Polyethylene products are used for pipelines for various purposes. Technical and operational characteristics allow the use of PE products for laying cables and power lines, transporting gas and liquids. Polyethylene communications have proven themselves in the installation of sewers, drainage systems and pressure pipes. The parameters and properties of the pipe are regulated by GOST.

Polyethylene pipes are products that are widely used for the installation of water, gas pipelines, sewers and other communications
Content
- 1 The use of plastic products
- 2 Overview of GOSTs on PE pipe
- 3 Characteristics of PE (GOST 16338)
- 4 HDPE pipe production
- 5 PE pipe dimensions as per document 32415
- 6 Limit deviations in the size of polyethylene pipes
- 7 Basic design ratios
- 8 Technical requirements according to GOST 32415
- 9 Durability parameters of pipe joints
- 10 Sizes of sewage products made of polyethylene
- 11 Technical parameters of sewer pipe
- 12 Weight of polyethylene pipe for sewage
- 13 Characteristics of gas pipes
- 14 HDPE pipe for cable
- 15 Assortment of technical pipes
- 16 Advantages of HDPE pipes over steel
- 17 Features of marking HDPE pipes
- 18 PE heat resistant
- 19 Crosslinked Polyethylene Properties
- 20 Crosslinked Polyethylene Parameters
The use of plastic products
There are pipes made of polyethylene (P) high (B) and low (H) pressures (D). LDPE products have a limited area of use. Typically, pipelines for drinking water or other liquid media are built on their basis. LDPE pipes can be laid in the ground without the use of additional shells for protection.
High hardness, density, low combustibility, flammability, and dielectric properties of HDPE pipes make it possible to take them as the basis of sewer systems, water pipelines (both drinking and industrial water), gas pipelines, industrial pipelines, for laying cables and wiring elements.
LDPE is performed at elevated pressure. Its melting point is about 110 degrees. Gas and moisture permeability of PND products is five times less than LDPE. They are great for outdoor piping.
Overview of GOSTs on PE pipe
There are several standards (GOSTs) for polyethylene pipes. Each document defines the main characteristics, features, assortment and other important properties of products. So, we can distinguish GOST 18599, GOST 22689, GOST 32415, GOST 50838. The properties of PE as a material are prescribed in standard 16338, approved in 1985.
Document 18599-2001 applies to pressure pipeswhich are divided into 3 types:
- PE products with possible presence of marking strips.
- PE pipes having coextrusion layers of the same MRS level (minimum - "minimum", required - "long", strength - "strength") inside and / or outside.
- Polyethylene products with a protective shell made of thermoplastic.
GOST 22689, approved in 2014, establishes the technical parameters of shaped elements and PE pipes for an internal water drainage and sewage system. Document 50838 outlines the requirements for PE pipes for transporting gas, which is used as fuel and raw material in industry or municipal services.
Note! According to the standard 18599, products for laying cables are produced.
GOST 32415 was approved in 2013 and applies to thermoplastic products, including polyethylene, pressure type for heating, cold water supply and connecting elements (fitting) to them.
Characteristics of PE (GOST 16338)
Regulatory document 16338 regulates the technical performance of HDPE (high density), which is obtained by gas-phase or suspension method of ethylene polymerization (C2N4) at low pressures.
Also indicated are compositions and brands of PE permitted for the production of products in contact with drinking water, food, pharmaceuticals and cosmetics, and other purposes. Pipes and films should be made of gas-phase compositions of the first and highest grades or suspension - of the second and first grades.
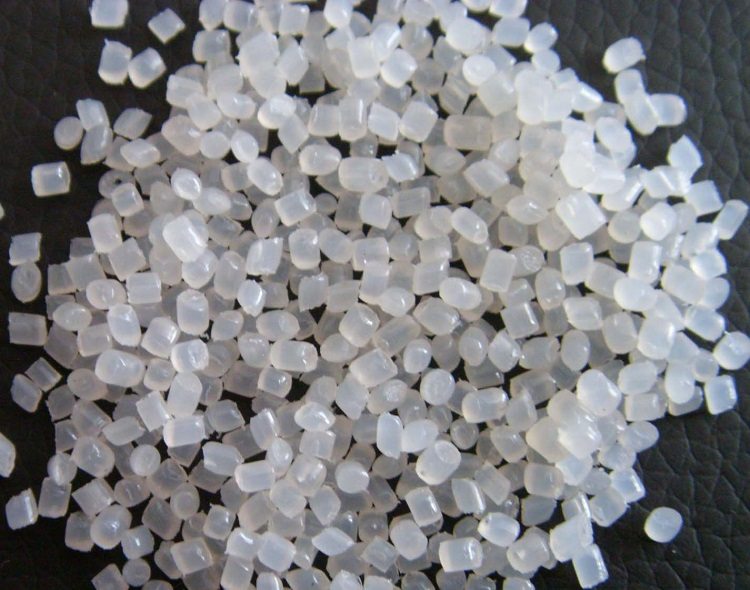
GOST regulates the composition of the raw materials used for the production of a particular type of pipe
The document sets the maximum concentration of harmful substances that can be released into food, water or air. The corresponding values are given in the table.
Table 1
Product name | Permissible concentration, mcg / m3 | Hazard class (GOST 12.1.007) |
Formaldehyde | 500 | 2 |
Acetaldehyde | 5 thousand | 3 |
Carbon monoxide | 20 thousand | 4 |
Organic acids (converted to acetic acid) | 5 thousand | 3 |
Aerosol PE | 10 thousand | 3 |
HDPE (according to GOST 16338) is a combustible material. At room temperature, it does not emit harmful substances into the environment. During processing, when values exceed 140 degrees, volatile products that contain organic acids may be released.
HDPE pipe production
GOSTs on polyethylene products for cables, water supply, sewage, gas, regulate not only the technological process for the production of semi-finished HDPE, but also pipes. So, according to the standard 18599, there are two ways to obtain the final product:
- extrusion;
- casting.
