The seamless pipe is one of the most expensive types of metal. This is due to the complexity of its production. The product is highly reliable and is manufactured in full accordance with standards. Seamless seamless pipes are widely used in oil refining, chemical industry, aircraft and machine building, as well as in public utilities.
Content
- 1 Cons and pros of seamless steel pipes
- 2 Seamless design: main types
- 3 Scopes of use of seamless products
- 4 Standardized product size requirements
- 5 Seamless products for special purposes
- 6 Standards for hot-deformed pipes
- 7 Product Quality Check
- 8 The secrets of pipe production
- 9 Correction of product parameters during manufacturing
Cons and pros of seamless steel pipes
The scope of steel pipes is very extensive, since the absence of seams affects the strength characteristics of products - they become almost invulnerable. The seamless design is characterized by low linear expansion, which is caused by the influence of high temperatures, corrosion resistance and is not afraid of high pressures.
The degree of thermal conductivity depends on the material of manufacture and, as a rule, is at a good level. The seamless steel pipe has a perfectly smooth surface inside, which improves throughput. Compared to a welded product, the seamless design is much better in terms of strength and resistance to external influences.
Among the shortcomings of this type of metal rolling, the lack of flexibility of thick-walled products can be noted, which can lead to certain difficulties when performing repair and construction works. In addition, the production of pipes requires expensive equipment, and the technology itself is very complex. In combination with the high cost of materials, this leads to an increase in the cost of production, so in some cases it is impractical to use such products.
Seamless design: main types
Seamless steel pipe is classified according to wall thickness. In the case where the wall is larger than the diameter, the seamless structure is called especially thick-walled. In addition, especially thin-walled, thin-walled and simply thick-walled elements are distinguished.
Note! The first type is characterized by a wall thickness of no more than 2.5% of the diameter, for the second from 2.5 to five percent, for the third from 5 to 10%.
Light, reinforced and ordinary structures are also distinguished. Reinforced pipe options are characterized by increased corrosion resistance, and the lungs lend themselves well to bending. The most common is a seamless steel structure, but it is possible to produce products from various alloys and non-ferrous metals. Pipes vary in manufacturing techniques. On this basis, cold and hot rolled products are distinguished.
Scopes of use of seamless products
Due to the excellent strength characteristics, seamless pipe has found its application in a large number of sectors of human life, but the main one is the installation of highways for various purposes.In the gas and oil industries, such products are used to transport fuel.
The absence of a weld and an absolutely smooth surface inside allows the use of such elements in pipelines for drinking water supply. Seamless design allows arranging highways transporting aggressive substances and being under high pressures and elevated temperatures.
The nuclear industry is not complete without such pipes. They are used in ship, car, aircraft, tractor and machine building, for example, to solve the problem of transmitting shaft rotation. A seamless hollow, seamless structure is needed in the construction of coal mines and oil rigs.
It is advisable to use it under particularly difficult operating conditions, when ordinary metal and the weld may not withstand. Monolithic products also found themselves in the defense industry.
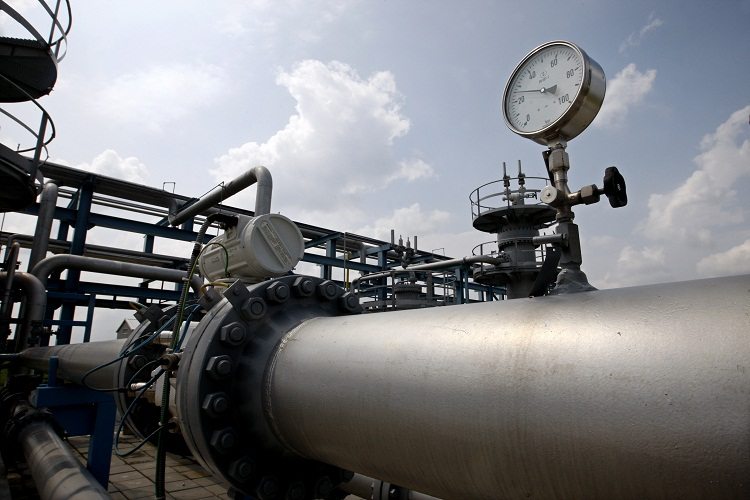
Seamless pipes are indispensable for highways operating in difficult conditions, under high pressure or temperature.
Standardized product size requirements
The requirements for cold-deformed products are set out in standard 8734 of 1975. According to this document, a seamless pipe can be produced in unmeasured or measured lengths. In the first variant, this characteristic is within the limits of 4.5–9 meters, in the second - from one and a half to 11.5 m. The maximum deviations are not more than 1 cm.
By agreement with the customer, pipes of measured length can be produced from 4 to nine meters with a constant value of limit deviations. Products of multiple measured lengths are produced in sizes from one and a half to 9 m.
Note! Typically, products are made in accordance with the wall thickness and outer diameter, however, according to customer requirements, you can focus on other characteristics, for example, difference and both diameters or wall and inner diameter.
At the request of the customer limit deviations can also be combined. For example, the diameter of the product is made by ordinary accuracy, and the wall thickness is increased.
