This type of shutoff valve is made in the form of a valve. The locking element moves parallel to the flow direction of the medium passing through the pipes. Unlike the shut-off and control device, the shut-off valve can only be in two extreme positions - “open” or “closed”. The use of such plumbing fixtures provides reliable sealing of the locking structure.
Kinds and advantages
These products are usually classified according to several criteria.
Depending on the installation method in the system, shut-off valves are divided into:
Coupling. Designed exclusively for threaded mounting. Therefore, the ends of the valve locking coupling are designed for internal or external thread. Shut-off valves of this type are made of brass or steel. In the first case, it is used only in domestic pipelines. Moreover, both brass and steel valves are installed in the mains with a low pressure of the working medium - up to 15.792 atmospheres (1.6 MPa). There is another design of such plumbing fixtures. So, today you can buy a brass locking coupling valve for installation on threaded crimp fittings;
Flanged. The body of the flange part is made of steel or cast iron. Its installation is carried out in a completely different way. The main ends of the body of this armature end with flanges. This design is more durable. Therefore, engineering communications with an average pressure level of 10 MPa are a priority area of application for a shut-off flanged valve. This feature allows the use of these devices in industrial and municipal trunk pipelines. Flange mounting on pipes with a diameter of 10 ≤ D ≤ 1600 mm is practiced.
The design of the ends is not the only difference between the above types of valves. The flange valve is much larger compared to its coupling counterpart. In numbers, it looks like this: the size of the flanged valve can reach 300 mm, while the size range of the coupling products ends at 63 mm.
In addition to these two groups of locking parts, there is also a third variety - valves, the design of which is designed for welded installation. Their main ends are designed in the form of smooth pipes. The scope of application of a welded shut-off valve is industrial pipelines operating under a pressure of more than 10 MPa.
Depending on the design of the valve body, there are:
Corner Two pipes arranged perpendicular to each other are connected. Angle shut-off valve has the following advantages:
- the efficiency and simplicity of the design make it easy to operate and repair the product.
- in comparison with a gate valve - a small construction height;
- shutting off the flow of working media is ensured by the low stroke of the crane.
On a note! The perpendicular arrangement of the nozzles at the inlet and outlet, among other things, allows to reduce the excess hydraulic pressure present in the system.
Walkthroughs. Such products are mounted on a horizontal or vertical node of the pipeline.There are two types of gate valve design: bellows (with a high degree of tightness) and stuffing box. Of the shortcomings of such a detail, experts distinguish:
- high hydraulic resistance;
- quite a lot of weight;
- the complexity of the design of the housing. This leads to the fact that, to facilitate manipulation, the straight-through valve is often equipped with an electric drive;
- large construction dimensions;
- the presence of a stagnation zone. Rust particles can accumulate there, which usually leads to corrosion.
The body of the shut-off in-line coupling valve has 2 fittings on which an internal or external thread is cut. In the latter case, the sleeve is screwed onto the body, and its free end is mounted in the pipe bend. If there is an internal thread on the shutoff valves, the connection to the pipe is carried out by screwing the run-in into the body of a passage steel or brass shut-off valve.
Direct-flow. In appearance, a device of this type is similar to a gate valve, but is longer and much larger in size. Its design is characterized by the fact that the nozzles are located opposite to each other. The flow control in this shut-off valve is carried out due to the lateral movement of the passage element when the seat of the device is aligned with the boundaries of the passage hole. The undoubted advantage of such valves is the absence of stagnation zones and low hydraulic resistance.
Types of locking elements
Modern industry produces valves with three types of locking elements. Actually, their form is the basis of the generally accepted names of these details:
- cylindrical;
- conical;
- ball.
The cones are slowly losing their former relevance. They, in fact, were replaced by the other two types of valves. The reason for this was the presence of the following disadvantages in cone valves:
- To control the flow of water, a significant amount of torque must be applied.
- conical plug due to rapid wear requires constant grinding and adjustment.
But valves with cylindrical and ball locking elements are firmly established in the leading positions in this segment of the plumbing market. This is due to the simplicity of the design, which does not provide for additional maintenance during operation. However, there are some nuances. So, for example, the shutter of a cylindrical valve is not pressed close to the seat, which does not provide a high degree of tightness. Therefore, it is better to use such devices to control the flow on any intermediate segments of the highway, and not to completely block it.