By extrusion is meant extrusion of a pipe from granules in a molten state. The product obtains the required shape thanks to the extruder head. In this case, the superheated polymer is pushed by the press.
The pipe is obtained by casting using a rotating mold, to the walls of which molten material sticks.
Note! This process is more complicated than extrusion, but it is possible to obtain more accurate HDPE pipes with minimal deviations and ovality.
There is another way to get the pipe - pneumatic formation. In this case, the polymer is fed into the mold under pneumatic pressure, as a result of which a PND product is formed.
Depending on the selected type of production and raw material features, you can get the final product with various technical characteristics. HDPE pipes, GOSTs that regulate their parameters, specific application conditions - all these are important issues that require special attention when it is necessary to equip a pipeline for gas, water, cables, etc.
PE pipe dimensions as per document 32415
GOST for pipes (polyethylene) for water supply determines the main dimensions of the products. The corresponding values from the standard are given in the table. SDR (СРО) - standard ("standard") dimensional ("dimension") relation ("ratio").
table 2
Polyethylene grade | 80 | 80, 100 | ||||||||
Series 2.5; SRO 6 | Series 3.2; SRO 7.4 | Series 4; SRO 9 | Series 5; CPO 11 | 6.3 series; SRO 13.6 | Series 8; CPO 17 | Series 10; SRO 21 | Series 12.5; SRO 26 | Series 16; SRO 33 | Series 20; CPO 41 | |
Diameter, * 103 mm | Pipe wall, * 10-1mm | |||||||||
0,016 | 30 | 23 | 20 | — | — | — | — | — | — | — |
0,020 | 34 | 30 | 23 | 20 | — | — | — | — | — | — |
0,025 | 42 | 35 | 30 | 23 | 20 | — | — | — | — | — |
0,032 | 54 | 44 | 36 | 30 | 24 | 20 | — | — | — | — |
0,040 | 67 | 55 | 45 | 37 | 30 | 24 | 20 | — | — | — |
0,050 | 83 | 69 | 56 | 46 | 37 | 30 | 24 | 20 | — | — |
0,063 | 105 | 86 | 71 | 58 | 47 | 38 | 30 | 25 | — | — |
0,075 | 125 | 103 | 84 | 68 | 56 | 45 | 36 | 29 | — | — |
0,090 | 150 | 123 | 101 | 82 | 67 | 54 | 43 | 35 | — | — |
0,110 | 183 | 151 | 123 | 100 | 81 | 66 | 53 | 42 | — | — |
0,125 | 208 | 171 | 140 | 114 | 92 | 74 | 60 | 48 | — | — |
0,140 | 233 | 192 | 157 | 127 | 103 | 83 | 67 | 54 | — | — |
0,160 | 266 | 219 | 179 | 146 | 118 | 95 | 77 | 62 | — | — |
0,180 | 299 | 246 | 201 | 164 | 133 | 107 | 86 | 69 | — | — |
0,200 | 332 | 274 | 224 | 182 | 147 | 119 | 96 | 77 | — | — |
0,225 | 374 | 308 | 252 | 205 | 166 | 134 | 108 | 86 | — | — |
0,250 | 415 | 342 | 279 | 227 | 184 | 148 | 119 | 96 | — | — |
0,280 | 465 | 383 | 313 | 254 | 206 | 166 | 134 | 107 | — | — |
0,315 | 523 | 431 | 352 | 286 | 232 | 187 | 150 | 121 | 97 | 77 |
0,355 | 590 | 485 | 397 | 322 | 261 | 211 | 169 | 136 | 109 | 87 |
0,400 | 665 | 547 | 447 | 363 | 294 | 237 | 191 | 153 | 123 | 98 |
0,450 | — | 615 | 503 | 409 | 331 | 267 | 215 | 172 | 138 | 110 |
0,500 | — | 683 | 558 | 454 | 368 | 297 | 239 | 191 | 153 | 123 |
0,560 | — | — | 625 | 508 | 412 | 332 | 267 | 214 | 172 | 137 |
0,630 | — | — | — | 572 | 463 | 374 | 300 | 241 | 193 | 154 |
0,710 | — | — | — | 645 | 522 | 421 | 339 | 272 | 218 | 174 |
0,800 | — | — | — | — | 588 | 474 | 381 | 306 | 245 | 196 |
0,900 | — | — | — | — | 662 | 533 | 429 | 344 | 276 | 220 |
1,000 | — | — | — | — | 725 | 593 | 477 | 382 | 306 | 245 |
1,200 | — | — | — | — | 882 | 679 | 572 | 459 | 367 | 294 |
1,400 | — | — | — | — | 1029 | 824 | 667 | 535 | 429 | 343 |
1,600 | — | — | — | — | 1176 | 941 | 762 | 612 | 490 | 392 |
Limit deviations in the size of polyethylene pipes
GOST 32415 establishes the permissible diameter deviations and ovality of PE products.
Table 3
Diameter, * 1 thousand mm | Tolerance upward, * 10-1mm | Ovality mm * 10-2 not more |
0,016 | 3 | 120 |
0,020 | 3 | 120 |
0,025 | 3 | 120 |
0,032 | 3 | 130 |
0,040 | 4 | 140 |
0,050 | 4 | 140 |
0,063 | 4 | 150 |
0,075 | 5 | 160 |
0,090 | 6 | 180 |
0,110 | 7 | 220 |
0,125 | 8 | 250 |
0,140 | 9 | 280 |
0,160 | 10 | 320 |
0,180 | 11 | 360 |
0,200 | 12 | 400 |
0,225 | 14 | 450 |
0,250 | 15 | 500 |
0,280 | 17 | 980 |
0,315 | 19 | 1110 |
0,355 | 22 | 1250 |
0,400 | 24 | 1400 |
0,450 | 27 | 1560 |
0,500 | 30 | 1750 |
0,560 | 34 | 1960 |
0,630 | 38 | 2210 |
0,710 | 64 | — |
0,800 | 72 | — |
0,900 | 81 | — |
1,000 | 90 | — |
1,200 | 108 | — |
1,400 | 126 | — |
1,600 | 144 | — |
For the wall thickness of a PE pipe, GOST provides such data (in millimeters).
