Quite often, the existing water supply system requires expansion in order to connect additional plumbing or create a new circuit. When tapping into a water pipe, it is necessary to comply with safety regulations and a strict sequence of steps. If there is no possibility of overlapping water, then the insertion occurs under pressure.
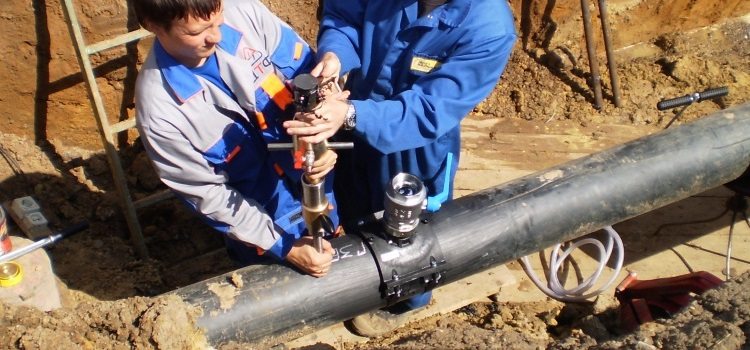
It is possible to make an insert into the water supply system without disconnecting the line, but this requires special connecting parts and equipment
Content
Coordination and permission to work
In order to crash into water pipes both without welding and with its use, it is necessary to obtain all the required permits and documents.
Note! Carrying out an illegal tapping into a pipe entails administrative and material liability.
First you need to get a site plan to find out if there are any communications underground. This paper, together with title documents (at home, land) is fed to the water utility branch. The resulting technical specifications for the connection include:
- connection place;
- diameter of the pipeline;
- other data depending on the purpose of the frame.
Next, the necessary data are submitted to the SES and the development and registration of design and estimate documentation is carried out. Self-installation of metering and tapping into a pipe under pressure is strictly prohibited. To perform such work, you must contact the specialists.
It should also be remembered that the inset is forbidden to bypass metering devices, to the large-diameter trunk network that feeds the house, to the pipeline without a connection to the central sewer system, to the water supply system of any diameter, unless permission is obtained for any type of work.
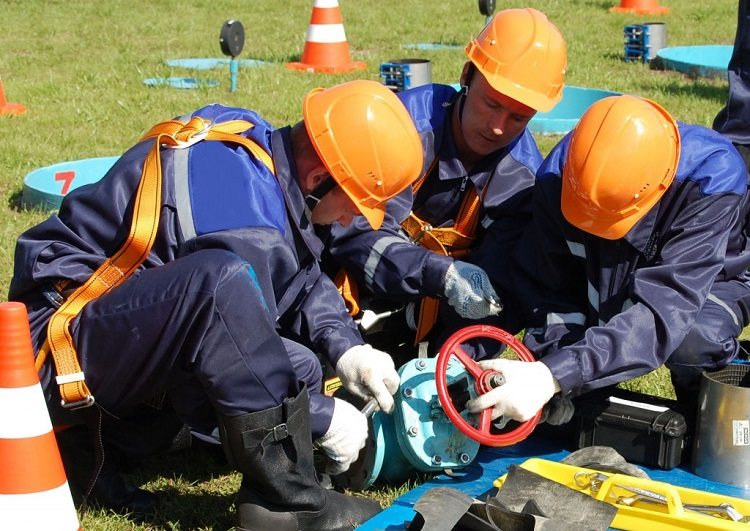
It is better to entrust the work to the development of the project, preparation of materials and the implementation of the insert
The essence of the insertion process
The choice of how to crash into a water pipe depends on its material. Modern systems are built on plastic, metal, metal-plastic and, less commonly, on cast-iron pipes. For insertion, a hole is required. It is clear that when the process is performed under pressure, water will flow from the pipe. Therefore, special clamps are used for work, the design of which depends on the material of the pipes.
There are two most general rules that you must follow when inserting:
- Equality of the inner diameter of the cut-in pipe and the diameter of the drill.
- The pipe to be cut must have a smaller diameter than the one in which the hole is made.
The process of tapping into the pipeline depends on the type of water supply. The most common technologies are welding and the use of clamps. Clamps are necessary in cases such as a pressure tapping into a water pipe or in the absence of the possibility of cutting a trunk. Work on pipes with polyethylene pipes excludes the use of gas and electric welding.
When using welding, an additional coupling or thread is welded to the pipe, and a root tap is mounted on these connecting elements. In this case, the water supply must be turned off and the water released.
Piping Stages
The main tool that will be required for work is a special mechanism for drilling water pipes under pressure. This method is quite productive and operational if you comply with safety regulations and comply with all technological steps.
First, the insulation is removed and the surface of the pipe is cleaned. Next, a flange is installed with an outlet to the feed pipe and secured with a clamp. A mechanism for drilling is mounted to a valve that connects to the flange.
