Bends are a type of connecting fittings that are used in various pipeline structures to change the direction of the pipe. They can be made from various materials (metal and polymer) and have a variety of dimensions. In the manufacture of such important elements of pipelines as bends, it is necessary to comply with quality standards and process technology.
Content
Varieties of bends
From a structural point of view, the branch is a pipe segment, which is made at a certain angle. The selection of these products is carried out depending on operational tasks. They are classified according to several criteria:
- material of manufacture;
- mode of production;
- the size;
- bending angle.
All bends can be made of both metal and plastic. Consider the basic materials from which these products are made:
- steel (stainless, alloy and carbon);
- low pressure polyethylene (HDPE);
- polyvinyl chloride (PVC).
Note! Each branch, without exception, has its own brand, which is assigned to it in accordance with state standards (GOST). The brand of the device allows you to learn all the necessary information about it if you wish.
If the indicator of the communication cross-section is less than 50 mm, then steel fittings are used to organize the branches. All steel bends are divided into two groups:
- welded;
- seamless.
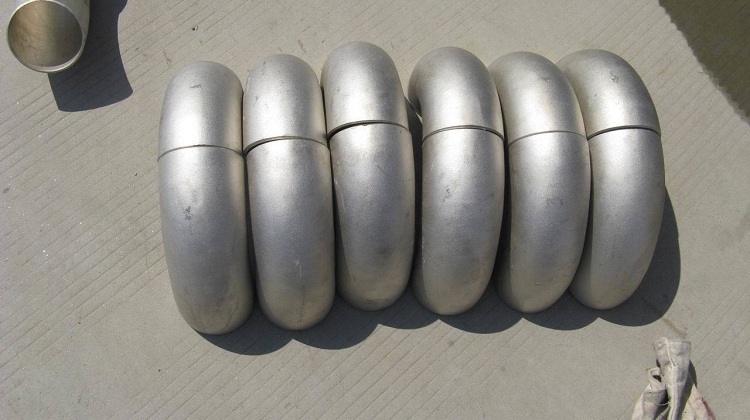
For the production of bends, metals and alloys are used - steel (including stainless), cast iron, copper and others
The presence of a seam in steel models is determined by the production option. Steel fittings are manufactured using special pipe bending equipment, and plastic fittings are usually made using the extrusion method.
Branch operation area
Today, industry does not stand still. The methods for obtaining various components for pipes are improving every day, but the fundamentals of the technological process remain unchanged. As mentioned above, steel and plastic materials are used for the production of bends. Outlets are made of plastic, which are mainly used during the laying of plastic sewer lines.
Steel products, in turn, are used in more severe operating conditions. Pipelines with high pressure, as well as communications transporting aggressive media, require durable and corrosion-resistant components. Stainless steel fittings are suitable for use in virtually any climate.
The operational area of these elements of pipeline communications is quite extensive. They are used in economic, industrial spheres of human activity. Let us consider in more detail the systems in which these products are used:
- water supply communications;
- gas pipelines;
- oil pipelines;
- heating network.
Steel products are popular for laying trunk lines related to the oil and gas industry.In such communications, the working medium moves through the pipes under high pressure, so the steel connecting elements are suitable for them as well as possible. In turn, water pipes laid for economic purposes are laid using thin-walled connecting bends.
Modern industry allows to obtain products that are resistant to fairly high pressure (up to 100 MPa). The operating temperature for modern bends ranges from −70 to +450 ° C.
Methods for the production of various steel bends
All steel bends are divided into several main varieties:
- steeply curved;
- stamp welded;
- welded sectional;
- bent.
Consider the main ways to perform the above varieties:
Steeply curved. Products of this type are regulated by state standards 17235–2001 and 17235–83, as well as technical documentation (TU). Such parts are produced by pulling a pipe segment through the mold. Thanks to this method, products with high quality characteristics are carried out. The material for such models is carbon steel and stainless steel. The bending angle obtained by drawing through the mold ranges from 30 to 90 °. The minimum cross-sectional index for such models is 18 mm, and the maximum is 426 mm. The maximum working pressure that such a pipe bend can withstand is 16 MPa.