Table 4
Pipe wall made of polyethylene, * 10-1 | Variation upward in grade V | |
> | ≤ | |
10 | 20 | 0,3 |
20 | 30 | 0,4 |
30 | 40 | 0,5 |
40 | 50 | 0,6 |
50 | 60 | 0,7 |
60 | 70 | 0,8 |
70 | 80 | 0,9 |
80 | 90 | 1,0 |
90 | 100 | 1,1 |
100 | 110 | 1,2 |
110 | 120 | 1,3 |
120 | 130 | 1,4 |
130 | 140 | 1,5 |
140 | 150 | 1,6 |
150 | 160 | 1,7 |
160 | 170 | 1,8 |
170 | 180 | 1,9 |
180 | 190 | 2,0 |
190 | 200 | 2,1 |
200 | 210 | 2,2 |
210 | 220 | 2,3 |
220 | 230 | 2,4 |
230 | 240 | 2,5 |
240 | 250 | 2,6 |
250 | 260 | 2,7 |
260 | 270 | 2,8 |
270 | 280 | 2,9 |
280 | 290 | 3,0 |
290 | 300 | 3,1 |
300 | 310 | 3,2 |
310 | 320 | 3,3 |
320 | 330 | 3,4 |
330 | 340 | 3,5 |
340 | 350 | 3,6 |
350 | 360 | 3,7 |
360 | 370 | 3,8 |
370 | 380 | 3,9 |
380 | 390 | 4,0 |
390 | 400 | 4,1 |
400 | 410 | 4,2 |
410 | 420 | 4,3 |
420 | 420 | 4,4 |
420 | 440 | 4,5 |
440 | 450 | 4,6 |
450 | 460 | 4,7 |
460 | 470 | 4,8 |
470 | 480 | 4,9 |
480 | 490 | 5,0 |
490 | 500 | 5,1 |
500 | 510 | 5,2 |
510 | 520 | 5,3 |
520 | 530 | 5,4 |
530 | 540 | 5,5 |
540 | 550 | 5,6 |
550 | 560 | 5,7 |
560 | 570 | 5,8 |
570 | 580 | 5,9 |
580 | 590 | 6,0 |
590 | 600 | 6,1 |
600 | 610 | 6,2 |
610 | 620 | 6,3 |
620 | 630 | 6,4 |
630 | 640 | 6,5 |
640 | 650 | 6,6 |
650 | 660 | 6,7 |
660 | 670 | 6,8 |
670 | 680 | 6,9 |
680 | 690 | 7,0 |
690 | 700 | 7,1 |
Basic design ratios
According to GOST, a polyethylene pipe can be operated for 50 years at a temperature of the working environment of 20 degrees. These values are inherent in cold water supply.
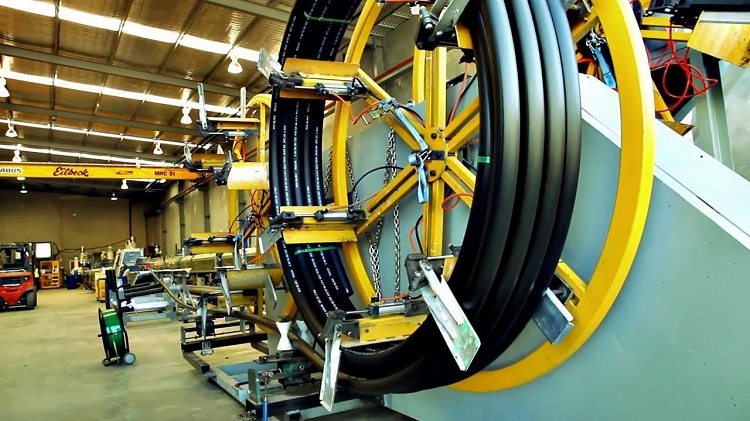
Pipes of small diameter and small wall thickness are most often used for transporting cold water in the domestic environment
For him, the nominal pressure, rated voltage and series of the product are related by this ratio:
D = 10 * N / C = 10 * MRS / S * K,
where K is the safety factor in the form of a coefficient taking into account the operating conditions of the pipeline; C - a series of pipes; MRS is the minimum value of long-term strength, expressed in MPa; N is the calculated voltage (in MPa).
If the pipeline carries water whose temperature is above 20 degrees, then the value of the working pressure is adjusted by entering a coefficient. In this case, the relation
D1 = D * K1,
where D1 - allowable pressure, expressed in bar; D is the nominal pressure; K1 - pressure reduction in coefficient form, the value of which is given in the table.
Table 5
K1 value for polyethylene pipe | Water temperature, degrees |
1,00 | 20 |
0,93 | 25 |
0,87 | 30 |
0,80 | 35 |
0,74 | 40 |
Technical requirements according to GOST 32415
Pipes should be smooth both inside and out. Fulfillment of this requirement is important to ensure a given pipeline throughput. Slight undulation and the presence of longitudinal stripes are allowed.
Note! On the surface there should not be bubbles, shells, foreign inclusions and cracks.
