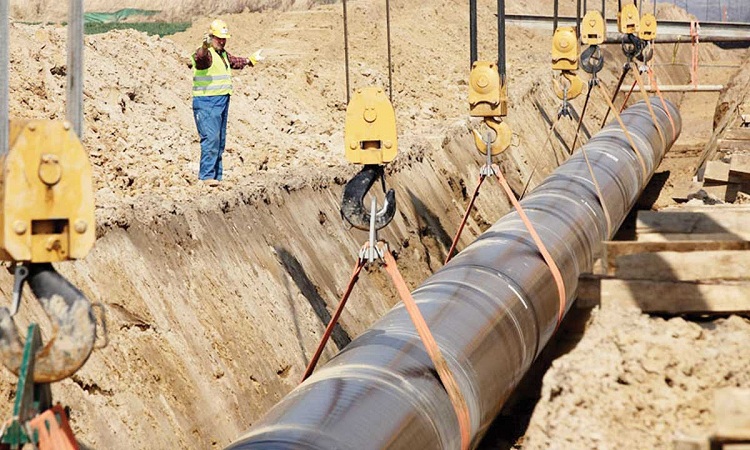
The choice of pipe laying method is influenced by many factors, the soil structure is of great importance
The sequence of operations when laying large diameter pipes in a trench
Products intended for piping are checked twice:
- Manufacturing plant.
- Before trenching.
Important! During the inspection, all pipes that have cracks, bubbles, spalls, foreign inclusions and other defects that jeopardize the trouble-free operation of the system are rejected.
Manually, with the help of simple devices, or with the use of small-scale mechanization, only pipes of small diameter are laid, in other cases, the use of cranes is required. To lower the pipe or section into the pit is a laborious and slow process, which affects the timing and cost of the work performed. The use of large-sized fasteners containing:
- vertical shields;
- horizontal runs
- spacer frames arranged 3-3.5 m from one another.
When using large mounts, one of two laying schemes is used:
- In two streams. First, the pipe is laid by the installers with a crane to the bottom, its position is finally verified and temporary fixation is made. Then another group of installers chokes joints using a compressor and pneumatic hammers.
- In three streams. Laying, welding, alignment and temporary fastening of two pipes at once separately are carried out using two cranes. The third thread performs chasing joints.
Fastening is carried out by powdering the soil or using wedges.Joints of pressureless pipes are sealed with tarred tow or asbestos-cement mixtures, pressure pipes - with rubber rings or cuffs. Compounds of steel products are welded, polymer - glued and welded.
Laying concrete, reinforced concrete and ceramic pipes in a trench
For laying concrete and reinforced concrete pipes with a diameter of more than 250 mm, mounting self-propelled cranes and pipe layers are used. To speed up the process, products are pre-connected in sections (links) of 2-5 pieces. Fixing the horizontal position of the sections during lowering is achieved using the yoke.
With the intended connection, a concrete stop is pre-installed in the socket, onto which the first link is lowered. Pipes are fed by a crane with a bell forward as the installation progresses, and against the flow of the working medium.
Note! Docking is performed using sleeve and socket joints using rubber ring seals, tarred hemp and asbestos cement mortar.
When folded joints of products with a diameter of 400-800 mm, cement mortar applied to the folds is used. With diameter values exceeding 1000 mm, the entire perimeter of the joint is sealed with hemp strands and rubbed with cement mortar. On the outside of the joint, formwork is installed, the reinforcing mesh is laid and cement mortar is applied.
When closing joints of ceramic pipes, sometimes resorting to the preliminary installation of rings of bitumen mastic on the inner surface of the socket and the outer surface of the smooth end. The surface of the conical rings is softened by applying a solvent or molten hot bitumen. Thus, a durable and tight connection is made in a cold way.
The choice of polymer pipes for home piping
The functional purpose of the pipeline dictates the conditions when choosing the type of pipe, diameter and material used in the manufacture. The materials traditionally used for laying pipelines give way to polymers that are not inferior in strength and tightness, but much lighter, having a relatively low cost. A pipeline of polymer structures will have a higher throughput, and the selection of components and fittings will not be difficult and will not require significant costs.
Polyethylene pipes are recommended for laying an underground pipeline, since the source material is resistant to temperature extremes and soil pressure. For domestic water supply systems, it is advisable to purchase a PN10 model of low-pressure polyethylene pipes that can withstand a constant pressure of up to ten atmospheres. Not recommended for underground pipelines with low density PN6 grade. Installation of a polyethylene pipeline can be carried out without special tools.
Given the relatively high thermal expansion of polyethylene, the pipeline design provides for bends of a G- or U-shape.
Polypropylene pipes are harder and stronger than polyethylene pipes. They are also easy to install, the lack of flexibility is compensated by the installation of adapters and corners. Also. They are easy to connect with elements made of other materials.