The spherical locking element of the ball valve has a through hole and is installed in a direct-flow housing.
On a note! In most cases, direct-flow valves equipped with ball valves perform the functions of only stop valves. Flow control with their help is quite complicated.
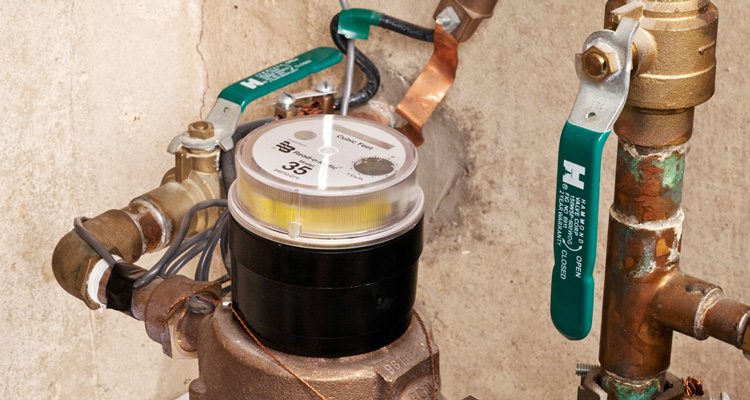
Ball valves are most often used to shut off or supply working fluid, for example, on water risers in houses
The movement of water is opened by turning the handle until the longitudinal axes of the body and the through hole are combined. In order to block the flow, the passage hole must be deployed in the direction perpendicular to the axis of the housing.
Valve Replacement
Owners of apartments in houses commissioned more than 15 years ago are often forced to deal not only with replacing the valve in the riser, but also with the revision of all valves.Performing such work is not difficult, but without the presence of locksmith tools (wrenches, screwdrivers, flax) and certain skills you can not do here.
All risers are common property, therefore, the management organization must carry out the replacement of their components. However, in practice, it is very difficult to get the provision of such services from her. It is sometimes easier to do this work with your own hands.
First, a suitable stop valve is selected. Here you need to listen to the opinion of professionals. Regardless of whether it is a question of replacing the valve with cold or hot water, they advise you to opt for ball-type devices. The reason lies in their durability and high reliability. And even if such a valve fails, it will be very easy to make its next replacement.
Before proceeding with valve replacement, the riser must be closed. If there is unhindered access to the basement, you can do it yourself. Otherwise, you have to write a statement to the managing organization.
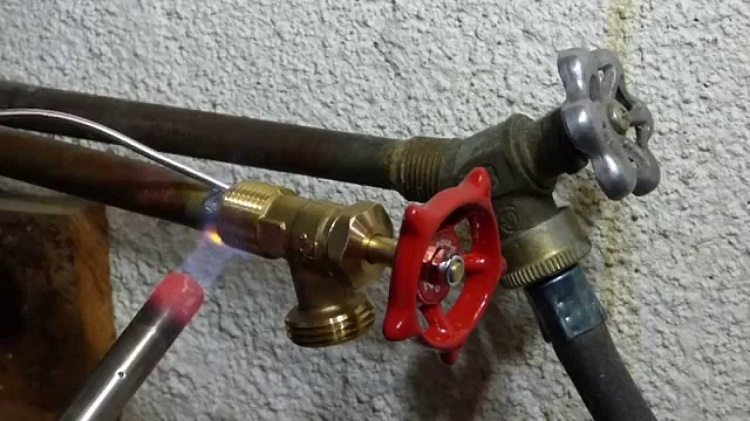
The complexity of installing or replacing a shut-off valve depends on the type of pipe and type of connection.
After the riser is closed, water is drained. Dismantling of old valves must be done very carefully to prevent damage to the pipe and the threads present on it.
Having done this, wrap the FUM tape or linen on the pipe thread. So you increase the tightness of the joints and eliminate the possibility of undermining, which in the future will certainly grow into leaks.
Turn the valve onto the pipe without rushing so that it does not skew, due to which the thread may be damaged. When mounting, pay attention to the location of the handle of the locking device. She should stay at the top. Otherwise, it will be very difficult to shut off the water in the future. Do not overtighten the nuts so that the pipe body does not burst. At the end of work, apply silicone sealant to the joints.