Electric-welded coupling - a type of polymer fitting (as usual, polyethylene, less commonly polypropylene, fluoroplastic), equipped with a built-in electric heater. It is used to connect sections of pipelines made of low pressure materials using a special electrofusion welding machine operating in automatic mode.
Content
- 1 Design and principle of operation of the electrofusion coupling
- 2 Fabrication of an electrically welded coupling
- 3 Where are electric welded couplings used?
- 4 Advantages of Electrofusion Couplings
- 5 Disadvantages of electrofusion coupling
- 6 Apparatus for welding. Welding procedure
- 7 How to be guided when choosing an electrically welded coupling
Design and principle of operation of the electrofusion coupling
An electric-welded coupling combines the advantages of a fitting (representing a variety of it) and welding equipment in its device. It consists of the following elements:
- a casing;
- heating threads. They can be copper or carbon. The latter are more expensive, but warm up faster;
- conductive parts for terminals;
- an indicator indicating the stage of the welding process of the product;
- fasteners with which the clutch set the working position.
The principle of operation of the connection is simple. It is made of a low-pressure polymeric material, most often of polyethylene, with built-in electric heating elements - conductors with high resistance. The electrodes of a special welding machine are connected to two terminals on the outside of the connection. When specified values of electric current flow through the conductor, electrical energy is converted into heat. The polymer material of the connected parts, heated to the melting temperature, is mixed into a homogeneous mass. When cooling, a finished structure is obtained, characterized by the same properties as the pipes.
Fabrication of an electrically welded coupling
An electrofusion coupler is manufactured using a method such as injection molding under high pressure. The production process takes very little time, but requires preliminary preparation of molds in order to mold couplings of a certain configuration and size. The dispensing module is filled with the required amount of molten polymer. A nozzle injects molten mass into a prepared mold under pressure. The cooled polymer mass takes the given dimensions and configuration, turns into a finished connection for pipelines.
A coupling made in this way is placed in a plastic bag, supplemented by a bar code. It can be enclosed in a package in the form of a separate card or sticker fixed directly to the coupling. The bar code captures important information about the welding parameters for a special electrofusion welding apparatus, which sets the program for its operation.
It's important to know! To start the device, you need a scanner or a reading pencil.
Where are electric welded couplings used?
The ease of manufacture and installation of electrowelded couplings, combined with the low cost and sufficient reliability of the design of polymeric materials, led to their widespread use.
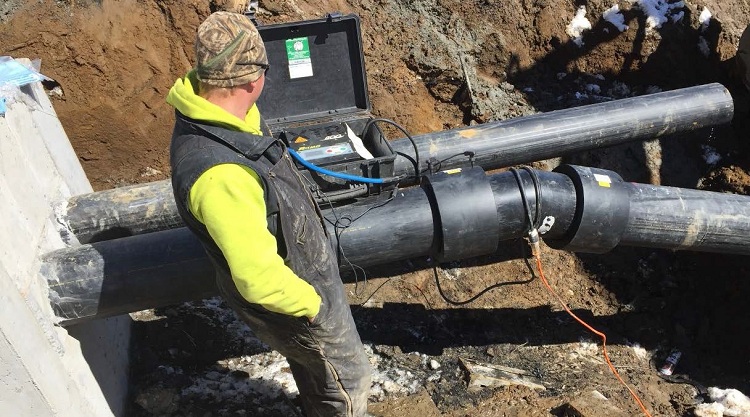
By electrofusion couplings it is possible to mount gas pipelines and water supply lines in which the use of PE pipes is allowed
When installing electrowelded couplings, it should be remembered that there are strict restrictions on their use:
- the temperature of the working environment should not exceed 40º C;
- pressure - no more than 16 atm.
It is permissible to use electrowelded couplings:
- in the sewer system;
- in the water supply system (pressure and non-pressure), for supplying both drinking and industrial water;
- in the gas supply system;
- in pipelines that transport chemicals that do not react with polyethylene (contact with acids and alkalis should be excluded categorically).
Helpful information! The spread of electrowelded joints is also associated with the fact that they, like pipes made of low pressure polymers, can withstand freezing and thawing of the fluid pumped through them.
Advantages of Electrofusion Couplings
The distribution of fittings of this type is associated with their inherent significant advantages, which include:
- longevity (they can last more than fifty years);
- relatively low cost (when compared with compounds made from other materials);
- corrosion resistance;
- the ability not to lose resistance to water shocks and extensions over time;
- variety of configurations and sizes;
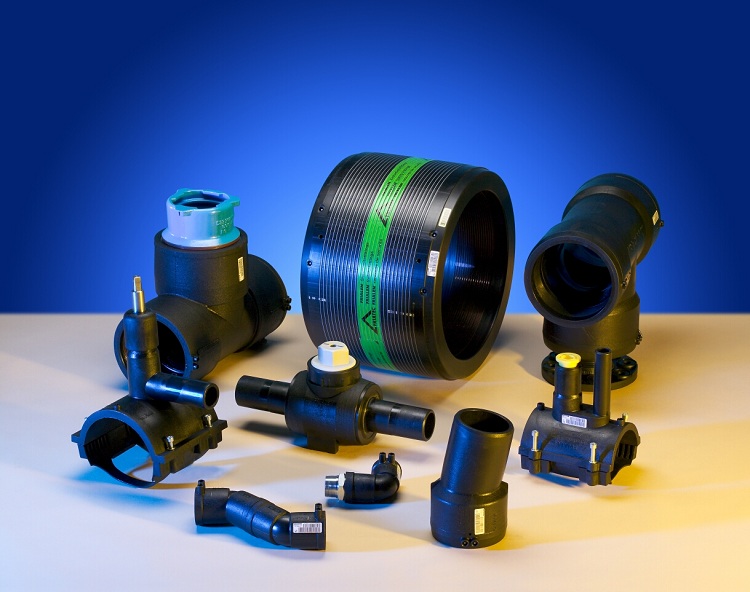
Such fittings are available in various sizes and configurations, which leads to their widest application.