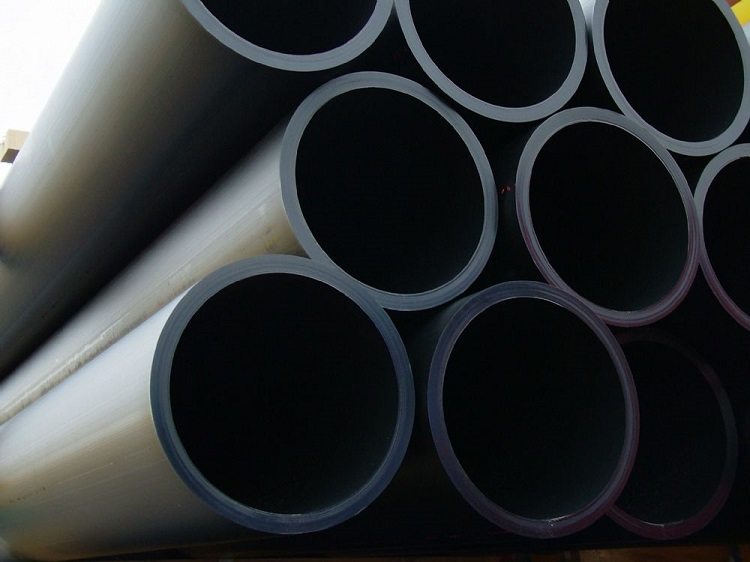
One of the indicators of the quality of PE pipes is the absolute smoothness of the outer and inner surfaces of the products
The resistance of pipes (GOST 32415) to internal pressure is determined during tests, the modes of which are given in the table.
Table 6
No. p / p | Test time, min., No less | Test temperature, degrees | Ring (hydrostatic) stress for the brand PE, kPa | |
100 | 80 | |||
1 | 6 thousand | 20 | 12 thousand | 10 thousand |
2 | 165*60 | 80 | 5400 | 4500 |
3 | 60 thousand | 80 | 5 thousand | 4 thousand |
With plastic failure for the second mode, the tests are repeated under the conditions specified in the table.
Table 6
PE brand 100 | PE brand 80 | ||
Hydrostatic stress, kPa | Time h | Time h | Hydrostatic stress, MPa |
5400 | 165 | 165 | 4,5 |
5300 | 256 | 233 | 4,4 |
5200 | 399 | 331 | 4,3 |
5100 | 629 | 474 | 4,2 |
5 thousand | 1 thousand | 685 | 4,1 |
— | — | 1 thousand | 4,0 |
Water pipes can be extended after heating by a temperature of 110 ± 2 ºС by no more than 3%. The tests last 60 ± 2 minutes for products with a wall of up to 8 mm, 120 ± 2 minutes - from 8 to 16 mm and 240 ± 2 minutes - more than 16 mm. At break, the elongation of the pipe grades 80, 100 is not less than 350%. The change in PTR compared with the initial one is not more than 20 percent, thermal stability at a temperature of 200 degrees is not less than 20 minutes.
Durability parameters of pipe joints
Polyethylene pipes connected by fittings must meet the requirements of the standard. The welded joint of products and its technical parameters of resistance are checked during tests with a temperature of 80 ° C for at least 165 hours at a hydrostatic (ring) voltage of 5.4 MPa (for PE 100) and 4.5 MPa (for PE 80).
Mechanical joints of pipes made of polyethylene are checked under the conditions indicated in the table.
Table 7
Test design | Pressure bar | Temperature degrees | Test time, not less than, h |
No bending PE pipe | 1.5 * nominal pressure | 20 | 1 |
With a bend | 1 |
Mechanical joints are also subject to verification of resistance to tensile load (at a temperature of 20 degrees for at least an hour), which is calculated by the formula:
PH = 1.5 * N * π * (ND-TS) * TS,
where RN - tensile load, N; N - permissible voltage: 8 MPa (for PE 80), 10 MPa (for PE 100); ND - nominal value of the outer diameter, mm; TS - the average wall thickness, mm.
The bending radius can be 15 outside diameters of the pipe (in mm) if the nominal pressure is ≤10 and 20 outside diameters if more than 10. Nominal pressure should be selected from the table.
Table 8
Series | SDR | Nominal pressure for polyethylene grade, * 10-1 | |
80 | 100 | ||
20 | 41 | 32 | 40 |
16 | 33 | 40 | 50 |
12,5 | 26 | 50 | 60 |
10 | 21 | 60 | 80 |
8 | 17 | 80 | 100 |
6,3 | 13,6 | 100 | 125 |
5 | 11 | 125 | 160 |
4 | 9 | 160 | 200 |
3,2 | 7,4 | 200 | 250 |
2,5 | 6 | 250 | — |
If used for the connection compression fittings, then the test pressure shall correspond to the values in the table (symbol: NI - nominal pressure).
Table 9
Temperature test degrees |
Time, h, no less | Pressure, bar, for fittings made of | ||||
PP-R | PP-B | PP-H | POM | ABS | ||
20 | 1 thousand | 1.2 * ND | 1.5 * ND | |||
40 | 0.8 * ND | 1.1 * ND |
Sizes of sewage products made of polyethylene
Sewer pipes (GOST 22689) are characterized by the dimensions indicated in the table.
Table 10
Nominal size, * 10-1 mm | Outer diameter (nominal) * 10 mm | The average value of the outer diameter, * 10-1 mm | |
maximum | minimum | ||
320 | 3,2 | 323 | 320 |
400 | 4,0 | 404 | 400 |
500 | 5,0 | 505 | 500 |
630 | 6,3 | 636 | 630 |
750 | 7,5 | 757 | 750 |
800 | 8,0 | 808 | 800 |
900 | 9,0 | 909 | 900 |
1 thousand | 10,0 | 1009 | 1 thousand |
1100 | 11,0 | 1110 | 1100 |
1250 | 12,5 | 1262 | 1250 |
1600 | 16,0 | 1615 | 1600 |
2 thousand | 20,0 | 2018 | 2 thousand |
2500 | 25,0 | 2523 | 2500 |
3150 | 31,5 | 3179 | 3150 |
The standard also sets the wall thickness.
