Polyethylene pipes are found in many highways for various purposes. Modern production of products is not complicated and offers pressure head, non-pressure types of various sections, shaped elements, shells. Due to its properties and characteristics, which are reflected in state standard specifications, the certificate for polyethylene pipes and other regulatory documents, the demand for such communications is increasing annually.
Content
Certification of polyethylene products
Certification refers to the procedure for checking products for compliance with state regulations. Based on the results of examinations, a certificate is issued. The receipt of this document may be mandatory or voluntary. There are lists of products for which a declaration or certificate must be issued.
Note! From the whole variety of pipe products, confirmation of compliance with the standards is necessary for pressure-type polyethylene pipes and for gas pipeline systems.
Other species HDPE pipes may not have such documents. A voluntary certificate is issued at the initiative of the applicants. It is a confirmation of the quality of products and can increase the competitiveness of the enterprise.
Voluntary certification does not exempt from the need for other permits. For example, a document (certificate, certificate) of the sanitary-epidemiological service should be issued for polyethylene pipes for drinking purposes. Other types of IPA communications (for a swimming pool or for supplying drinking water) require an expert opinion. In some cases, you may need a fire safety certificate or a hygiene certificate.
Certificate of Conformity
Polyethylene pipes can be certified in various systems. The selected scheme according to the commodity nomenclature code and the purpose of the product determine which permit document should be obtained. Both a voluntary and mandatory certificate for certain polyethylene pipes confirms their quality, compliance with the provisions of the standards and safety.
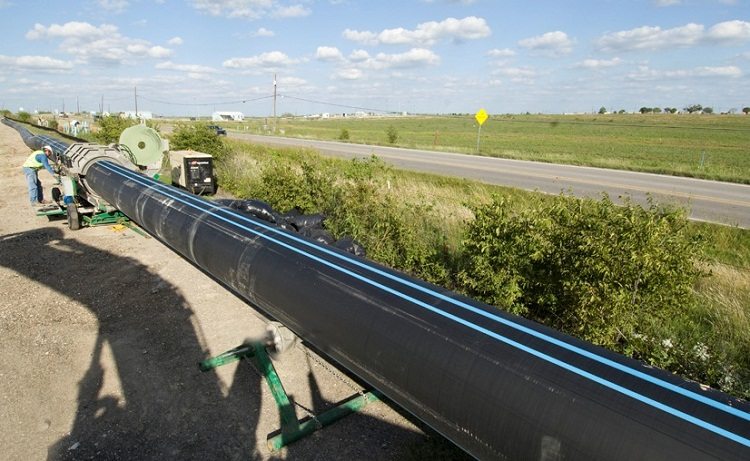
For the installation of pipelines with drinking water use only pipes that have a quality certificate
Paperwork is carried out by accredited bodies. If necessary, they can issue a letter of refusal, which indicates that the particular product taken does not require mandatory confirmation of quality. To obtain a certificate for polyethylene pipes, the applicant must apply to the certification body with an application and all the necessary technical documentation for them. The applicant may be both the manufacturer and the distributor of PND products.
After reviewing the application and making the appropriate decision, the selection of the necessary samples and certification tests are carried out. Polyethylene pipes are checked for compliance with physical characteristics, strength, resistance to deformation and many other parameters. Methods of certification tests are regulated by GOSTs.The results are entered into the protocol and studied by specialists. If PND products meet all the requirements and standards, then a certificate is issued.
Extruders for the production of HDPE pipes
For the production of polyethylene pipes, extruders are used, which according to the principle of work are:
- auger;
- combined;
- disk.
Most often, the first type of mechanisms is used to manufacture PND products. The main element is the Archimedes screw (or auger). Such extruders may have one or more co-directional or counter-directional screws.
Disk (single or multi-disk) mechanisms are relatively rare. They are distinguished by a higher price and structural complexity. The principle of operation of an extruder of this type is based on the movement of raw materials using special disks by adhesion. At the same time, granular polyethylene mixes well.