For a home water supply system with a length of up to 15 m, pipes with a diameter of 20 mm are selected, with a length of up to 30 m - 25 mm, with a greater length - 32 mm. (The calculation is given taking into account the average value of the water velocity in the system, not exceeding 2 m / s). To supply hot water, polypropylene pipes with a reinforcing layer of aluminum foil or fiberglass (PN20 or PN25) will be required. When laying a pipeline of polymeric materials, it is advisable to select all of its elements from one manufacturer. They should not have irregularities and roughnesses.
The advantages of using polyethylene pipes
Polyethylene piping is the most economical and practical for installation in the household. Laying a system of low-pressure polyethylene promises:
- no corrosion problem;
- ease of cutting and stacking of individual links;
- increased throughput;
- the absence of scale and clogging with suspensions contained in the working fluid, which do not stick to the elastic inner walls;
- lack of need for additional protection of chemically inert material from the influence of aggressive environments and stray electric currents;
- saving on connecting parts, designing and laying due to the incredible flexibility of the material, which allows to achieve a minimum bending radius of 25 pipe diameters;
- lightness, simplifying transportation, installation and laying;
- resistance to temperature changes;
- sanitary and hygienic safety.
Note! Laying a polyethylene pipeline in freezing soil requires special calculations of the bending radius at lower temperatures. This is due to the uneven movement of the polyethylene structure in the vertical plane when the soil freezes, causing deformation.
Installation of engineering networks with HDPE pipes
Trench laying of engineering networks using HDPE requires consideration of the following circumstances:
- area of the territory where the work will be carried out;
- soil characteristics, the presence of hard rocks in it. Loose soil strengthen. When laying in dense and solid soil, it is customary to lay a compacted sand cushion at least 10 cm thick on the cleared bottom of the trench. Gravel of small fractions can be added to it;
- destination of the object;
- depths of freezing soil. This is a very important circumstance, since the HDPE pipeline is supposed to be laid at least 20 cm below the level of maximum freezing of the soil in order to avoid damage to the system. If the required deepening is not possible, pipes must be insulated. HDPE sewer system is not recommended to be deepened below the 2.5-3 m mark.
Installation is made:
- butt welding. Used to dock large diameter pipes;
- electrofusion welding. It is recognized as indispensable when laying is carried out in cramped conditions;
- bell method. Use, laying an external pressureless sewer, the tightness of which is increased by the use of rubber sealing rings and sealant treatment;
- using compression fittings. Usually they resort to it, laying internal communications. The diameter of pipes with detachable joints, according to the rules, does not exceed 63 mm.
Laying pipelines using HDPE reduces operating costs and ensures long-term effective operation of the system.
The use of welding during the installation of polypropylene pipes
Welding acts as the main means of connecting the elements when laying the pipeline. Obtaining one-piece joints, excluding changes in the design, is extremely convenient for trenching. The polypropylene pipeline can be laid by the route method, involving the preliminary welding of sections to a size that can be transported. The final connection is already in place.
Pipes with a diameter of 25 mm are welded for nine to ten seconds, 32 mm - for two to three seconds longer. The soldering iron heats up to 260-270º С. It is required to carefully monitor both the heating temperature and time. With insufficient heating, it will not be possible to achieve the desired bond strength. Overheating is manifested in the blackening of the plastic, which means that the area is damaged and should be removed.
When connecting the polypropylene elements by welding, they are pre-cleaned. In order to avoid gaps at the junction, the depth of the fitting is previously marked at the end of the pipe. Upon completion of welding, the swarms that appear appear to be allowed to cool, since hasty removal deforms the pipe.
Possible problems when laying polymer pipes
The laying of polymer pipes with the trench method seems to be the best choice when installing the pipeline. If it is necessary to carry out work on a site where the soil is too hard and trenching is difficult, it is worthwhile, if possible, to wait for weather conditions with high humidity. A similar effect can be achieved by moistening the soil at the site of the laying.
Laying the pipeline in loose soil is accompanied by constant shedding of soil. This can lead to deformations in the system and its decommissioning. Therefore, loose soils are usually strengthened using, among other things, special geotextiles. Another way out of this situation is to use the puncture method. Then a pipe made of polymeric materials will be placed inside a steel pipe previously laid as a protective casing.
Good to know! It is necessary to resort to the trenchless laying method when some large object appears on the pipeline path. In this case, polymer structures can be additionally insulated with a steel casing.
Pipeline insulation
Most outdoor piping requires additional protection against low temperatures. When trenching, in order to avoid the consequences of defrosting the system, warming is carried out previously using known methods:
- laying in a case, i.e., a pipe of a larger diameter;
- pouring with a monolithic layer of foam concrete;
- wrapping with a heater, for example, polystyrene foam or polyurethane foam, which will not be damaged by humidity and small rodents;
- wrapping with a heating cable, which is helically laid outside or inside the pipe in one or two parallel lines;
- increasing pressure in the system when it is impossible to conduct physical insulation.
It is not customary to insulate irrigation systems, because they are used only in the warm season. But it is worth considering the frost resistance of the system when laying, since the structure of the materials of construction can be damaged.
Compliance with technological standards when laying a pipeline in a trench will avoid problems with its maintenance and operation for decades, especially if modern polymer materials are used.