The popularity of metal-plastic pipes with the advent of polypropylene analogues has somewhat decreased. However, today they occupy a voluminous niche in the plumbing market. For example, when installing underfloor heating, there is no worthy replacement for metal-plastic pipe products. These products got strength from metal, and flexibility from plastic. The correct approach to joining metal-plastic elements will save a considerable amount during the installation of the pipeline.
Content
Design and characteristics of plastic pipes
The internal and external parts of these products are made of plastic, so that the design is highly resistant to negative factors. Between these parts is a reinforcing layer, which is an aluminum foil. Glue is applied on both sides. He securely fixes it between the plastic layers. On the one hand, such a device provides flexibility of the product, but multiple bends in one place are not allowed.
The reinforcing layer is overlapped using ultrasound or end-to-end with a laser. Non-uniform geometric parameters are inherent in pipe products with a joint according to the first embodiment, and for this reason it plays in strength. Butt-welded products using laser technology are called seamless. They have a uniform thickness over the entire length, more reliable, but also cost more.
The aluminum layer practically does not have any effect on the main operational parameters of the pipeline. Her tasks are as follows:
- providing partial compensation for polymer expansion upon heating;
- creating a diffusion barrier that prevents oxygen from entering the pipe.
Since the fluid is transported along the plastic layer, it is therefore it that forms the operational properties of metal-plastic pipe products.
Good to know! Both layers - internal and external - are made of cross-linked polyethylene. Moreover, for a metal-plastic water supply, an expensive type of this polymer is used - food-grade polyethylene, and for a sewage pipeline it is cheaper.
Water systems can cause water hammer. Pipe products marked with such sequences of characters: PEX and PE-RT do an excellent job of them. But for the arrangement of water supply branches, in which the likelihood of water hammer is high, it is better to refuse metal-plastic pipes marked PE-RS, PE-HD and HDPE - they work at low pressure.
Of the advantages of these products, it is worth highlighting:
- ease of installation;
- high chemical resistance;
- environmentally friendly materials are used for manufacturing;
- flexibility provides the ability to bypass bumps and corners, which in some cases reduces the relevance of connecting plastic pipes with fittings in a limited space. They can simply be bent;
- scale does not form on the inner surface;
- not subject to corrosion;
- long service life - up to 50 years.
But it was not without flaws. The main ones are:
- exposure to ultraviolet radiation causes “aging” of metal-plastic pipe products;
- such products are subject to burning.
How to connect metal-plastic pipes
To connect these elements of the water supply branch, special press fittings, compression parts and sliding press fittings are used. Consider the methodology for their installation in more detail.
Compression parts. In this case, we are talking about the use of crimp brass fittings. To connect the elements of the water supply branch with their help, it is enough to have a wrench. The part design includes a union nut, a fitting and a split ring. Crimp fittings can be disassembled and reused.
Even a person with only basic plumbing skills can cope with the task of joining metal-plastic pipes using this technology. The sequence of events is as follows:
- First, a pipe of the required length is prepared. The basic requirement is as follows: the section of the workpiece at a distance of 10 cm from and to the point of cut must be even;
- then the workpiece for marking is trimmed with precision scissors. In this case, the cut plane should be strictly perpendicular to its longitudinal axis;
- after checking the integrity of all parts and gaskets, a nut is put on the pipe, and then a fitting ring;
- the edge of the workpiece is processed by a reamer. The inner facet of 1 millimeter is removed by the calibration side. The other side is the chamfer;
- the pipe is pushed onto the fitting until it stops;
- the union nut is screwed onto the fitting first by hand, and then using a wrench. Ultimately, 1-1.5 turns of thread should be visible.
Advice! Tighten the nut very carefully. Excessive force may cause the ring to crack.
It is this factor that determines the presence of one feature in such a collet connection of metal-plastic pipes. It consists in the need for periodic tightening of the union nut.