Table 11
Outer diameter (nominal) * 10 mm | Wall, * 10-1 mm | |||
For 12.5 series | For series 16 | |||
maximum | maximum | minimal | minimal | |
3,2 | 35 | 30 | 35 | 30 |
4,0 | ||||
5,0 | ||||
6,3 | ||||
7,5 | ||||
8,0 | 36 | 31 | ||
9,0 | 41 | 35 | ||
10,0 | 44 | 38 | 38 | 32 |
11,0 | 49 | 42 | 40 | 34 |
12,5 | 55 | 48 | 45 | 39 |
16,0 | 71 | 62 | 56 | 49 |
20,0 | 87 | 77 | 71 | 62 |
25,0 | 108 | 96 | 87 | 77 |
31,5 | 136 | 121 | 109 | 97 |
Other wall thicknesses of products are also acceptable at any point, but not more than 1.25 of the minimum limit.
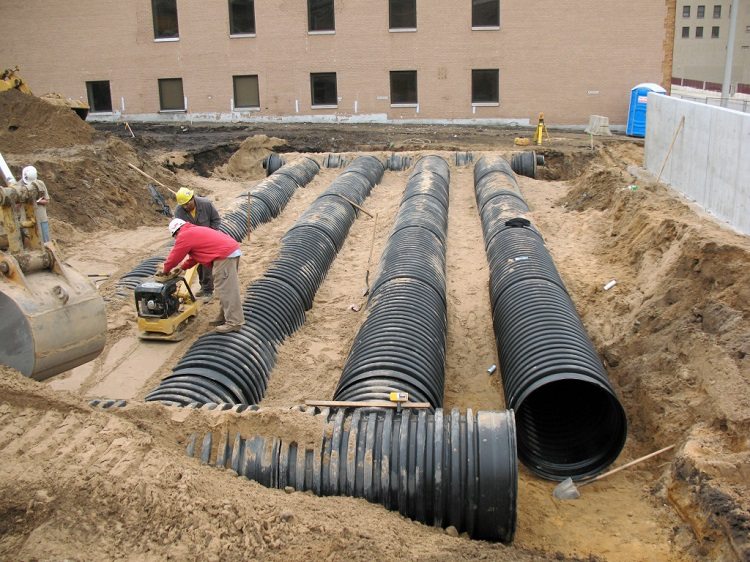
For installation of pressure head sewer systems, smooth and corrugated pipes with thick walls are used
Technical parameters of sewer pipe
A polyethylene pipe (GOST 22689) for sewage after heating can be extended by no more than 3%. In this case, the appearance of cracks or bubbles is unacceptable. Change PTR for pipes that are designed for butt welding - no more than 2 * 10-1 g / 10 minutes.
If connection should be pipes and fittings with a sealant, then water tightness without leaks at a pressure inside 0.05 MPa should be within 15 minutes, and air tightness at a pressure of 0.01 MPa within 5 minutes. PTR indicators for products comply with GOST 11645.
Note! The document allows the addition of recycled material bearing the same brand in the composition.
HDPE pipes have a high degree of rigidity due to their crystal structure. They are characterized by high strength, density, low modulus of elasticity. The main document for a pressure head sewer pipe (PND) is GOST 18599.
Weight of polyethylene pipe for sewage
GOST 18599 establishes the mass values of 1 meter of the pipeline from PE products.
Table 12
Outer Diameter * 103 mm | Mass g | ||||||||
SRO - 41, series 20 | SRO - 26, series 12.5 | SRO - 21, series 10 | SRO - 17.6, 8.3 series | SRO - 17, series 8 | SRO - 13.6, 6.3 series | SRO - 11, series 5 | SRO - 9, series 4 | SRO - 6, series 2.5 | |
0,010 | — | — | — | — | — | — | — | — | 52 |
0,012 | — | — | — | — | — | — | — | — | 65 |
0,016 | — | — | — | — | — | — | 92 | 92 | 116 |
0,020 | — | — | — | — | — | — | 118 | 134 | 182 |
0,025 | — | — | — | 151 | — | 151 | 172 | 201 | 280 |
0,032 | — | — | 197 | 197 | 197 | 233 | 280 | 329 | 459 |
0,040 | — | 249 | 249 | 286 | 297 | 358 | 432 | 511 | 713 |
0,050 | — | 315 | 376 | 443 | 456 | 552 | 669 | 798 | 1100 |
0,063 | 401 | 497 | 582 | 691 | 724 | 885 | 1060 | 1270 | 1750 |
0,075 | 480 | 678 | 831 | 981 | 1020 | 1250 | 1490 | 1790 | 2480 |
0,090 | 643 | 982 | 1190 | 1420 | 1480 | 1800 | 2150 | 2590 | 3580 |
0,110 | 946 | 1440 | 1780 | 2090 | 2190 | 2660 | 3200 | 3840 | 5340 |
0,125 | 1240 | 1870 | 2290 | 2690 | 2810 | 3420 | 4160 | 4960 | 6900 |
0,140 | 1550 | 2350 | 2890 | 3390 | 3520 | 4290 | 5190 | 6240 | — |
0,160 | 2010 | 3080 | 3770 | 4410 | 4600 | 5610 | 6790 | 8130 | — |
0,180 | 2500 | 3850 | 4730 | 5570 | 5830 | 7100 | 8590 | 10300 | — |
0,200 | 3090 | 4770 | 5880 | 6920 | 7180 | 8750 | 10600 | 12700 | — |
0,225 | 3910 | 5980 | 7450 | 8740 | 9120 | 11100 | 13400 | 16100 | — |
0,250 | 4890 | 7430 | 9100 | 10800 | 11200 | 13700 | 16500 | 19800 | — |
0,280 | 6090 | 9290 | 11500 | 13500 | 14000 | 17100 | 20700 | 24900 | — |
0,315 | 7630 | 11800 | 14500 | 17100 | 17800 | 21700 | 26200 | 31500 | — |
0,355 | 9740 | 14900 | 18400 | 21600 | 22600 | 27500 | 33300 | 40000 | — |
0,400 | 12300 | 18900 | 23400 | 27500 | 28600 | 34900 | 42300 | 50700 | — |
0,450 | 15600 | 23900 | 29600 | 34800 | 36300 | 44200 | 53600 | 64200 | — |
0,500 | 19300 | 29500 | 36500 | 42900 | 44800 | 54700 | 66100 | 79200 | — |
0,560 | 24100 | 37100 | 45800 | 53700 | 56100 | 68500 | 82800 | — | — |
0,630 | 30500 | 47000 | 57800 | 68100 | 71200 | 86688 | 104800 | — | — |
0,710 | 38800 | 59700 | 73600 | 86400 | 90300 | 110000 | — | — | — |
0,800 | 49300 | 75600 | 93300 | 109700 | 114500 | 139700 | — | — | — |
0,900 | 62100 | 95700 | 118100 | 138900 | 144700 | — | — | — | — |
1,000 | 76900 | 118100 | 145900 | 171300 | 178900 | — | — | — | — |
1,200 | 110800 | 170100 | 209800 | — | — | — | — | — | — |
When calculating the mass, the density of polyethylene is 950 kg / m3.