Note! The disadvantage of a disk extruder is the inability to manufacture polyethylene tubes with high strength parameters and an exact predetermined geometric shape due to the low pressure in the area of the working head.
If the mechanism uses both the disk and the screw part, then it is called combined. Using such extruders, the production of polymers with low elasticity and viscosity has been organized. Also, mechanisms can be universal and specialized, one- or two-stage, without a degassing zone or with it. Technology is improved annually, so the variety of models is constantly growing.
Equipment on the production line
A standard polyethylene pipe production line usually includes the following equipment:
- granular polyethylene feed system;
- extruder
- removable dies (working heads);
- vacuum moulder, calibration bath, pulling device;
- cooling system;
- conveyor belt;
- cutters and cutting device;
- HDPE pipe laying system.
Product manufacturing is fully automated. All technical processes during manufacture are checked by a control system. It is important that one company act as a supplier of HDPE, since a change in raw materials will require the installation of other suitable equipment for the manufacture of communications.
Used polyethylene for pipes may have a certificate confirming its quality and compliance with the requirements of documents.
Process steps
The technological basis for the production of HDPE communications is extrusion - forcing material in a molten state through a forming hole (die). At the initial stage, the granular feed is loaded into the hopper of the extruder. Then it enters the working cylinder equipped with heating elements.
Moving, the feed passes to sections of the cylinder that are hotter. Accordingly, 3 of its working areas are distinguished:
- filing;
- plasticization of polyethylene;
- pushing out.
In the plasticization zone, compression, homogenization, and also the melting of polyethylene granules occur. The shape of the finished product and its quality are determined by the die.
Note! The production of pipes from polymers requires that the molding head have a certain fixed temperature during the passage of the melt.
In the designs of the dies there are cartridge or flat heating elements. Passing the external matrix and the forming mandrel, the workpiece is already acquiring a cylindrical shape. The calibration process follows - the polyethylene pipe enters the area of the vacuum bath, where it is finally molded by pressing it to the calibration form.
Then the product goes through the cooling stage and enters the caterpillar or belt type conveyor.At the final stage, polyethylene pipes are cut with cutters or circular saws and stacked in bays. They are marked.
Product quality control
A typical production line allows the production of pipes and fittings from polyethylene of the following sizes:
- pressure pipe for water lines with a diameter of 12.5-120.0 cm;
- pressure head gas pipe section 12.5-31.5 cm;
- sheath pipe with a diameter of 12.5-120.0 cm.
In the workshop where pipe products are received, quality control must also be ensured. At the entrance, monitoring of consumables is carried out on the basis of accompanying documents to them (for example, passports, certificates).
During manufacture, the quality of the pipe is controlled by the operator based on information from measuring equipment and devices. In addition, it is important to conduct visual inspection of the communication surfaces for the presence of shells, scratches or sagging.
Also, each batch of polyethylene pipes is checked for compliance with the provisions of the standards. It is conducted by the technical control service. When storing and transporting products, it is necessary to adhere to the rules: lay pipes on flat surfaces, take a stack height of no more than 2 meters when stored for more than two months, no more than 3 m - up to 2 months.
Pipe specifications
Polyethylene as a material has many advantages. Its developers point to a huge operational life of up to 300 years, but pipe manufacturers guarantee significantly lower values.
note! Polyethylene products are very reliable. This is due to the properties of the material itself and the technology of their manufacture, in which the polymer is structured.
Pipes are not susceptible to corrosion, various influences of chemical environments, which allows them to be installed underground, have a high resistance to water hammer. The latter property is due to the plasticity of polyethylene, which under high loads can stretch a little.
Also, communications do not require special maintenance and protection. They are characterized by high thermal insulation parameters, therefore, when laying underground, additional insulation is not required. Additional properties include light weight (this greatly simplifies installation work), simple assembly technology, and a large length, which reduces the number of connections.
The disadvantage of polyethylene pipes is one - poor resistance to ultraviolet radiation. Therefore, the main area of use of such products is underground utilities.
Polyethylene pipes are a modern and competitive product, the production of which does not require large financial and labor costs. Water pipes with their use have a long service life.