PND coupling is a type of fitting product that has become widespread with the advent of communications made of polyethylene. The combination of low cost, corrosion resistance, tight joints with an incredible duration of operation led to the fact that the PND coupling is successfully used in various sectors of the economy in the construction of communications for water and gas supply, sewage and heating.
Content
PND couplings classification
Depending on the purpose, the couplings made by extrusion from low pressure polyethylene perform:
- Protective. Such products protect structures from the possibility of damage.
- Connecting. Also referred to as repair due to the use in the elimination of gusts of pipeline networks. Valued for special reliability, ensuring tightness and durability of joints.
According to the design features and purpose of the coupling, there are:
- compensatory. With their help, a variety of devices are connected to the pipeline or a transition to a smaller section is carried out. In the latter case, a transition coupling is used;
- equal bores. Such fittings linearly connect pipes of the same diameter;
- flanged. The use of such a connecting element is resorted to, if necessary, to join pipes made of different materials and / or having different diameters;
- plugs. They are used to temporarily block the pipeline section;
- crosses and tees. Allow to create branches from the main network of the pipeline or to insert into it;
- bends. The use of bends with angles of 45, 66 and 90º allows you to change the direction of the pipe line.
Docking of polyethylene pipes is carried out using the following types of couplings:
- connecting;
- compression (crimp);
- flanged;
- electrowelded (reduction).
Benefits of Using Couplings
Couplings are the simplest in design and are only suitable for connecting pipes with the same internal cross-section. This is the most massive of all varieties of HDPE fittings, which is explained, first of all, by the incredible simplicity and almost instantaneous installation. To install the coupling, two simple operations are required:
- Insert the polyethylene pipe into a special sleeve made of plastic and fix it.
- Scrolling the nut (cover) clockwise, press it in.
In addition to the low cost and the pace of installation of connecting PND couplings, other advantages are inherent:
- ensuring high reliability of fastening;
- insignificant sensitivity to changes in temperature in the widest range. They remain operational at twenty-degree frosts and a temperature increase of up to + 50º С;
- resistance to mechanical influences;
- inertness to aggressive environments;
- breadth of spectrum of application;
- durability. Warranties are issued for half a century of operation, and a simple polyethylene construction can last three centuries.
The device and installation of compression (crimp) couplings
Compression fitting is not much more complicated than connecting. The design consists of:
- UV resistant polypropylene casing;
- the same press-in sleeve and nut cover;
- sealant (nitrile rubber is used for manufacturing);
- collets (seam ring) (for production take acetal resin).
- Compression couplings are used on PND pipelines for transportation of various liquids under pressure reaching 16 bar.
Step-by-step assembly of the connection using the compression sleeve is as follows:
- In a pipe cut strictly at right angles, the burrs are simultaneously eliminated and the edges rounded. The surface of the pipe to be inserted into the fitting is cleaned of contaminants.
- The blue nut is removed from the sleeve and put on the end of the pipe. The white clamping ring is installed so that the thickened part is directed to the pipe tail.
- Having inserted the pipe all the way into the coupling body, the clamping ring is moved in the same way. It is recommended that this operation be preceded by preliminary drawing on the pipe using a marker marker showing the extreme point of entry.
Tightening the blue nut begins manually, and ends using a special tool or tool.
Important! Tighten the nut with caution not to spoil the connection by hauling.
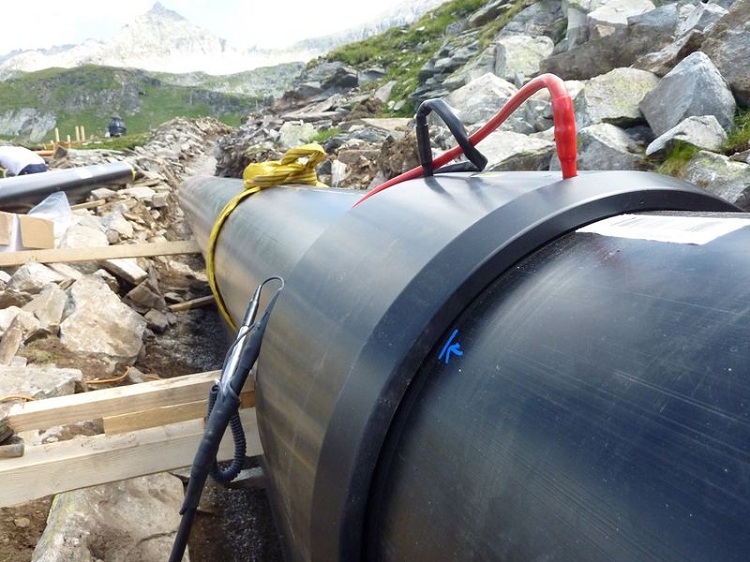
Electric-welded couplings are connected with special cables to the welding machine and are used for mounting pipes of various diameters
The design of electric-welded PND couplings, its advantages and disadvantages
Electric-welded (reduction) PND fitting is a sleeve with built-in electric heating elements. The design is composed of the following elements:
- body;
- providing excellent heat dissipation by a heating spiral, the manufacture of which requires a special alloy. Three types of heating elements with different levels of safety are used: open (unsafe and therefore rare); half open. They are used massively and to a sufficient degree ensure uniform heating of the surface; hidden.