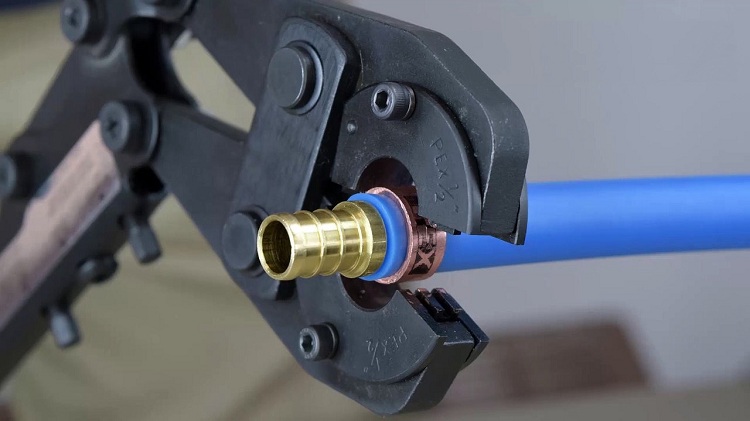
If there is a need for hidden pipe laying, then for their installation it is worth using press fittings
Special press fittings. These connecting elements are used when laying hidden communications and when installing underfloor heating. Work is carried out using a tool called press pliers. Installation in this case is more reliable than using compression fittings. The connection is performed in the following order:
- the pipe is cut off. The edge is calibrated by chamfering, both external and internal. Pipe diameter control is performed using a calibrator;
- the fitting is checked for o-rings and dielectric gaskets;
- a crimp sleeve is put on its edge;
- O-rings are put on the fitting, after which the fitting is inserted into the pipe;
- in the process of crimping the coupling with the help of press tongs, it is necessary to control the penetration of the sleeve collar into the recess on the press nozzle. This tool is equipped with inserts suitable for working with pipe products of different diameters. Repeatedly squeezing the coupling is undesirable, it is necessary to act so that a positive result is obtained the first time.
There are press fittings on sale, the coupling on which is already fixed. This technical solution allows you to immediately push the part onto the pipe. The landing depth is controlled through the hole in the coupling.
Sliding fittings. Such a connector for water-filled metal-plastic pipes is fixed not only by means of press tongs. In this case, it is also intended to use an expander to expand the pipe diameter to a size that allows reliable fitting fastening. The result is a one-piece connection. Use it when arranging a hidden pipeline.
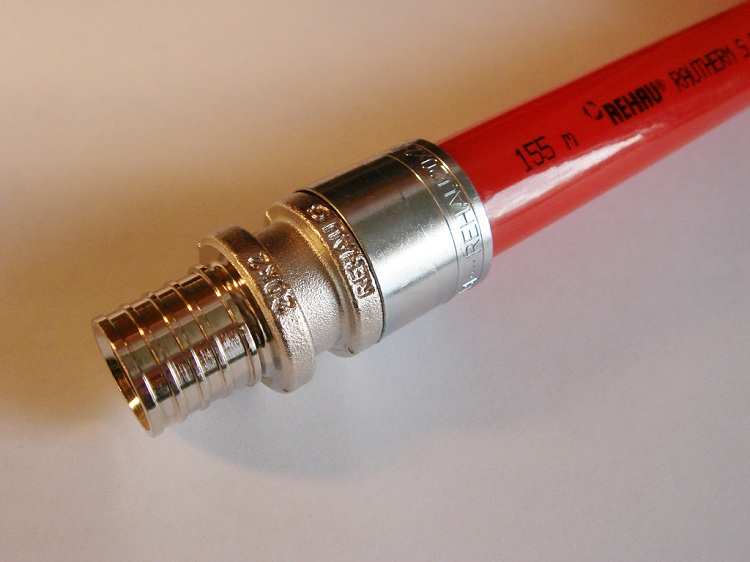
Sliding fitting provides one-piece connection, and can also be used with hidden wiring communications
The answer to the question of how a metal-plastic pipe is connected to a fitting of this type begins with a standard phrase: first, we prepare a segment of the required length. Then we put a sleeve on it, after which we extend the edge of the pipe with an expander. Then the fitting is put on, the coupling is clamped by the press, and the fitting on the fitting is tightened. Such actions will ensure a reliable and tight connection.
How to connect a plastic pipe with a metal pipe
The need for this operation arises when, for example, only part of the water supply system changes or if a metal-plastic branch is removed from the metal riser. It is important that you follow the step by step instructions. The most common option is to use a crimp fitting.
Perform the work in the following order:
- if the pipe is old, clean it of rust, and screw the fitting onto it using an open-end wrench.
Advice! To prevent leaks, a proven method is suitable: soak the tow with paint and wrap the resulting sealant in a thin layer on the pipe thread, then screw on the connecting part.
- while the paint dries, work with a metal-plastic pipe product: pass it through the nut and press washer, and calibrate the pipe itself;
- then screw the cone to the metal pipe and put on it a metal-plastic pipe product;
- using a open-end wrench, tighten the nut, ensuring that the washer tightly compresses the metal-plastic pipe element.
Connection of plastic pipes with radiators
To perform this procedure, several schemes have been developed using fittings and special adapters.
- When the pipeline is laid in the floor using a hidden wiring method, the bottom-up scheme is used. The presence of valves and temperature regulators provides for the mandatory use of special adapters designed to firmly fix all the necessary connections.
