Most often, galvanized pipes are used in the construction of pipelines transporting gas or water. The cost of processing products with zinc is slightly less than other corrosion protection methods, so such steel pipes are available. There is no separate standard for galvanized products. Steel pipes of this type are manufactured according to regulatory documents for electric-welded straight-seam (GOST 10704) and gas pipeline (GOST 3262-75) products.
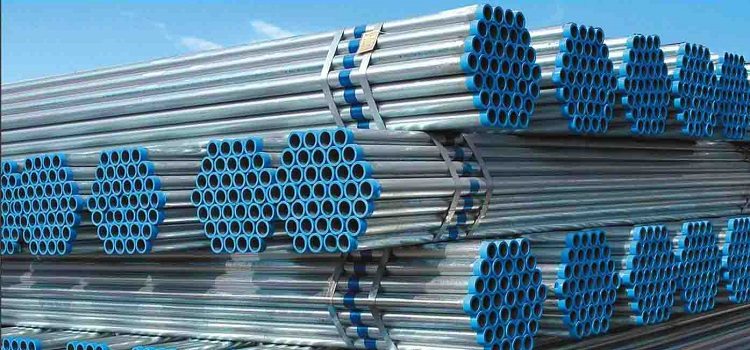
Galvanized pipes have a layer of protective coating, which significantly increases their service life.
Content
Galvanized Pipe: Technical Parameters
Galvanized pipe is characterized by good mechanical strength and resistance to high temperatures. Technical parameters of the products allow their use for the construction of heat-conducting networks with liquid temperatures up to + 130-140 ° С. No other pipes made of other materials give a guarantee of trouble-free operation under such conditions.
The main technical characteristics of galvanized steel pipes are:
- outer section from 10.2 to 165 mm;
- the weight of one meter of the product is from 0.4 to 22 kg;
- nominal pass from 6 to 150 mm;
- wall thickness from 1.8 to 5.5 m;
- length from 4 to 12 m.
As well as ordinary, galvanized pipes are available with lightweight, reinforced and standard walls. Distinguish ordinary and increased accuracy. For the manufacture of tubular products, steel is used that complies with the points of standard 1050.
Galvanized products must have a protective coating located on their entire surface with a thickness of not less than 30 microns. Peeling of the zinc layer from the base material, external impurities, bubbling is not allowed. Pipes may have small flux spots and local influxes. The thickness of the protective layer is determined in accordance with 9.301; 9.302.
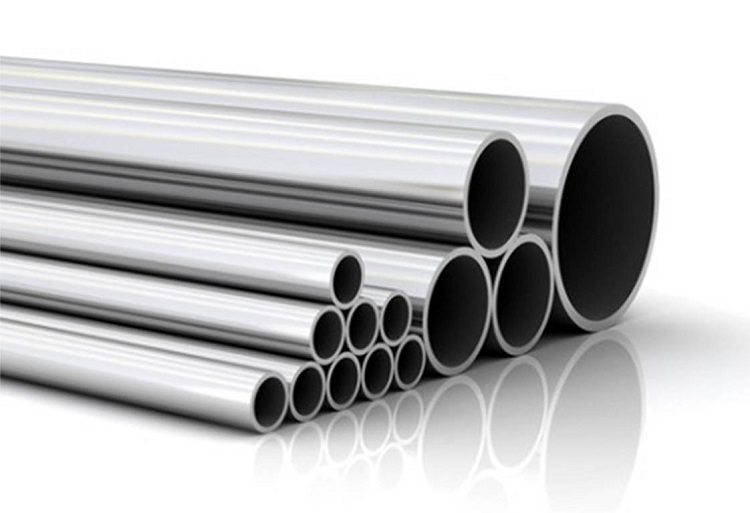
A variety of diameters of galvanized pipes allows you to choose a product for domestic and industrial purposes
Pipe Galvanization Technology
The terms of use of the products determine the requirements for their characteristics. Galvanization of a steel pipe can be carried out on its external or internal surface. Various technologies are used for coating. Their choice largely depends on the required strength and quality of the zinc layer, as well as on the size of the pipe.
There are such types of galvanizing:
- electro galvanic;
- hotter;
- thermal diffusion.
In addition, there are ways that protect already mounted steel communications. Such methods include, for example, cold galvanizing - painting the pipe with a zinc-containing composition. Such a coating will last at least 5 years, however, it is sensitive to mechanical damage.
The method of galvanizing by the thermal method involves obtaining a coating on the surface of the product by flame spraying of zinc powder. A distinctive feature of this coating is porosity.
Note! Such protection will last about 7-8 years.
Features of galvanizing
Electro galvanizing of a steel pipe is one of the most used coating methods. It is based on the dissolution of zinc electrodes in an electrolyte under the influence of current. During electrolysis, zinc is deposited on the surface of the product.
For this method, various electrolytes are used - cyanide, non-cyanide, acid. One of the most common in the industry is alkaline galvanizing. The thickness of the coating and its characteristics depend on the temperature regime, the strength of the electric current between the anode and cathode. The resulting layer should be continuous and uniform.
The advantages of this technology include evenness of the coating, good appearance, low cost, high speed and a layer thickness of 30 microns, the disadvantages are poor adhesion, low operational life (up to 5 years) due to porosity. In addition, the disposal of the electrolyte used to obtain galvanized steel pipes is quite dangerous from an environmental point of view and an expensive process.
The essence of hot dip galvanizing
The method of hot galvanizing allows you to get the most reliable coating and is made in accordance with GOST 9.307-89. Its disadvantage is the high cost and the possibility of sagging on the surface of the pipe.