Manufacturers are required to ensure that neither the difference in size nor the ovality of the pipes go beyond the limits of permissible deviations. The standard also gives curvature values. For products with a cross section of up to 8 millimeters, it should not be more than 3 mm, within 8-10 mm - more than 2 mm per 1 m of length, more than 10 mm - more than one and a half millimeters.
Seamless products for special purposes
There are seamless pipes for special purposes, which are produced in accordance with the standard 9941 of 1981. This type of metal rolling is also characterized by measured, multiple and unmeasured length. Wall thickness varies from 0.3 to 24 mm, diameter - from 5 to 250 mm.
Possible curvature of the structure is determined depending on the parameters. For example, for products with a cross section higher than 5 mm and a wall from half a millimeter, this figure can be no more than 1 millimeter per meter, and for a diameter of more than 15 mm and a metal thickness of less than 0.5 mm, up to 2 mm.
The edges of the metal should be free of defects and trimmed to 90 degrees. At the request of the consumer at the ends can be applied chamfers for welding. This is permissible when the thickness of the metal is more than 5 mm. In this case, the material of manufacture must meet special requirements. For example, the chemical composition of steel is regulated by state standard 5632, and some of the harmful impurities (sulfur) cannot exceed 0.02%.
The surface of the pipes should be characterized by the absence of sunsets, shells and cracks. The exception is products that have not been cleaned. At the same time, single captures, small dents or risks are allowed on them, but the influence of these defects on the diameter and wall of the element is excluded.
Standards for hot-deformed pipes
Hot-deformed seamless products must fully comply with the standards that are stipulated in state standard 8732 of 1978. This document contains tables with possible product sizes. Hot-deformed products of measured / unmeasured length are made from 4 to 12.5 meters. In the case of multiple lengths, an allowance is possible that does not exceed 5 millimeters per cut.
Note! The maximum permissible deviation is +15 mm if the product is more than 6 m, +10 mm if the pipe is shorter than this length.
As for cold-deformed elements, the difference and ovality should not lead the wall and diameter beyond the specified boundaries. The curvature of the pipes depends on the thickness of the metal (all values correspond to one meter of the product). If it is less than 20 mm, then the parameter cannot be higher than 1.5 mm; if 20-30 mm - up to 2 mm. For pipes with a larger wall thickness, a curvature of up to 4 mm is permissible.
Product Quality Check
Seamless seamless pipes of high quality without fail undergo a series of tests. After checking the products for the absence of surface defects with the help of special instruments, the diameter, ovality, length and curvature are measured.
A tensile test is conducted according to document 10006-80. In this case, the relative narrowing and elongation of the pipe after rupture, the temporary resistance of the material and its yield strength are determined. According to the requirements of standard 19040-81, seamless structures are tensile tested at elevated temperatures. In this case, the material characteristics are set at temperatures from 35 to 1200 degrees.
Also, all elements are tested by hydraulic pressure. Regulatory document 17410 stipulates the conditions for ultrasonic testing. If at least one indicator does not meet the standards, it is necessary to conduct repeated tests on twice the number of samples.
The secrets of pipe production
Consider the process of manufacturing hot rolled pipes. It consists of several technological steps. Raw materials are billets, which can be continuously cast, forged, rolled or even ingots.
Note! The selected type of element affects the strength class and the class of finished products.
At the initial stage, the blanks go to presses or mills, where the formation of the sleeve occurs. Further, its diameter increases to the required size. At the same stage, the surface leveling of the future product takes place. Then the pipe enters the hot rolling mill. The final step is a cold calibration process. If necessary, a thread is applied to the pipe.
The formation of the sleeve is carried out on machines that consist of cone or mushroom-shaped rolls with one-sided rotation. They are located in a vertical plane and are characterized by a slope of several degrees. Due to the rotational-translational motion, the cross section of the workpiece located between the axes is reduced, and a small hole appears in the axial part. To increase the diameter, a special mandrel is required.
Correction of product parameters during manufacturing
The mandrel is installed between the shafts, and a metal sleeve is mounted on it during the next passes. Structural displacement can be avoided with fixed rollers and ruler guides. To adjust the diameter of the pipe, there are various automatic installations. Their work is carried out according to this principle: the mandrel is inserted into the caliber so that there remains a gap equal to the wall thickness of the future product. Further, the seamless structure is rolled, and the mandrel is deployed at a right angle each time. In order for the pipe to enter the mandrel, it is necessary to lower the lower roller of the installation.After occupying the desired place with the blank, the roller is placed in its original position.
A cold-deformed pipe is made on the basis of a hot-rolled billet, the heating of which is carried out to low temperatures. The future pipe undergoes a drawing process, during which it is drawn, the diameter is regulated and the wall thickness decreases. Such elements are distinguished by high surface quality. The pipe acquires anticorrosive properties by galvanizing. A thin layer of zinc promotes the appearance of a protective film on the surface of the metal, which prevents its contact with O2 (oxygen) and its penetration deep into. Products processed in this way do not need a primer or paint.
Seamless pipes are indispensable structural elements operated in difficult and aggressive conditions. Their parameters are much superior to the strength characteristics of products with a seam.