The connection of plastic pipes is not the most difficult, but responsible operation associated with the installation of pipelines for various purposes. The widespread use of polymer structures has led to the use of materials that differ in certain features for their manufacture. When choosing in favor of one or another type of connection of the elements of a plastic pipeline, the requirements of instructions drawn up taking into account practical experience are taken into account.
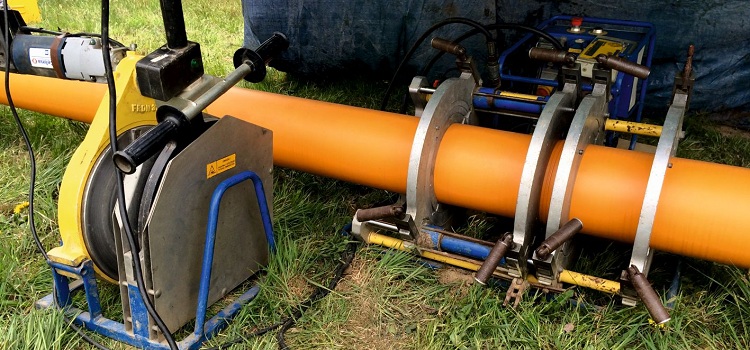
The method of joining plastic pipes depends on the type of product, their diameter and the performance of the mounted line
Content
What affects the choice of connection method
The impact of what factors have to be taken into account when determining the type (method) of docking? First of all, it is taken into account which of the types of polymer products it was necessary to combine:
- metal-plastic;
- polyvinyl chloride (PVC);
- polypropylene;
- polyethylene.
It is advisable to choose connectors for different types of plastic pipes from the same material from which the plastic elements of the pipeline construction were made. Then the reliability of the connection will be higher than when connecting different types of plastic or a combination of plastic structures with metal.
Secondly, it should take into account the particular operating conditions of the site where the docking is performed. Not all types of adhesive joints, for example, are useful when installing a heating system, since they begin to melt when the temperature rises. When installing the heating system, it is desirable to combine the sections using couplings.
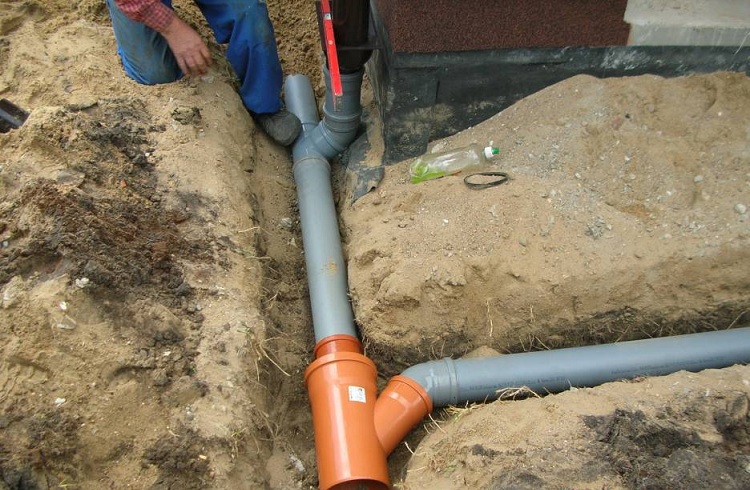
To create branches and change the direction of the pipeline, fittings are used: bends, tees, crosses and other elements
Thirdly, it is important to consider the complexity and shape of the structure. Installation of rectangular (square) sections excludes the use of adhesives for joining, since pipes cannot be glued at a strictly defined angle. In such a situation, it is wise to use fittings.
Types (methods) of compounds
Vrastrub. The simplest method used in the installation of sewers. The end of the other is placed in the bell of one product using a sealing ring. Tightness and durability of a connection are provided with a sealant.
Flange. Apply by connecting metal areas with plastic. The flange method of connection will require welding the bushings under the flanges to the ends. Steel flanges are screwed onto the bushings. The flange connection can be used during the installation of a square design, but then angular couplings will be additionally needed.
Collet connection of pipes. It is used when docking elements having a small diameter. Installation is carried out using crimp fittings. With the collet connection of plastic pipes, the presence of a rubber sealant and the insertion of the teeth of the plastic sleeve into the pipe increase the strength and tightness of the structure.
Butt welding. It is used when joining products with a diameter exceeding 50 mm.The connected elements are pre-cleaned, installed in a centralizer, checking the accuracy of joining and parallelism of the parts, connecting the heating plate. Having removed the plate, the structural elements are docked. The use of butt welding using a special welding machine is excluded during the installation of square structures. You should not resort to this type of connection if the operating conditions are associated with high pressure, differential pressure. Inevitably, deformations will occur, the joint will disperse. In this case, they decide how to connect the plastic pipes and without soldering.