- For lateral connection, adapters are also used and, in addition, tees are brass or chrome with metric threads.
- Connection to the exit from the floor. Complicating the implementation of this scheme is the "breakdown" of the front pipes. This phenomenon effectively compensates for the telescopic fitting.
- Diagonal pattern or corner joint. This method is not the only one existing, the implementation of which requires the use of rotary elbows.
Installation of metal-plastic pipes. Tips from professionals
One of the great advantages of this pipe product is the ability to create shaped elements from it, change the direction of the pipe to any desired angle, not to mention the fact that it can even be rolled up under certain conditions into a ring. When installing a metal-plastic pipeline, professionals recommend using a collector. This approach will ensure a uniform pressure of the water flow to all connected consumers. It is also worth listening to one more advice of plumbers, who have a long work experience. It sounds like this: to minimize the number of connections and, accordingly, to increase the reliability of the system, it is better to use the pipe from the collector to the end user with “one thread”.
To bend metal-plastic pipe products follows using a pipe bender or hand conductor, which is a spring.It can be worn on top or embedded in a pipe.
Advice! It is better to use an internal conductor in the manufacture of medium-sized shaped elements. Then this accessory will not slip due to the fact that the contractor controls the bending voltage of the pipe and, accordingly, the conductor with his own hands.
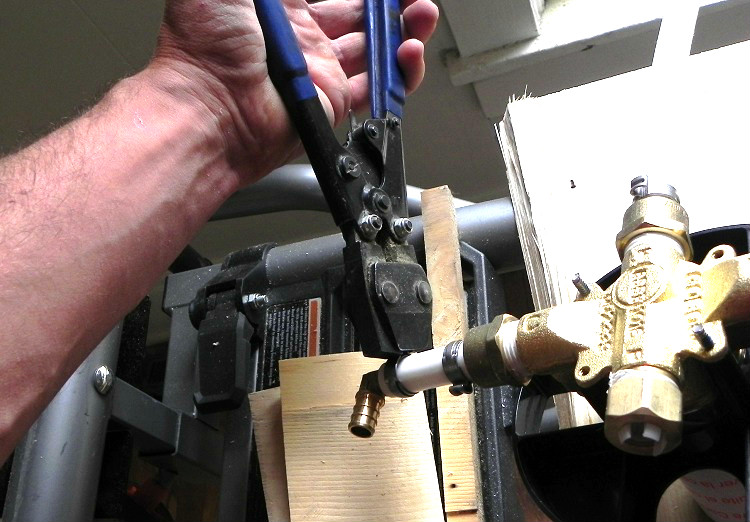
Installation of structures made of metal-plastic pipes must be carried out in accordance with all the rules, otherwise the system will be unreliable
One cannot do without an external conductor if it is necessary to create turns or several turns of the pipeline (for example, when a warm floor is laid). If you do not have the skills to work with metal-plastic pipes, it is not recommended to bend these products only with your own hands without a tool.
Note! In the best case, you will narrow the cross section of the water supply branch, and in the worst case, simply break the pipe at the bend.
Returning to the conversation about joining metal-plastic pipes with fittings, it should be noted that pipelines laid in the floor or in the wall are equipped with one-piece, unattended parts. Those of them that go openly may be equipped with any convenient connection. The use of compression fittings is advisable when connecting, for example, taps and other plumbing fixtures. This will ensure their quick repair or replacement.
For fastening pipelines to the wall, fixed and movable supports are used. They are made of plastic of any kind, for example, polyvinyl chloride. Having decided to use metallic similar accessories, equip them with an elastic gasket. Supports should not cause deformation of the pipe or its outer layer. When laying the water supply branch in an open way, use split supports.
How to disassemble the fitting of plastic pipes
It should be noted right away that not all types of joints of this type can be replaced with new connectors without damage. It all depends on the technology used for joining metal-plastic pipe products, for example, what fittings were used in this procedure for specific sections of the pipeline.
If docking was carried out using press fittings or fittings with sliding sleeves, pressed by means of press pliers, such connections are classified as non-separable. Therefore, if necessary, their replacement is carried out by complete dismantling followed by cutting off this section of the pipeline. Then you need a new set of fittings and in addition an additional piece of pipe.
If a compression type connector was used for plastic pipes, you only need to unscrew the clamping nuts, which is quite simple. And therefore, it will not be difficult to disassemble the entire site with a problematic connection.
The choice of fittings for such pipe products must be approached with care. It is better to give preference to products of well-known companies. After all, the most common cause of all accidents and leaks is poor-quality connecting elements of metal-plastic pipelines.