Note! If the water supply is steel, then the installation of the apparatus for drilling is carried out not on the clamp, but on the welded pipe.
After the welding process, the seam is checked for defects. If necessary, it can be cooked again.
Then, through the open valve, a mill of the required diameter is introduced and a hole is cut. At the last stage, the drilling equipment is removed, blocking the water supply from the nozzle, and the insulation and anti-corrosion coating are restored. This sequence of steps is applicable for pipes made of cast iron and metal.
Varieties of clamps
Clamps come in various designs and configurations. The most popular are:
- clip;
- saddle clamp;
- drill collar;
- electrowelded saddle clamp.
The use of a clip holder is possible for tapping into the water main, which is not under pressure. Structurally, it consists of a pair of parts, one of which has a threaded bend. The clamp is bolted and can be made of plastic or metal.
A saddle clamp is used to insert under pressure into a pipe made of metal, asbestos cement or plastic. It is attached to the pipeline using a bracket. Often such a clamp is made of metal and has a locking plate or a special mechanism.
The drill collar is used for tapping into a pipe under pressure. In addition to it, nozzles, as well as rotary connectors, can go. To install the clamp on a steel, cast iron and plastic pipe, special equipment is required.
The design of the drill collar includes a butterfly valve. Subsequently, it is applicable as shut-off or control valves.
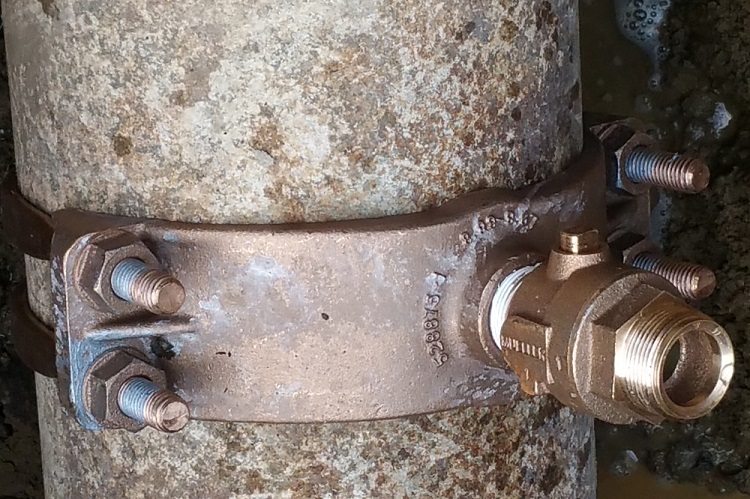
The clamp for insert is selected depending on the purpose of the branch and the material of the main pipe
The saddle clamp is used for tapping into a plastic pipe. The design includes a milling cutter for making holes and a heating coil. The case of such a clamp is made of special plastic and additional equipment is required for its installation.
Insertion into the main pipeline
The tap from the main pipeline under pressure is implemented in 3 stages:
- Excavation.
- The insertion process.
- Execution of water supply diversion.
At the excavation stage, a pit digging with dimensions of 1.5 x 1.5 meters is being excavated. Its bottom falls half a meter below the pipe. You can dig first with an excavator (to a metal or polymer tape laid above the pipe at a distance of 300-500 mm), then with shovels. If the tie-in point is in the well, this step is excluded.
Using a hole in the saddle or collapsible clamp, the reinforcement body is punctured. A similar pairing element is similar to a tee. A shut-off valve is screwed onto the lateral outlet, which, after a puncture, blocks the flow of water.
For mounting on plastic pipes, you can use ordinary saddle clamps or saddle holders.
Note! The optimal version of the saddle for pipes made of polymer is an electric-welded collapsible collar. Dismantling into 2 parts, it is installed above the insertion point and soldered to the pipe body using a welding machine. Thus, a high-strength and tight connection is obtained.
The withdrawal of the water supply line from the highway is the final stage of the process. The beginning of a new pipeline is located on the valve of the saddle, and its end is on the water flow meter.
