A variety of communications that people use can be connected to the central pipelines. The need to crash into a pipe in order to create a new branch arises very often. For example, to modernize pipe structures. To facilitate the work, for a quick and at the same time high-quality tie-in into the pipeline, a part was created that is called a saddle or tie-in collar.
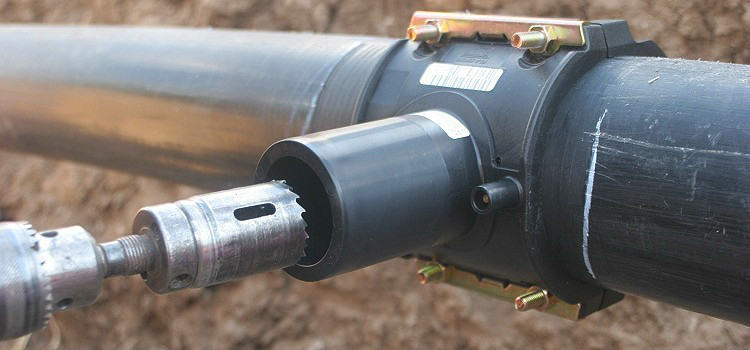
A saddle pin is a part with which you can crash into an existing pipeline and create a branch from it or install additional equipment
Content
Advantages and disadvantages
The saddle is a part consisting of two halves. Due to this, it has the ability to tightly compress the pipe on both sides. Pipe saddles are used in different cases based on need. Such a device allows inserting into a working communication without disconnecting it, which is an incredibly convenient function.
There are compression (mounted mechanically) and electrowelded saddles. The compression saddle is, as a rule, used for pipelines made of steel. The installation of such a device is not difficult, however, is more time consuming than the installation of electric-welded elements.
Helpful information! The most common is their operation in the industrial sector and during the installation of sewer communications with a diameter of 110 mm. Less commonly, these devices are used for tapping into gas pipelines and heat pipes.
Nurses on a steel pipe have a number of positive qualities that allow them to enjoy such popularity in the modern market.
The advantages of using fittings of this type:
- practicality;
- low cost;
- mounting the saddle on the pipe will not cause difficulties and is done at high speed;
- effectiveness and efficiency;
- reliability.
Like any other product, the saddle also has its drawbacks. The negative side of operation is such a factor: the device, although it has high operational performance, but still can not compete with the standard tee for tapping into the pipeline line.
Design and product features
A saddle with a threaded branch consists of several structural elements and is conditionally divided into 2 parts:
- lower half, which is equipped with clamps and belts. They perform a fixative function;
- the upper half, which includes a special pad with a hole. Through this hole, a new branch is docked.
The saddle mounted on a pig-iron or steel pipe is firmly fixed by a clamping bolt. The sealing rubber ring allows to achieve high tightness. There are models that can be mounted using welding. Such products are considered more advanced.
The use of fittings such as herring allows you to reduce financial costs when installing various pipelines, as well as reduce installation time. The nurse is mounted on a steel pipe quite simply.It is fixed in place with elastic fasteners and tightened with bolts. After this, a hole is drilled and the resulting compound is tested.
If the installation of this device is carried out on a pipe made of polyethylene (PE) or low-pressure polyethylene (HDPE), then the process goes even easier and faster. It is necessary to connect the part and the pipeline by diffuse welding and everything is ready.
Varieties of saddles
Nurses, as a rule, are made of different materials and are primarily classified according to this indicator. Consider the basic materials from which these fittings are made:
- low-pressure polyethylene (PND saddles);
- polyethylene (PE saddles);
- steel;
- cast iron (110 mm);
- brass.
In addition to the separation according to the material of manufacture, all saddles into pipes are subdivided according to the design into the following types:
- crimp saddle (in the form of a clamp);
- flanged;
- electric welded;
- branch pipe;
- valve for insertion.
Crimp
Such a product is also called compression. It is produced in the form of a regular clamp and mounted in this way: the pipe is clamped on both sides by halves of the device. One of the halves is equipped with a threaded bend, which is necessary for mounting the transition element on the insert pipe.
Note! The most popular saddles with a threaded branch when installing plumbing communications or irrigation structures. In such systems, they are used in conjunction with compression fittings and ball valves.
This type of fitting can be used for communications from different materials:
- polyethylene (PE);
- polypropylene (PP);
- polyvinyl chloride (PVC);
- asbestos cement.
The maximum temperature of the working medium that is allowed for the use of such saddles is +40 ° C. And the pressure can reach up to 10 atmospheres. The nipple crimping for insert differs in the big assortment of carving exits (from 1/2 to 4 inches) and is used for pipes with indicators of section from 20 to 315 mm.
Flange
Such models are installed mechanically, that is, without the use of electrodiffusion welding. Saddle flanged, as a rule, are used for metal and cast-iron communications. At the same time, they have practically no differences from crimp saddles.