- two terminals for connecting a special device for welding (rectifier transformer). The course of the welding process in automatic mode with the exception of the human factor, when the information necessary for work is read from the bar code, significantly reduces the already almost zero chance of marriage.
The advantages of reducing PND couplings are usually:
- ease of use;
- high installation rates;
- universality of application;
- amazing reliability and the incredible duration of operation resulting from it;
- the ability to install when connecting pipes made of various materials and differing in diameter;
- the absence of installation problems in almost any environment, even with extreme space tightness.
The disadvantages of electrically welded PND compounds are the restrictions on the use of products arising from the characteristics of the material used for the manufacture of:
- limitation of the temperature of the working environment by the upper forty-degree limit excludes the use in heating and hot water supply systems;
- it is unacceptable to use in pipelines with a working medium under high pressure;
- lack of inertness common to many polymers with respect to the effects of acidic and alkaline media.
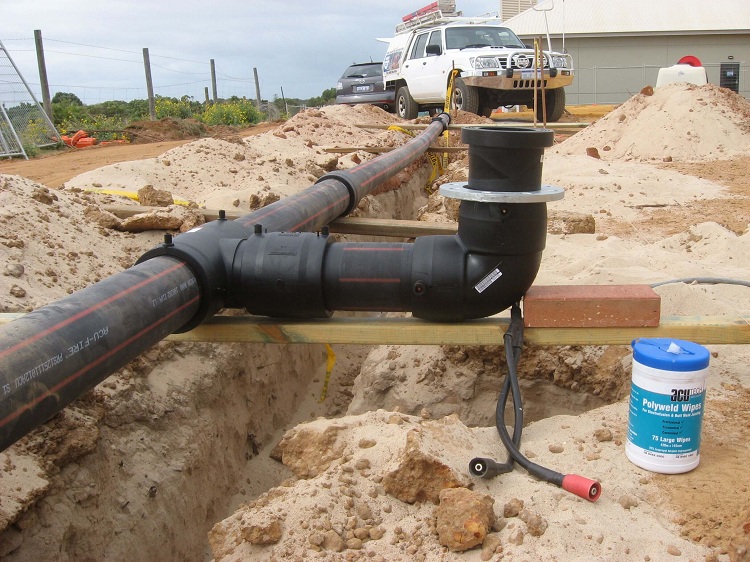
Connection by electrowelded couplings is suitable for different types of pipelines, but working under low pressure
How is welding using reducing PND couplings
The passage of welding in automatic mode does not exclude the need for thorough preparation and care during the process.
Note! As with other types of couplings, you have to start with the preparation of the pipe, which is cut so that the axis of the pipe and the cut plane form a perpendicular.
Correctly cut pipe is deburred for the entire length of the intended entry into the coupling, the bevel is removed using a special scraper and carefully degreased. For free entry of the pipe into the fitting, its diameter decreases due to the use of clamps. The last step in the preparation of welding is fixing the elements to be connected in a special mount.
Actually, the welding process proceeds as follows:
- The terminals of the reduction coupling are connected to the contacts of the welding device (rectifier transformer).
- By reading the information contained in the bar code, electricity is supplied. Warming up takes some time. Exposure to high temperature and pressure provides melting of the plastic fitting and pipe. The melt becomes a homogeneous mass.
- After stopping heating, the junction is allowed to cool, which takes about twenty minutes. After sustaining the time for cooling, they achieve the fact that the strength at the pipe walls at the junction is higher than in other areas. After that, the process is repeated, since it is necessary to connect another segment of the pipe to the output of the coupling.
- A leak test is carried out by washing the joints and supplying air under pressure (at least through a vacuum cleaner hose). The appearance of bubbles means a leak in the joint, but this happens extremely rarely.
- When working with large diameter pipes, the pipes are preheated at the junction. Then, at the joint, the sides of the product are sequentially welded, first on one half of the fitting, then on the other.
A variety of couplings for connection HDPE pipes allows you to use them on communications of various types. Regardless of the type, all the PND products are characterized by excellent performance, low cost, ease of installation and long-term service. The choice of a specific type of connection is determined by the specifics of the pipeline and the joined structural elements, and the place of installation.