The spiral reinforced rubber hose is a flexible conduit. Its construction of several rubber tubes is strengthened by winding or winding synthetic threads or special textiles, or metal wire. A flexible and durable sleeve is used to transport various working fluids, both liquids of different consistencies and gaseous under high pressure.
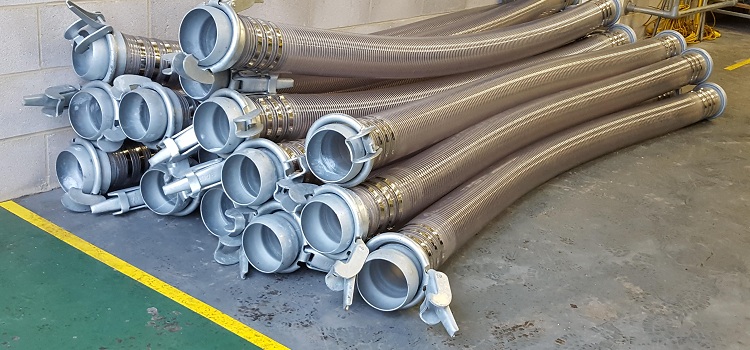
Reinforced hoses of various types are used for transporting liquids and gases both under pressure and without it.
Content
Reinforced Rubber Hose Design
Reinforced rubber hose consists of the following elements:
- inner rubber layer providing sealing;
- power frame - braids made of metal wire, textile or synthetics;
- outer rubber layer.
To perform the inner and outer layers, the extrusion (extrusion) method is used. The sleeve is made using fluoroplastic, polyethylene film and polyamide. By combining these polymeric materials and combining them with various special additives, they achieve increased product durability:
- to temperature effects;
- to mechanical and physical stress;
- to aggressive working environments.
The winding or winding that makes the sleeve stiff enough is done on special equipment. The combination of the inner and outer layers of rubber with a braid, which can be performed in one or several layers, allows the structure, while maintaining sufficient flexibility, to be very durable and withstand high pressure of the working environment.
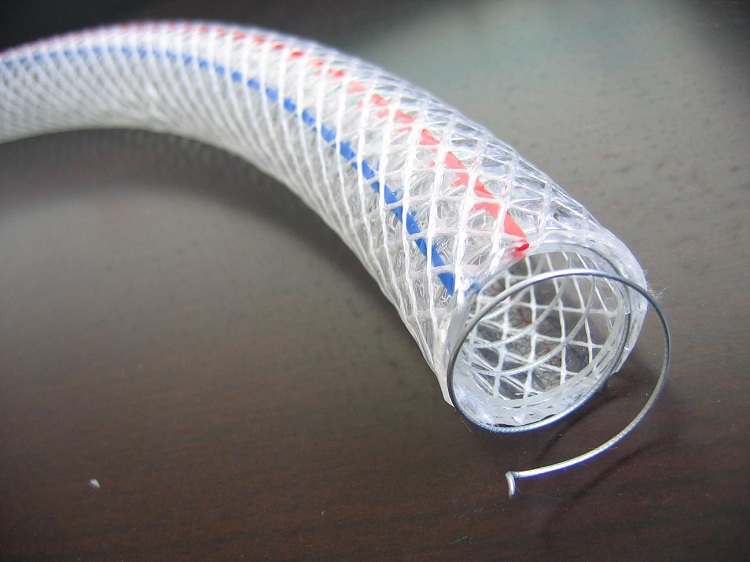
Reinforced hose is a multilayer construction, inside of which there is a metal wire that gives strength
Note! The sleeve, the ends of which are equipped with fittings, is sealed at the junction with them with special sleeves and cuffs.
The sleeve, depending on its purpose, is equipped with a tip with a profile view suitable for certain equipment.
Classification of high pressure armored hoses
The rubber hose reinforced with a spiral can be braided or wound. Braided high-pressure hoses are intended for transportation of technical fluids, water-based emulsions and mineral oils, the temperature of which is in the range from -42º C to 75º C (for emulsions and oils) and 101º C (for liquids). Three types of sleeves withstand different tensile forces:
- A - from 14.7 kgf
- B - from 17.5.
- In (Z) - more than 20 kgf. They are characterized by increased strength, brass wire is used for the manufacture.
Three types are also distinguished by the magnitude of the working pressure:
- I - braid in one layer withstands up to 160 atm.
- II - two-layer - up to 200 atm.
- III - three-layer - up to 330 atm.
According to international marking:
- SN - the outer layer is formed by fine structure rubber;
- ST- braided used brass wire.
A sleeve with a braid of a winding type can be designed for different pressure of the working fluid:
- 4 SP - four layers of steel wire - for medium pressure.
- 4 RS - four layers of an especially strong spiral - for high.
- R 12 - will withstand prolonged use in conditions of elevated temperature and medium pressure.
- R 13 and R 15 - winding in six layers - for elevated temperatures and pressure.
Parameters and marking of reinforced hoses
For high pressure hoses with one or two braid layers, the operating pressure can be up to 250 bar. According to the DIN standard, they are classified as EN853. With a braid thickness of four or six layers, the working pressure can reach up to 455 bar. The DIN standard for them is the designation EN856.