- the possibility of using when connecting pipes of both different diameters, and made of different materials (especially when connecting metal pipes with polyethylene);
- ease of installation that does not require professional skills;
- incredible speed of installation;
- inaccessible to similar joints made of other materials, the ability to install in the most difficult places of the pipeline route. They are absolutely indispensable when connection is required on a bend, branching, reinforcement connections.
Disadvantages of electrofusion coupling
Speaking about the disadvantages of electrically welded couplings, we are talking more about the features of their application, limitations. Welded joints cannot be operated if:
- the temperature regime is beyond the working range from 0º to 40º C. That is, their installation in hot water supply systems should be excluded so as to prevent leaks;
- there is contact with an alkaline or strongly acidic environment;
- working pressure exceeds recommended for this type of coupling (more than 16 atm).
The disadvantages of the electric-welded coupling include its considerable cost. But the costs of acquiring such a compound are compensated by the longevity of its operation, the insignificance of the costs of the work of a specialist invited for installation (or their complete absence, if installed independently).
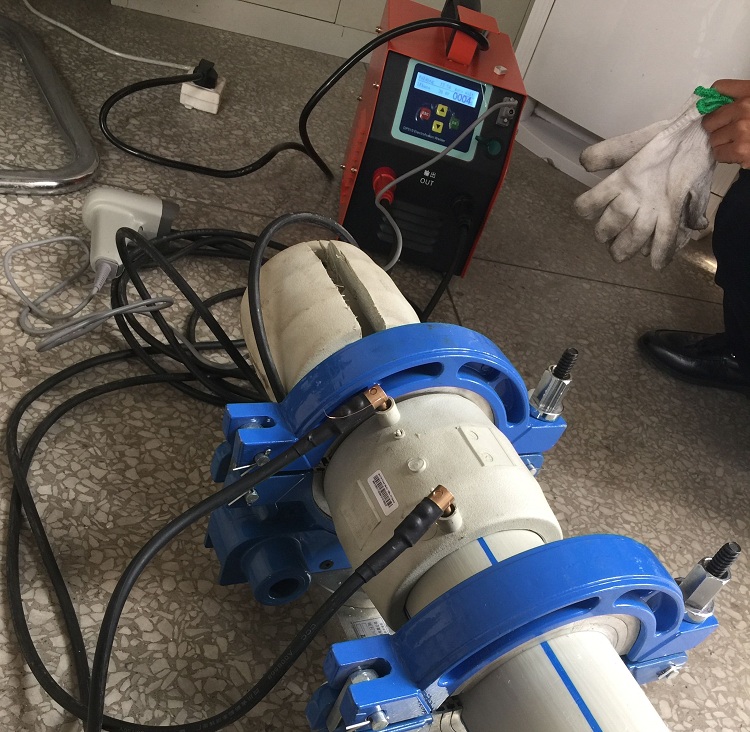
Couplings are mounted only using a special welding machine; there is no other method for connecting these fittings to pipes
Apparatus for welding. Welding procedure
Installation of an electric welding coupling requires special equipment - an apparatus for welding electric-welded couplings PND. The device is used right at the place where the work is directly carried out. It weighs less than 20 kg, and does not require a highly qualified specialist for service. The welding equipment through the scanner or reading pencil receives the required information to start the program of work. The process control is programmed, the intervention of the welder is unnecessary. The work is carried out in the following order:
- The mounted pipe, which does not have significant curvature, is cut strictly perpendicular to its axis. The ends of the connected pipes are cleaned using a scraper for the entire length of the connection. Then they are thoroughly degreased by soaking in a rag or napkin in acetone or isopropyl alcohol.
- Parts intended for welding are carefully fixed in the positioner.At the same time, attention is drawn to the technological beams that are available in the center of the inner part of the coupling, specially installed so that the ends of the pipes connected by welding rest against them. It is not permissible for the gap between the pipes to be connected inside the coupling to exceed their wall thickness.
- The terminals of the welding machine (transformer-rectifier) are connected to the contacts of the coupling. By reading the information from the barcode on it, an automatic welding process begins.
- At the end of welding, when the connection cools down, its tightness is checked. To do this, soap solution is applied to the junction, and compressed air is supplied to the pipeline system.
How to be guided when choosing an electrically welded coupling
The electrowelded coupling is selected based on which pipes will need to be connected with it. As usual, these are polyethylene pipes, which are marked using alphabetic characters and numeric values.
Good to know! The designation PE refers, of course, to polyethylene, and numerical values indicate its brand.
The designation SDR marks such a parameter as the ratio of the outer diameter to the pipe wall thickness. A larger SDR value means a smaller pipe wall thickness, and vice versa - the thicker the pipe wall, the lower the numerical SDR value.
Pipes made of low-pressure polyethylene are durable products designed for a very long service life. (And polypropylene and fluoroplastic pipes are even more reliable and durable). However, they also have to be changed, often well before the end of their life. This is due to the connection of new household and plumbing devices, changes in the configuration of the pipeline system. In such cases, it is worth installing a coupling with an electric heating element. Dutch, Italian, German manufacturers do not use secondary raw materials in the manufacture of electric-welded couplings. This affects the quality of products for the better.
When purchasing electrowelded couplings, it is worthwhile to familiarize themselves with their technical characteristics presented in special tables. Having correctly selected the coupling and without violating the simple rules for its installation, you can count on many years of perfect operation of the product.