Characteristics of gas pipes
GOST for polyethylene products intended for gas, their required technical parameters are established. Some of the indicators are common for both grades of material (80 and 100). So, the installed density should be more than 930 kg / m3, the spread of MFIs is ± 20%, the mass fraction of soot (carbon black) is 2.0-2.5%, and the volatiles are not more than 350 mg / kg.
Indicators that are different for different grades of polyethylene are given in the table (symbol: BRT - rapid crack propagation).
Table 13
Index | The value for the brand of polyethylene, * 10 | unit of measurement | |
100 | 80 | ||
PTR at 190º / 5 kgf | 0,01-0,05 | 0,03-0,12 | g / 10 minutes |
Resistance to MRI at a temperature of 80 degrees for products with a nominal diameter of 160 or 110 mm and SDR 11 | 50 (at an initial voltage of 4600 kPa) | 50 (at an initial voltage of 4 thousand kPa) | no less than |
Pipes for gas from different grades differ in the calculated safety factor, which is given in the table.
Table 14
Maximum working pressure, kPa
|
Safety factor | ||||||
300 | 400 | 600 | 800 | 1000 | 1200 | ||
For PE 80 | SDR 26 | 2,1 | — | — | — | — | — |
SDR 21 | 2,7 | 2,0 | — | — | — | — | |
SDR 17.6 | 3,2 | 2,4 | — | — | — | — | |
SDR 17 | 3,3 | 2,5 | — | — | — | — | |
SDR 13.6 | 4,2 | 3,2 | 2,1 | — | — | — | |
SDR 11 | 5,3 | 4,0 | 2,7 | 2,0 | — | — | |
SDR 9 | 6,7 | 5,0 | 3,3 | 2,5 | 2,0 | — | |
For PE 100 | SDR 26 | 2,7 | 2,0 | — | — | — | — |
SDR 21 | 3,3 | 2,5 | — | — | — | — | |
SDR 17.6 | 4,0 | 3,0 | 2,0 | — | — | — | |
SDR 17 | 4,2 | 3,1 | 2,1 | — | — | — | |
SDR 13.6 | 5,3 | 4,0 | 2,6 | — | — | — | |
SDR 11 | 6,7 | 5,0 | 3,3 | 2,5 | 2,0 | — | |
SDR 9 | 8,3 | 6,2 | 4,2 | 3,1 | 2,5 | 2,1 |
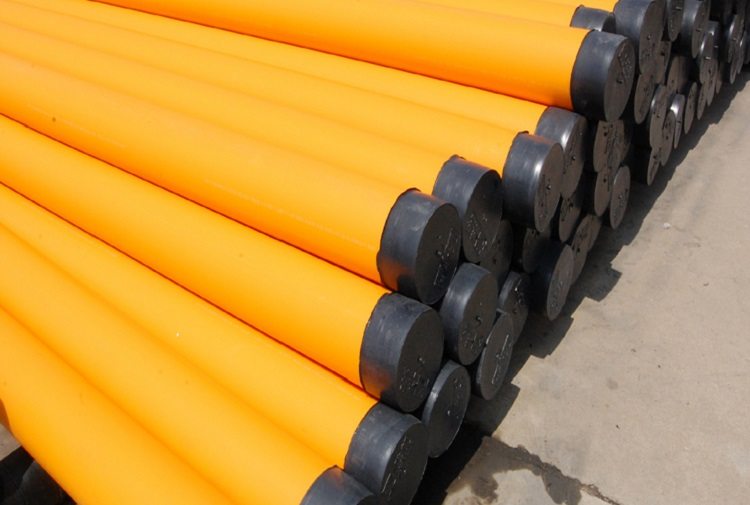
Gas pipes are selected according to the strength parameters, the choice depends on the pressure in the future line
HDPE pipe for cable
GOST 18599 defines the characteristics and technical pipes that can be used for laying and protecting cables.
Note! In the manufacture of such a product, the use of secondary raw materials is allowed (in agreement with the consumer), which reduces the base cost by about 50%.
Pipes for cables made of polyethylene are beneficial not only financially, but also in practical terms. Such communications do not withstand internal pressure, which leads to the limitation of their use:
- for pressureless sewerage;
- like a case for a power cable.
Technical pipes are usually supplied in bays of one hundred or two hundred meters, as well as segments of 12 meters. Different wall thickness determines the assignment of the product to one of the options for stiffness (see table).
Table 15
SDR | 26 | 21 | 17,6 | 13,6 | 11 | 9 |
A type | "SL" | "OS" | "WITH" | "ST" | "T" | "FROM" |
Assortment of technical pipes
Technical pipes have the characteristics presented in the table.