Welding using an electrofusion coupling. Prepared (peeled and fat-free) elements are placed in the same plane and put on them an electric sleeve. By connecting current, the coupling and pipes are heated at the junction, after which the joint is allowed to cool. The electric coupling for plastic pipes is not recommended for use in the installation of heating systems due to the instability of the joints.
Threaded. It is used in cases where it is necessary to dock metal and polymer structures.
Glue. It also implies the use of “cold welding”, in which the joining is carried out at the molecular level when the pipe section is dissolved.
Docking of polyethylene pipes
Polyethylene structures are joined using detachable and one-piece connections. The choice in favor of one or another type is determined by the necessity or undesirability of disassembly during operation.
Plug-in connections of small diameter are carried out by a collet connection with compression fittings. With large diameters of the polyethylene elements they are connected by a flange method.
One-piece joints are created by welding:
- Butt-heated tool.
- Using an electrofusion coupling.
Butt welding of polyethylene products requires special equipment and the availability of a qualified specialist for its maintenance. But this method promises its advantages:
- no additional elements are needed;
- the whole operation will require one weld, not inferior in strength to the connected parts;
- flexibility of products remains;
- it is permissible to carry out work on the surface, and then install the entire structure in the right place.
Butt welding is used exclusively for equal wall thicknesses of polyethylene pipes. In other cases, thermistor welding is necessary, using an electric coupling.
PVC pipe joint
Joining of PVC products is usually carried out in a bell. Pieces of the required length are cut with a pipe cutter (or hacksaw). The joined end face and the inner surface of the bell are cleaned and degreased. A rubber seal is installed in the socket. The smooth end of the pipe, lubricated with a silicone compound, is inserted all the way, and then pulled back 7-10 mm, to a pre-set mark. This provides greater bond strength. The assembly itself is carried out, as a rule, manually, and for positioning they resort to using scrap as a lever (in difficult cases, they resort to a jack).
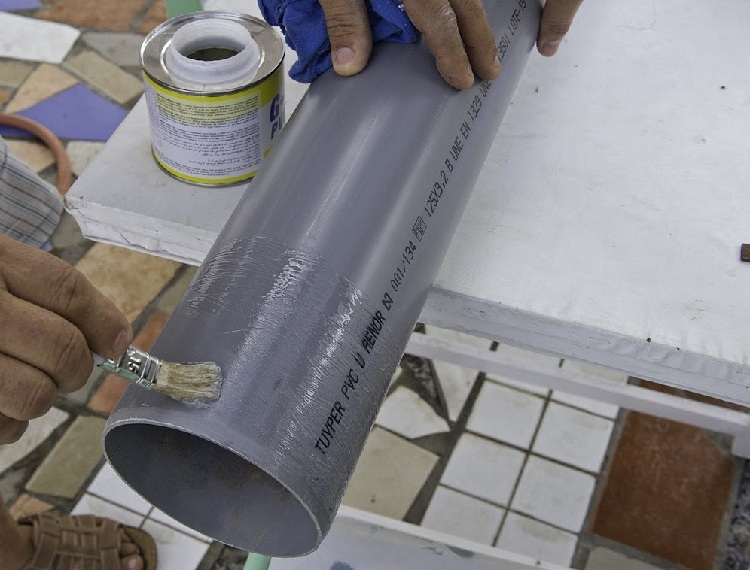
The connection of PVC pipes with glue is a fairly reliable method that ensures the tightness and durability of the system
The glued joint of PVC plastic pipes is carried out in the following order:
- After cleaning, the surfaces to be bonded are treated with a sandpaper to roughness to enhance adhesion.
- Glue in a uniform layer is quickly applied to 2/3 of the socket and the entire calibrated part of the pipe.
- Having entered the pipe all the way into the bell, they turn a quarter of a turn. All operations are carried out within three minutes.
- The connected elements are pressed tightly for about a minute, so that a thin strip of glue is squeezed out at the joint.
Cross-linked polyethylene pipe joint
Cross-linked polyethylene products are connected by fittings:
- compression;
- fitting;
- electrowelded.
The connection is carried out in the presence of an equal bore coupling, two mounting sleeves and a flaring tool. The sequence is as follows:
- A section of about five centimeters long is cut off strictly from the working pipe, the bevel is cut.
- A coupling is put on the product in the direction of the coupling to be connected using the internal fixing groove.