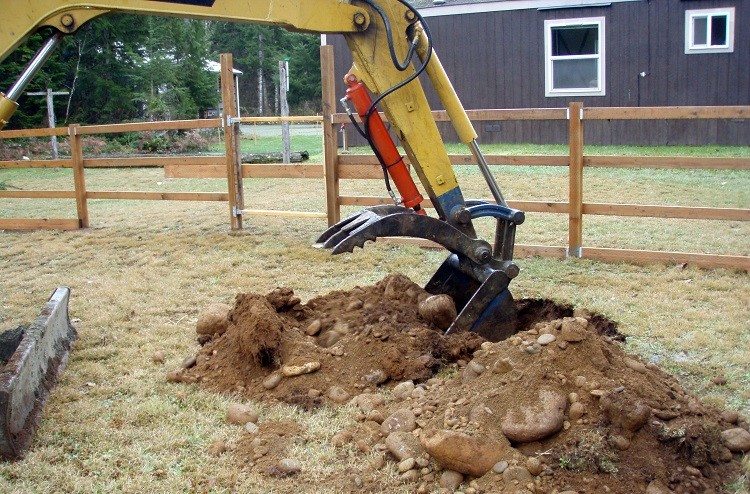
If an insert into the underground communications is needed, then first you need to dig a hole in the place where the pipeline is located
Well arrangement rules
To simplify the operation of the branch, a well (caisson) is installed above the insertion point. Its arrangement begins with a pit deepening of 50-70 cm. The places of the selected soil are filled with a 20 cm thick gravel cushion. A ruberoid is rolled out over the gravel and a 10 cm thick concrete slab is poured, which is strengthened by a reinforcement grid.
To achieve concrete strength up to 70%, 3-4 days are needed. After that, a mine of blocks is built above the stove. At the same time, its neck rises to zero level. The shape of the shaft can be square or round.
A cast plate with a round hole for the hatch is laid on the neck of the mine. At the final stage, the vertical insulation of the outer surface of the mine is arranged with a coating compound, and the foundation pit is filled up with selected soil.
Well construction requires a lot of time and cost. For this reason, it is better to insert a water pipe into the caisson than to divert from the underground part of the highway.
Insert in a metal plumbing
For insertion into a metal pipeline, a saddle clamp with drilling is used. There are several varieties of it. Before installing the device on the pipe, it is thoroughly cleaned of rust and dirt (if any). In addition to the lower part in the form of a semicircle, in the upper part the clamp has a shut-off valve with a hole designed for drilling and directly a drill. When placed on the pipe, the parts are fastened together by bolts.
Note! To ensure a snug fit to the surface of the water supply there are sealing gum.
After fixing the clamp, a hole is drilled and closed with a plug using a special screw. A similar clamp can be used as a stop valve. You can also take a clamp with a valve already screwed in. After the hole is ready, the drill is pulled out and the valve is closed. Further, other necessary installation work is performed.
A special machine consisting of a handle with a ratchet, a locking bolt, a shaft with a drill at its end and a flushing valve can be attached to the metal clamp. All elements are enclosed in a metal casing, which is attached to the clamp using sealing rubber bands. Thanks to the presence of a guide sleeve, it is possible to drill in a certain direction. So the insert is made into a cast iron or metal water pipe.
Insert in the pig-iron pipeline
In order to drill a pig-iron pipe under pressure, clamps with a special design and bimetallic crowns are used. When performing work, it is necessary to take into account such moments:
- brittle cast iron, so work should be carried out with a light pressure;
- before drilling, the surface of the pipe is cleaned of the layer that is applied to prevent corrosion;
- overheating of the crown is unacceptable;
- work is carried out at low speeds.
After removing the compacted layer, a collapsible saddle is mounted on the insertion point. The contact area is sealed with rubber pads. The pipe is drilled with a carbide crown, which will need to be changed at least 3-4 times during the insertion process.
The procedure for inserting into a cast-iron water pipe is as follows:
- dig a pipe, clean it of rust at the point of cutting;
- cut off the upper layer of hot iron with a grinder;
- mount a collapsible saddle, put a rubber sealant to seal the joint between the valve and the clamp;
- attach the shut-off valve to the flange branch, through which the crown will be inserted (cutting tool);
- drill a cast-iron pipe, cooling the place of cut;
- remove the crown from the valve and block the flow of water.
It is also necessary to remember about ensuring a slope of the saddle nozzle in the direction of the house at 2 degrees.
Insertion into the plastic pipeline
Crashing into a plastic pipe without reducing the pressure on it is possible with the help of an electrically welded clamp-saddle. It is made of special plastic and has a heating coil with a drilling mechanism. On the case of such a clamp there is a bar code that allows you to enter the welding parameters with the necessary accuracy.
This method is applicable for pipelines with pressure up to 1.6 MPa.
Note! The saddle clamp is resistant to corrosion and will last a very long time (up to 50 years).
The pipe is pre-cleaned and a clamp is fastened to it with bolts, which has terminals for connecting the welding machine. The spiral is heated by the welding machine and the branch is welded.
Currently, a saddle with a built-in cutter and valve is often used. For this, a coupling is used to make a tie into the water supply system by welding. Approximately 1 hour after complete cooling, the cutter makes a hole and the shut-off valve is screwed.
Welding of the pipe to the steel water pipe should only be done by professionals. Installation of saddles on a cast-iron or polymer pipeline can be done independently, but it should be ensured that the water supply is shut off. Pressure tapping works must be carried out taking into account all the rules and recommendations, otherwise such work can be dangerous.