Table 16
Diameter, * 10-1 mm | Type "SL" | Type "OS" | Type "C" | Type "ST" | Type "T" | |||||
Weight g | Wall, * 10-2 mm | Weight g | Wall, * 10-2 mm | Weight g | Wall, * 10-2 mm | Weight g | Wall, * 10-2 mm | Weight g | Wall, * 10-2 mm | |
160 | — | — | — | — | — | — | — | — | 92 | 200 |
200 | — | — | — | — | — | — | — | — | 116 | 200 |
250 | — | — | — | — | — | — | 148 | 200 | 169 | 230 |
320 | — | — | — | — | 197 | 200 | 229 | 240 | 277 | 300 |
400 | — | — | — | — | 281 | 230 | 353 | 300 | 427 | 370 |
500 | — | — | — | — | 436 | 290 | 545 | 370 | 663 | 460 |
630 | — | — | 573 | 300 | 682 | 360 | 869 | 470 | 1050 | 580 |
750 | — | — | 821 | 360 | 970 | 430 | 1230 | 560 | 1460 | 680 |
900 | 969 | 350 | 1180 | 430 | 1400 | 520 | 1760 | 670 | 2120 | 820 |
1100 | 1420 | 420 | 1770 | 530 | 2070 | 630 | 2610 | 810 | 3140 | 1000 |
1250 | 1830 | 480 | 2260 | 600 | 2660 | 710 | 3370 | 920 | 4080 | 1140 |
1400 | 2310 | 540 | 2830 | 670 | 3350 | 800 | 4220 | 1030 | 5080 | 1270 |
1600 | 3030 | 620 | 3710 | 770 | 4350 | 910 | 5500 | 1180 | 6670 | 1460 |
1800 | 3780 | 690 | 4660 | 860 | 5470 | 1020 | 6980 | 1330 | 8430 | 1640 |
2000 | 4680 | 770 | 5770 | 960 | 6780 | 1140 | 8560 | 1470 | 10400 | 1820 |
2250 | 5880 | 860 | 7290 | 1080 | 8550 | 1280 | 10900 | 1660 | 13200 | 2050 |
2500 | 7290 | 960 | 8920 | 1190 | 1060 | 1420 | 13400 | 1840 | 16200 | 2270 |
Advantages of HDPE pipes over steel
Polymer pipes are very common now. The breadth of their use is determined by a number of positive characteristics.
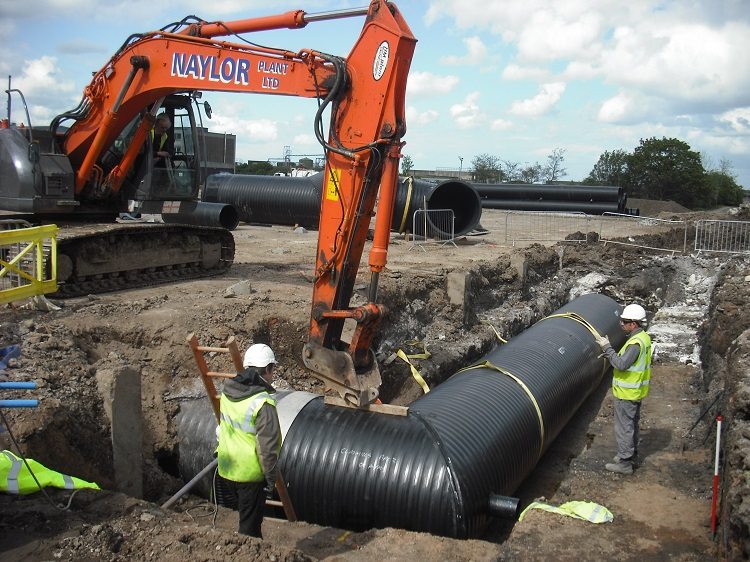
One of the advantages of PE pipes is corrosion resistance, which allows laying underground communications without additional protection
PE products are much cheaper than steel pipes and have a guaranteed operational life of at least fifty years. Since PND pipes (GOST 18599, 22689, 32415 and 50838) do not require the use of cathodic protection, there is no need for their further maintenance.
Such products are not afraid of corrosion, exposure to chemicals. Thanks to their low weight installation work. In addition, the installation is cheaper due to the butt welding of PE pipes. Water frozen inside the pipeline does not destroy it, while maintaining complete tightness and integrity.
HDPE pressure pipes protect well against microorganisms and bacteria. The smooth inner surface provides excellent throughput. When using such pipes, the purity of the transported liquid is guaranteed, which makes it possible to arrange drinking water pipelines based on polyethylene products.
Features of marking HDPE pipes
Information about the characteristics of products, expressed in alphanumeric form, is available on the outer surface of the pipes. The ability to read such markings greatly simplifies the process of choosing the right communication and allows you to avoid critical errors during the assembly of the pipeline.
Labeling of polyethylene products includes the name of the manufacturer, as well as the designation of the standard by which such products are made, for example, GOST 18599.
Note! The name of the pipe material has an international format: PE 100 (or 63, or 80).
After the polymer grade, a group of numbers is indicated that corresponds to the outer diameter. This value is given in millimeters and corresponds to the assortment. In addition to the external dimensions, the marking also includes the internal - wall thickness. It is also expressed in millimeters.
An important characteristic that you should definitely pay attention to when choosing a PND pipe is the nominal pressure. Sometimes manufacturers also indicate the maximum value of this parameter, expressed in MPa.
The final marking position is the batch number and production date.
PE heat resistant
GOST 32415 identifies a special type of polyethylene having increased heat resistance. The assortment is given in the table.