Note! The hot dip galvanizing method is applicable for steel grades with a carbon content of not more than 0.24%.
Hot technology involves immersing a steel pipe in a zinc alloy at a temperature of approximately 450 ° C. The technological cycle includes the following stages: hanging of the product; degreasing; etching; flushing; drying; preheating; direct galvanizing; cooling.
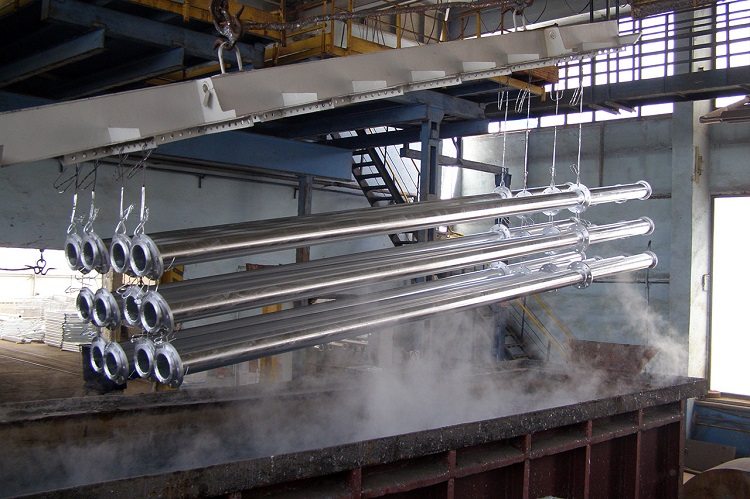
For hot-dip galvanizing, pipes are immersed in a zinc solution heated to a temperature of 450 degrees
For good adhesion, the steel pipe must be cleaned of oils and oxide layer. To do this, it is degreased and etched in a solution of hydrogen chloride (Hcl). The edges of the product with a radius of at least 3 mm are also pre-rounded. In the zinc bath, the pipe is no more than 10 minutes. The minimum value for the duration of the procedure is 3-4 minutes.
The advantages of the technology are:
- high productivity of the process;
- resistance of treated pipes to rust;
- good thermal conductivity and electrical conductivity of the zinc layer;
- simplicity of equipment and simple implementation of the process.
In this way, a protective zinc coating with a thickness of 40-200 microns can be obtained.
The process of thermal diffusion galvanizing
With high demands on the quality of the coating, thermal diffusion technology is used. A galvanized steel pipe is obtained by applying zinc vapor to the surface of the product. The process takes place in sealed containers, ensuring its environmental safety, and meets the requirements of GOST R 9.316.
The advantages of the method are:
- high hardness of the coating;
- lack of influx;
- the possibility of applying a protective layer only on the desired surface;
- operational term is more than 15 years;
- minimal layer disturbance when welding galvanized pipes.
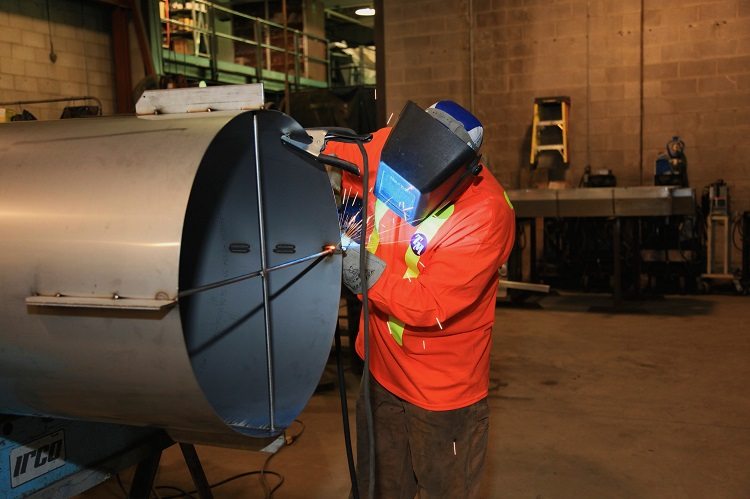
The zinc layer deposited by the thermal diffusion method will receive minimal damage when welding pipes
Thermal diffusion technology ensures maximum adhesion of zinc and metal. The thickness of the coating can be any and depends on the time that the steel pipe spends in the tank. Due to the lack of need for preliminary acid etching, the products do not lose their mechanical characteristics. The temperature of the process is 400-470 ° C.
Pipe Connection Rules
Connect steel products It is possible with the help of thread and welding. Threaded docking is an expensive process, so it is rarely used.A specific feature of galvanized metal welding is the transition of zinc into a gaseous state under the influence of a significant arc temperature.
Note! Since zinc fumes are harmful, the current standards require the equipment of the welder's workplace with local high-performance ventilation.
When welding, the heat-affected zone must be cleaned of the zinc layer. Otherwise, the connection will be very fragile and brittle, since after solidification of the metal intercrystallization cracks occur, and zinc concentration occurs along the grain boundaries of the metal. Places that connect must be degreased.
If it is technologically not possible to remove the zinc layer, then welding is carried out by electrodes with a special flux coating. The amount of flux should be 2 times greater than with normal soldering. During work, it is necessary to prevent overheating of zinc. This condition is important to ensure good corrosion protection.
With a wall thickness of less than 3 mm, materials do not require special edge preparation. The gas flame of the burner is set so that a slight excess of oxygen remains. After completion of welding, the flux is removed.
Galvanized pipes are an excellent structural material. Characteristics and appearance of products determine their popularity.