- The pipe is expanded. A hand or hydraulic tool is used. Its expansion nozzle is turned relative to the workpiece. After the first flaring, another turn is made, approximately 30º.
- The sleeve is inserted and held for some time (with a diameter of 11 cm - about three to four minutes). This time is enough for the product to compress the fitting tightly.
- The sleeve is pushed all the way to the coupling.
The same operations are carried out for the other end of the pipe, completing a tight and reliable joint.
Docking of polypropylene pipes
Polypropylene parts with a diameter of up to 63 mm are connected:
- With the help of compression fittings, without the use of special equipment.
- In a bell or with the use of socket welding. For larger products, butt welding is recommended.
Connecting polypropylene elements with a diameter of up to 40 mm, it is permissible to use a manual welding machine. For large diameters, you will need an aggregate with a centering device. The nozzle (heating element) consists of a sleeve and mandrel, which fuse the outer surface of the pipe and the inner side of the socket. The standard Teflon nozzle with a diameter of 16-40 mm is cleaned after each welding (it is unacceptable to clean the cold nozzle from plastic!).
For welding, the apparatus with the required nozzles, issuing a working temperature of 260º, is installed and fixed on a flat surface. Then:
- a pipe is cut perpendicularly;
- its end and fitting socket are cleaned;
- at a distance 2 mm greater than the depth of the socket, a mark is applied to the connected element;
- the pipe is inserted into the sleeve, the socket is put on the mandrel;
- by holding the required heating time, the parts are removed and docked.
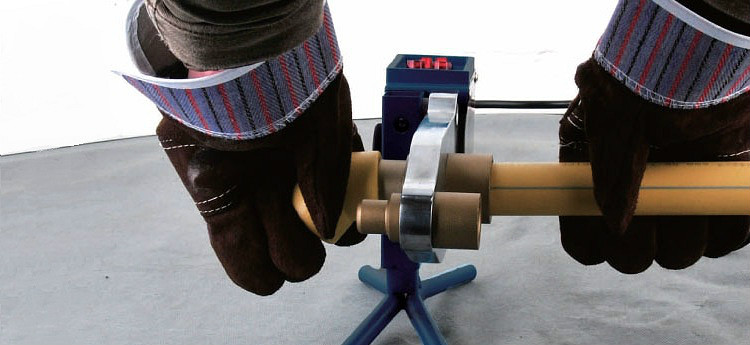
To connect pipes made of polypropylene, special equipment is used, with which the ends of the workpieces are heated to the desired temperature
Connection of plastic pipes
Due to the significant difference between the melting points of the polymer and aluminum, which are part of the metal-plastic products, they cannot be joined by welding. Self-installing metal-plastic pipeline, use fittings:
- crimp;
- press;
- self-focusing push fittings.
Push fittings are rapidly crowding other species. They are mounted simply and quickly, using only a calibrator and a torch. In addition to high reliability, such a connection has another advantage - it can be disassembled, if necessary.
The use of press fittings provides a one-piece connection. The pipe is cut, a crimp sleeve is put on its end, machined by a calibrator. After fitting, the clutch is crimped with press tongs. It is important to remember that it is forbidden to repeat crimping the coupling so as not to render it unusable.
The connection of metal-plastic pipes may be used at a pressure of 10 bar.
Universal connection
In some cases, it is not possible to determine what material the polymer pipes are made of, which need to be joined. In the absence of confidence in what material you have to work with, they resort to a universal method of docking.
Flexible polymer structures are connected using a worm clamp and a plastic hose coupling:
- The rigid part of the hose coupling is inserted into the pipe.
- Having retreated 18-20 mm from the end of the pipe, a worm clamp is installed.
- Rigid plastic products are connected using the following procedure:
- The pipe is cut, the edge is cleaned and leveled, scoring is removed.
- After making a chamfer on the outside of the product, a test assembly is carried out, marking the fixed positions of the assembled elements with a marker.
- Having disconnected a fitting and a pipe, the means promoting the best gluing are applied on a surface.
- The glue is applied with a brush in an even layer.
- The pipe is inserted into the fitting, taking into account the previously applied marking. The joint is clamped for about a minute, allowing the glue to set.
Work with the manufactured compound can be continued after five to ten minutes. Water in the assembled pipeline can be started in an hour, provided that its temperature does not exceed 21º C.
By joining different types of polymer pipes, one can confidently achieve reliability, strength and tightness of joints. In order for the result of the work done to be satisfactory, it is worth considering the conditions in which the pipeline operates. Based on them, the necessary elements are selected, and the docking is carried out in the most acceptable and guaranteeing a long service life way.