The optimum temperature range of the technical fluid for the WFD is considered to be a range from -40º C to + 100º C. Moreover, the products have a significant margin of safety, maintaining and lowering the minimum temperature by another 15 degrees, and increasing the maximum to + 155º C.
Note! The permissible bending radius is measured along the inner arc. The flattening of the hose in this case, measured using a special sliding calibrator, will be no more than a tenth of the initial value of the outer diameter.
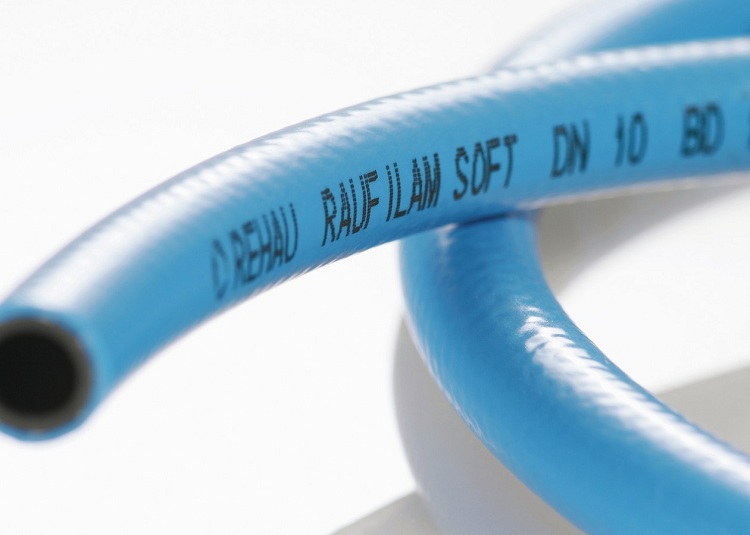
By marking on the outer coating of the product it is easy to determine its purpose and technical parameters
Marking of high pressure hoses contains data on key parameters:
- bending radius;
- inner diameter;
- sizes of connecting thread;
- key sizes;
- working fluid pressure.
The extended technical designation contains more than ten parameters. Embossing is applied to the outer surface of the hose. It may include a designation that determines the climatic conditions of use:
- Y - moderate;
- HL - cold;
- T - the tropics.
Reinforced Hose Application
Reinforced hoses, durable and flexible, stably resisting high pressure and aggressive environments, temperature drops are used in different fields of activity:
- ventilation systems;
- water supply and sewerage;
- woodworking;
- transportation of petroleum products;
- mechanical engineering;
- agriculture (for liquids and pneumatic conveying);
- Food Industry;
- transportation of waste, sludge and chemical products.
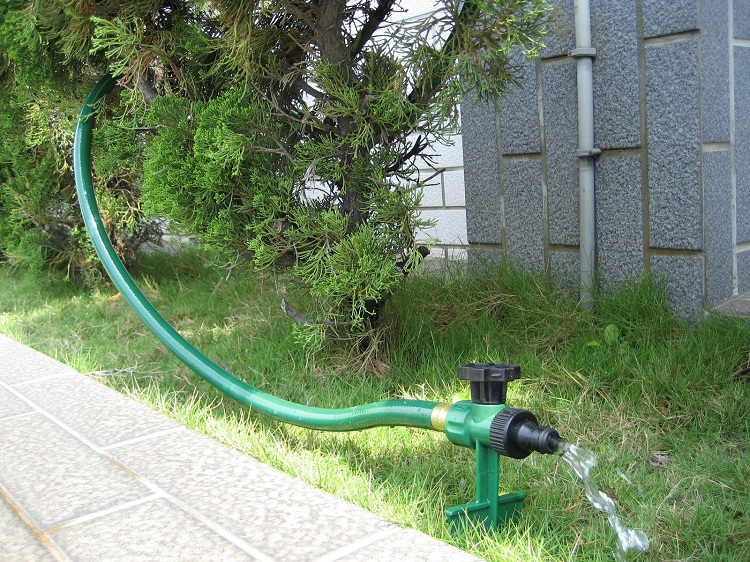
Such hoses can be found in various fields of construction, industry and economy, in everyday life they are most often used for watering
Almost every complex technical device or unit can not do without these useful devices. They are unpretentious, inexpensive and reliable.
Features of the operation of high pressure hoses
Sleeves are created with a considerable margin of safety, but cases of their failure occur. As a rule, hose breakdowns occur due to neglect of the operating rules or incorrect product selection. Of particular importance is the compatibility of all equipment elements with the working environment, and not just the inner layer directly in contact with it. Damage caused by the aggressive nature of the medium occurs, as a rule, at the end connections.
On a note! The sleeve should work at the optimum temperature recommended by the manufacturer. Otherwise, the fittings fail prematurely and the condition of the elastomer deteriorates.
The correct selection of the inner diameter of the hoses is important. When installing a sleeve with a diameter less than the recommended value, the phenomenon of turbulence occurs. As a result, the internal operating pressure and temperature rise sharply, which reduces the life of the equipment.
Hydraulic hoses cannot be selected exactly in length because of:
- its decrease with increasing pressure;
- vibration during operation;
- allowed twisting and sagging during installation.
Therefore, it is recommended not to allow strain on the hoses, given the permissible bending radius. The condition of the outer layer of the sleeves, subject to wear, also requires attention.
The correct selection of hoses and observance of operating conditions will allow using the equipment for a long time without significant damage.