The only feature of such devices is the presence of a flange hole, which allows the supply of pipes. The size of the outlet of the steel pipe may have different indicators depending on the specific case. A compression saddle can also have a flange bend, such a product is the most popular in the industrial field, which affects its size.
Electric welded
An electric-welded part with a mill is used to insert pipes into the HDPE. Installation of such clamps for tapping is carried out by electrodiffusion welding. In order to carry out quick and convenient installation, such models are equipped with a special spiral that heats and melts the pipe and part in the right place, resulting in a reliable and tight connection.
The adhesion of the part and the pipe using electrodiffusion welding is very reliable and can withstand pressures of up to 16 atmospheres (if the working medium is a liquid) and up to 10 atmospheres with a gaseous working medium.
Spigot
Such devices are made without a cutter and a locking mechanism.Installation of the nozzle-lining is also carried out using electrodiffusion welding, however, in this case, the insert is carried out only in idle communications. Parts can have cross-sectional indicators from 50 to 1200 mm and output bends for connecting communications from 32 to 315 mm.
Tapping valve
This device allows pressure tapping. He is able to control the flow of the working medium of the secondary pipeline. Control is carried out thanks to a special telescopic extension cord. Valves for tapping under pressure can have the following cross-sectional indicators - from 32 to 315 mm. And the diameter of the outlet can be from 32 to 63 mm.
Saddle Tips
If you decide to purchase such a product, then you should pay attention to advice on their choice. The difference between the different types of these devices from each other is quite insignificant, so their choice is not particularly difficult. Consider tips for choosing the right saddle:
- if the product will be installed on polyethylene or HDPE pipes, then in this case it is recommended to choose a part with an overlay of the same material. An ideal option for such communications is a saddle for inserting a polyethylene. Such a saddle is mounted on the PND pipe quickly and effortlessly by welding.
Important! for pipeline communications, differing in their dimensions, as a rule, products with appropriate diameters are selected. In this case, even slight differences in size are not allowed.
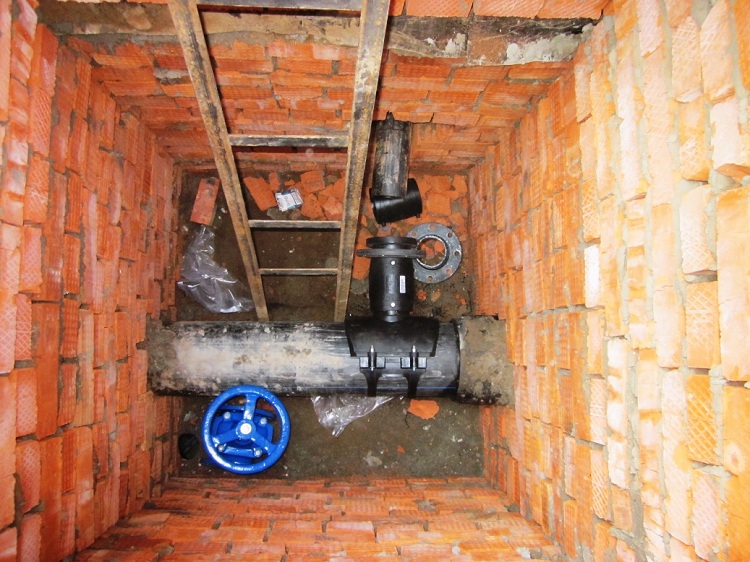
The type of saddle depends on the material from which the pipes are made and the destination of the line
- the most unreliable are crimp models without tight rings. The purchase of such devices is made only if you are sure that you can mount them correctly.
Nurses are mounted depending on the need and can be installed on a working communication. Some models are installed on communications, which are under quite a lot of pressure. Insertion into the pipeline under pressure is most often carried out at enterprises of various kinds, and not at home. Do not forget that other models have their own, albeit minor, design features. This is reflected in their sidebar. For example, a compression saddle is mounted differently, unlike an electric welded product.
Consider the basic steps for installing a crimp model:
- First, we block the pipeline section.
- We clean the pipe, followed by degreasing its outer surface.
- Set the saddle to the surface and adjust its position.
- We fix the part with bolts.
- We take the time to verify the installation, and then finally tighten the fastener.
- We make a hole in the pipe of the required size.
Stages of installation of electric-welded products:
- If necessary, block the pipeline.
- By scraping, we remove 1-2 mm of material from the outer surface of the pipe in the place where the fitting will be mounted.
- An important part of the action is again cleaning and grinding the pipe at the installation site. Performing these actions is a must.
- Using the fixing straps, we install the part on the pipe.
- We tighten special fixing belts to fix the product in the desired position on the pipe.
- We mark the start time of electrodiffuse welding.
- We connect the saddle terminals with the wires of the welding equipment.
- We wait until the welding of the pipe with the fitting is completed.
- In the pipe we make a hole of the required diameter.
- At the end, we remove the fixing belts and the rest of the auxiliary equipment.
Modern industry offers many devices for tapping into pipelines. The simplest and most practical tool is a saddle, which can be installed on a pipe of any type.