Bent. The manufacture of bends of this type is performed on pipe bending equipment. The billet during bending can be in two states: cold or hot. Such models have a straight section and are used in cases where for one reason or another it is not possible to use steeply curved products.
Note! The main disadvantage of bent bends is that they have a rather impressive mass, which complicates their installation on the pipeline.
Such products may have a bending radius of 2 to 90 °. These parts are regulated by GOST 24950–81 and relevant technical conditions. The minimum working temperature for such fittings is −50 ° C, and the maximum reaches +510 ° C. Bent models can be used in pipelines with very high pressure (up to 100 MPa).
Stamped. Performed through the use of welding equipment. Material for the production are special alloy steel or stainless steel sheets. Thanks to this method, products with large dimensions (up to 420 mm) are obtained. As a rule, such models are used as structural elements of gas and oil pipelines. Regulatory documentation in this case is presented by technical conditions.
Welded sectional. These products are produced by welding individual sections of pipes made of carbon or low alloy steel. From a structural point of view, such products are less reliable, since they are not an integral part, therefore they are used in communications with low pressure indicators (up to 2 MPa). The maximum operating temperature for such products does not exceed 425 ° C. Such bends have sizes from 108 to 1620 mm. The main operational area is thermal power plants.
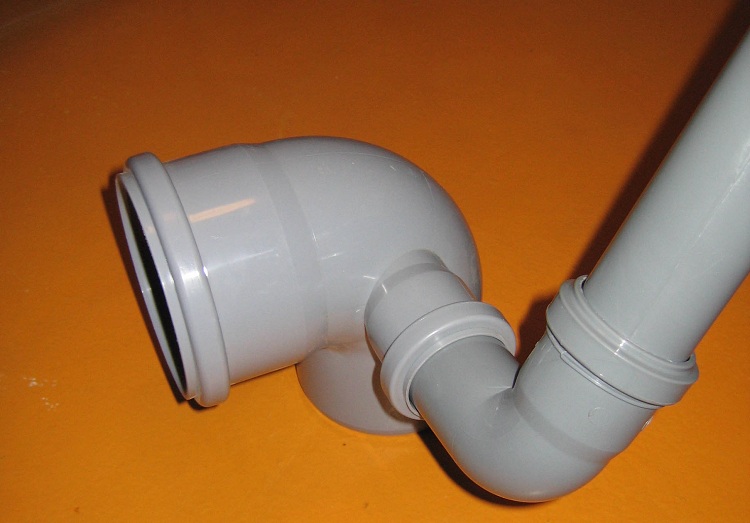
Bends from polymeric materials are used when connecting pipes from polyethylene, polypropylene, polyvinyl chloride and others
Plastic bends
Plastic fittings of this type are quite common today and have some advantages over steel counterparts. From the point of view of strength, they lose to steel models, however, the simplicity of manufacture, transportation and installation, as well as the low weight of bends made of polymeric materials allowed them to take their place in the modern market.
Consider the main polymeric materials from which pipe bends are made:
- low pressure polyethylene (HDPE);
- polyvinyl chloride (PVC).
For the manufacture of polyethylene fittings, different brands of low-pressure PE are used, which are distinguished by a high density coefficient (for example, HDPE). Low-pressure polyethylene in itself is a very durable material, therefore, products from it are able to provide stable pressure indicators in communication. Another feature of these products is elasticity, which makes it easy to install. Installation of polyethylene bends is easy, since there is no need to use welding equipment. Of the minuses of these products can be identified poor tolerance of low temperatures. Such products are used for the installation of internal sewer networks.
Models made of polyvinyl chloride are durable and are resistant to temperature extremes, active chemical compounds and ultraviolet.
Helpful information! As a rule, PVC pipes and bends are used for laying open (external) sewer communications. This is due to the fact that polyvinyl chloride parts are resistant to low temperature indicators, in contrast to PND products.
Polymer products, including PE and PVC bends, are made using the extrusion method. The phased production of polymer bends includes: extrusion, calibration, part cooling, calibration, trimming and stacking.