When replacing or upgrading a system of polyethylene pipelines, it is often necessary to create an additional branch. In such cases, insertion into the existing highway is required. To solve this problem, a fitting is provided in the form of a saddle on the HDPE pipe. Elements come in various designs, but with the same quality, ensure the integrity of the tightness and efficiency of the network.
Content
Item Feature
The saddle on the pipe made of HDPE is a special part of the pipeline, which consists of two parts, crimping it on both sides. Often it is also called a “tie-in collar”. The device is intended for branching of irrigation, sewer, gas, water (both drinking and technical) and other networks of the main or private type.
Note! Many types of devices are applicable to taps in the highway under pressure, therefore, the installation of sewer and water supply units is greatly simplified.
The nurse-saddle is installed on the PND product without violating its integrity. Most models are equipped with their own cutter for drilling holes of the required diameter. The device can be mounted in cramped conditions, for example, in a mine, collector, well, etc. Installation is possible on a new or existing network. The nurse is also used for open laying of PND communications. With its help, it is realistic to crash into any desired place in the pipeline.
Varieties of saddles
The saddle tap is more versatile, since it is produced with different diameters for different types of pipes. On sale there are not only elements for HDPE products, but also for steel, cast-iron (110 mm) options. In addition, the material of the saddles can also be brass, polyethylene.
According to the design, saddles are divided into two types:
- overlays;
- clamps.
The saddle plate (or electrowelded saddle) is specially designed for installation on HDPE pipes. Installation requires the use of electrodiffusion welding. The cost of the element is more compared to crimp clamps. However, the place of its junction with the pipe is monolithic so that it is no different from the usual welding of two HDPE parts.
Modifications of the type of crimp clamp are installed on the pipe by tightening two curved halves, one of which contains a threaded bend. A transition piece is located in it to make the insert into the pipe. The price of such a saddle on the PND product is very low, which determines its availability.
The most vulnerable and dimensionally dependent are crimp elements that do not have hermetic rings. They require a very tight fit.
Crimp Clamp Properties
The saddle-clamp made of polypropylene of the PP-B block copolymer is produced with diameters of 31.5; 22.5; 20.0; 16.0; 12.5; 11.0; 9.0; 7.5; 6.3; 5.0; 4.0; 3.2; 2.5; and 2.0 centimeters. The element has a maximum operating temperature of 45 degrees and is characterized by protection from ultraviolet radiation.
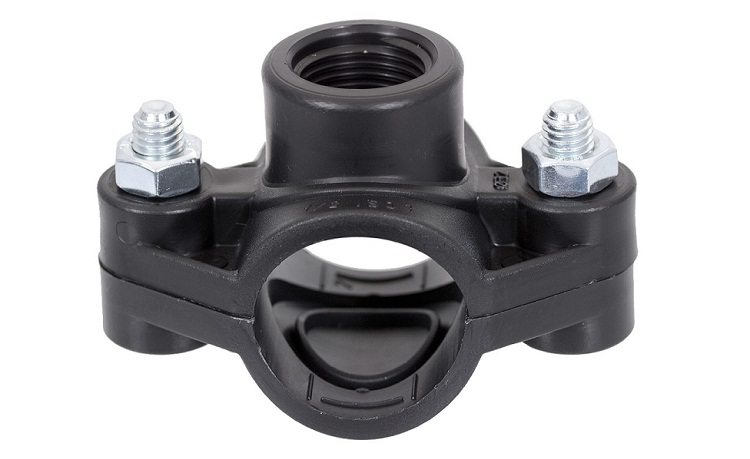
The thread on the clamp allows you to reliably attach the required element - a crane, elbow or adapter
The presence of a threaded outlet allows you to install a branch, tee, ball valve, adapter and other parts with an external thread. On its inside, a seat is provided for the o-ring, the material of which is rubber (for example, NBR 70).
Note! By installing a clamp and tightening the bolts, you can ensure the tightness of the connection node. Its maximum working pressure is up to 10 atm.
Important properties of the saddle on the HDPE pipe of this type is the simple design, lightness, chemical resistance and ease of installation. The branch has a standard pipe thread (from ½ to 3 inches), which allows it to be used with both plastic and steel fittings.
PND pipe saddle
The saddle plate is often used on plumbing and gas PND products. In its lower part there is a heating element, which is installed in the manufacturing process of the part. Using the apparatus for electrofusion (electrodiffusion) welding, the saddle is coupled to the HDPE pipe. Errors in the selection of parameters for welding are practically eliminated, since modern devices have the function of automatically setting the voltage and operating time with each fitting.
The required mode is selected using the barcode printed by the manufacturer on the electrowelded saddle. In its lower part there is a belt, due to which it is secured before welding in the required place.
The joining process consists in the transition to the elastic state (melting) of parts of the pipe and saddle when the spiral is heated by electric current of the required power for some time. When cooling, a single system is formed. Nurses of this type can withstand water pressure up to 16 atmospheres, and gas - up to 10. If there is a special valve and thanks to the equipment, the insertion into the line can be carried out under pressure.
Some types of electrowelded elements
There are several types of electrowelded saddles: with or without a head (rotary or non-rotary) part, with / without a mating part. Elements with a rotatable head are made in the cross-sectional range from 4 to 40 cm, non-rotatable - from 6.3 to 22.5 cm. In the first case, the construction is prefabricated, in the second - there is the possibility of retraction to a right angle relative to the main highways.
Such saddles are mounted on the HDPE pipe with bolts and nuts, and then welded in an electric-welded way.
Note! Installation requires a saddle key. It is with its help that the cutter, which is located in the head part, cuts into the pipe with a suitable degree of tightness.
Nurses, in which the head part is absent, can be with an exit for welding or with a cast pipe. These design features affect the installation method. In the presence of a molded nozzle, the saddle is mounted to the pipe by butt welding or an electric-welded coupling. Elements with an outlet for welding involve the simultaneous installation of them on the highway and the outlet pipe.
To install a saddle with a missing mating part on a large-diameter pipe, special straps are needed to prevent the offset care from shifting during welding.
Saddle Installation Technology
The type of construction or attachment of saddles affects the installation process. Among the stages of installation of crimp elements stand out:
- blocking the pipeline section;
- cleaning the pipe from dust and dirt, degreasing its surface;
- mounting the saddle on the surface and adjusting its position;
- bolting the part;
- re-checking the installation and final tightening of the bolts;
- drilling holes in the pipe.
Installation of electrowelded samples includes:
- pipeline shutoff (if necessary);
- scraping of the outer layer of the pipe in 1-2 mm at the installation site of the saddle;
- degreasing and cleaning of the polished surface;
- mounting parts using belts;
- adjustment of the saddle position and belt tightening;
- time stamp on the pipe when welding starts (if necessary);
- connection of welding machine wires to fitting terminals;
- waiting for the completion of welding;
- drilling holes in the pipe.
At the last stage, belts and other auxiliary equipment are removed. Such installation of saddles on the HDPE pipe is quick (work takes several minutes) and is very effective.
A saddle for a polyethylene pipe is a universal element, which is a type of compression fitting. It greatly simplifies and reduces the cost of installation of pipeline units.