Table 17
Series | 2,5 | 3,2 | 4 | 5 | 6,3 | 8 |
SRO | 6 | 7,4 | 9 | 11 | 13,6 | 17 |
Diameter, * 102 mm | Product wall * 10-2mm | |||||
0,10 | 170 | 140 | 130 | 130 | 130 | 130 |
0,12 | 200 | 180 | 140 | 130 | 130 | 130 |
0,16 | 270 | 220 | 180 | 150 | 130 | 130 |
0,20 | 340 | 280 | 230 | 190 | 150 | 130 |
0,25 | 420 | 350 | 280 | 230 | 190 | 150 |
0,32 | 540 | 440 | 360 | 290 | 240 | 190 |
0,40 | 670 | 550 | 450 | 370 | 300 | 240 |
0,50 | 830 | 690 | 560 | 460 | 370 | 300 |
0,63 | 1050 | 860 | 710 | 580 | 470 | 380 |
0,75 | 1250 | 1030 | 840 | 680 | 560 | 450 |
0,90 | 1500 | 1230 | 1010 | 820 | 670 | 540 |
1,10 | 1830 | 1510 | 1230 | 1000 | 810 | 660 |
1,25 | 2080 | 1710 | 1400 | 1140 | 920 | 740 |
1,40 | 2330 | 1920 | 1570 | 1270 | 1030 | 830 |
1,60 | 2660 | 2190 | 1790 | 1460 | 1180 | 950 |
1,80 | 2990 | 2460 | 2000 | 1640 | 1330 | 1070 |
2,00 | 3320 | 2740 | 2240 | 1820 | 1470 | 1190 |
2,25 | 3740 | 3080 | 2520 | 2050 | 1660 | 1340 |
2,50 | 4150 | 3420 | 2790 | 2270 | 1840 | 1480 |
2,80 | 4650 | 3830 | 3130 | 2540 | 2060 | 1660 |
3,15 | 5230 | 4310 | 3520 | 2860 | 2320 | 1870 |
3,55 | 5900 | 4850 | 3970 | 3220 | 2610 | 2110 |
4,00 | 6650 | 5470 | 4470 | 3630 | 2940 | 2370 |
4,50 | — | 6150 | 5030 | 4090 | 3310 | 2670 |
5,00 | — | 6830 | 5580 | 4540 | 3680 | 2970 |
5,60 | — | — | 6250 | 5080 | 4120 | 3320 |
6,30 | — | — | — | 5720 | 4630 | 3740 |
7,10 | — | — | — | 6450 | — | — |
Such pipes can be produced in straight sections, coils, bays. The deviation of products with a length of up to 12 meters should be 10 mm up (or down). Maximum dimensional deviations and ovality are given in the table.
Table 18
Diameter, * 100 mm | Deviation upwards, mm | Permissible ovality, no more than * 10-1 mm |
0,10 | 0,3 | 11 |
0,12 | 0,3 | 11 |
0,16 | 0,3 | 12 |
0,20 | 0,3 | 12 |
0,25 | 0,3 | 12 |
0,32 | 0,3 | 13 |
0,40 | 0,4 | 14 |
0,50 | 0,5 | 14 |
0,63 | 0,6 | 16 |
0,75 | 0,7 | 16 |
0,90 | 0,9 | 18 |
1,10 | 1,0 | 22 |
1,25 | 1,2 | 25 |
1,40 | 1,3 | 28 |
1,60 | 1,5 | 32 |
1,80 | 1,7 | 36 |
2,00 | 1,8 | 40 |
2,25 | 2,1 | 45 |
2,50 | 2,3 | 50 |
2,80 | 2,5 | 98 |
3,15 | 2,8 | 111 |
3,55 | 3,2 | 125 |
4,00 | 3,6 | 140 |
4,50 | 3,8 | 158 |
5,00 | 4,0 | 175 |
5,60 | 4,3 | 196 |
6,30 | 4,6 | 221 |
7,10 | 4,9 | — |
Crosslinked Polyethylene Properties
Regulatory documents (for example, GOST 32415) govern the technical characteristics and conditions of use of another type of polymer material - cross-linked polyethylene.
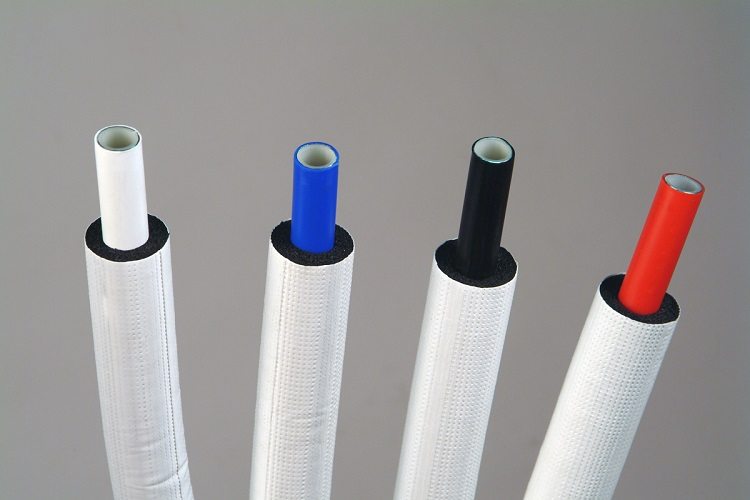
Cross-linked polyethylene is particularly durable, so pipes from it are used even when installing heating systems
Conventional HDPE polyethylene is obtained in the presence of catalysts under low pressure. Its structure includes molecules with a significant number of branches, most of which are in space in a free state.
Note! After stitching, side bonds are additionally formed, forming an intermolecular network, which is distinguished by its special strength.
Various crosslinking technologies lead to an increase or decrease in the number of such bonds, which affects the characteristics of the product. For example, PEX-a polymer is obtained by a more expensive method, but it has the highest crack resistance, impact resistance and the highest melting point.
Crosslinked Polyethylene Parameters
Standards define all the technical parameters of the material. So, its density is 940 kg / m3, the melting point is +200 degrees, the thermal conductivity is 0.38 W / m * K. Crosslinked polyethylene has tensile strengths of 350 to 800% and a very high level of flexibility. Pipes made of such a polymer are characterized by increased throughput, which is 20-30 percent higher than the same indicator for other communications. Tubular joints are also characterized by increased strength.
The negative properties of the material include instability to ultraviolet radiation, which, after prolonged exposure, leads to its fragility and slow destruction, as well as the destructive effect of oxygen (O2) upon penetration into the molecular structure of a substance.
PND pipe (GOST 32415, 22689, 18599 and 50838) is a high-quality product with a number of positive qualities. The technical characteristics established by the standards allow them to be applied in many fields and for various pipelines.