People dealing with pipelines of various types constantly have to solve the problem of combining their elements into a single whole. Firstly, endless pipes in nature simply do not exist. And, secondly, the mounted system must have branches and various turns. For this purpose, PND compression fittings are used in modern construction. And so that not a lot of effort and time is spent on the work, you need to know the features of such details.
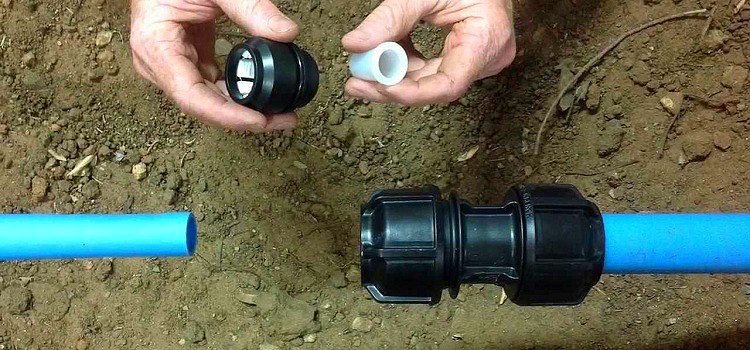
Compression fittings are a simple and reliable way to assemble water pipes from small diameter pipes
Content
Types of Fittings
Depending on what material was used for the manufacture of pipes, connecting parts have design features that allow them to be used for pipeline elements of only this type. For this reason, a certain set of fittings is suitable for each type of pipe. It should be noted that, with rare exceptions, the compounds sold using them are collapsible. And the correct installation of compression fittings for HDPE pipes is easily performed without using, for example, welding or other special equipment.
Actually, the greatest advantage of such a connection is precisely the ability to assemble / disassemble it. The fitting itself is an assembly structure that contains the following elements:
- parts mounted on the ends of the pipes to be joined;
- a mechanism or part that combines the above components into a one-piece sealed unit.
Modern industry produces the following types of fittings:
- crimp;
- flanged;
- welded;
- threaded.
Of these, compression fittings occupy a very large niche in the modern market. Their other name is crimp.
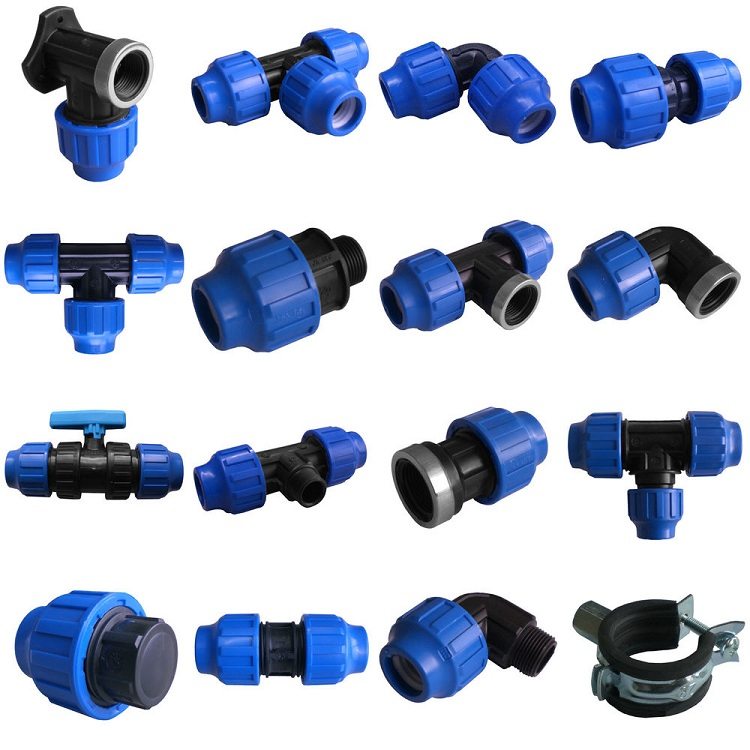
PND fittings come in many different shapes and purposes, the assortment includes not only connecting elements, but also bends, tees, cranes and other details
Design and use of compression fitting
All parts of this connecting element are housed in a body that is resistant to ultraviolet radiation. The counterpart includes a press-in sleeve and a nut cover. Sealing of the connection is ensured by a sealing ring installed in the groove of the housing. When disassembling with subsequent assembly, it must be replaced with a new one. The clamping ring plays the role of a damper, smoothing shock impulse loads. When the nut is screwed on, the seam ring clamps the polymer pipe due to the conical shape of the nut.
Compression fittings are the main elements for connecting HDPE pipes grades PE 100, PE 80 and PE 40 with diameters in the range of mm, as well as products from low density polyethylene. The most admissible temperature of a working environment is + 95˚С.
Good to know! Such pipes are used for transporting drinking water and other liquids in utilities with a working fluid pressure of up to 16 bar.
The materials used for the manufacture of such parts are highly resistant not only to UV radiation, but also to chemically aggressive substances.Compression fittings for pipes are used mainly in low-rise housing construction, that is, in rural areas when laying street water pipes, water pipelines in villages, and also when installing greenhouses. With their use, irrigation systems are created quite simply. This is due to the fact that compression fittings provide the ability to easily dismantle such water pipes with their subsequent installation in a new place.
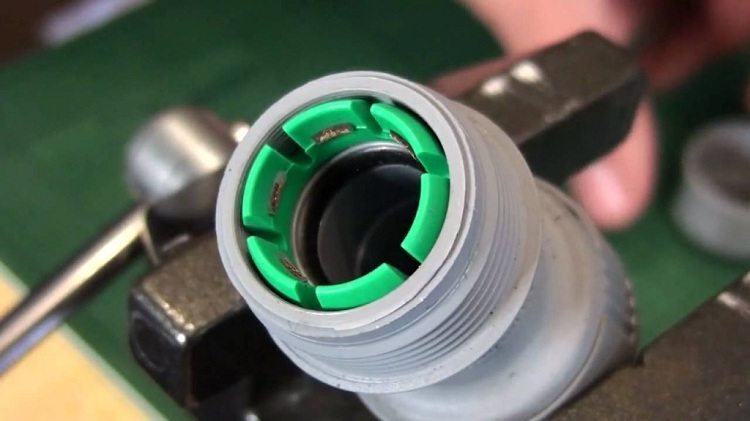
The design of the compression fitting is simple and does not require the use of tools during installation
Setting connection elements
It is necessary to create connections using PND fittings in accordance with the instructions. Before proceeding with the installation, you should study the quality of the tubular products. Their sizes should correspond to the values specified in the regulatory documents. In particular, attention should be paid to the following characteristics:
- the diameter should not deviate from the nominal value by more than 1%;
- cross section ovality should not exceed 2%.
If deviations exceed the above limits, such pipes should be laid in horizontal sections for safety.
Connecting products with a diameter of up to 50 millimeters are installed manually. For elements of a larger cross section, a special key is used for compression fittings. Before installation, the pipe must be cut at an angle of 90 °, thoroughly clean its surface, eliminate bumps and round the edges. The presence of defects is unacceptable.
The installation procedure does not require a long time. First, a nut is put on one of the prepared ends of the pipe, after which a clamp ring is installed. Then a pipe is inserted into the fitting. In this case, it is necessary to control so that the ring comes to a stop. Then the nut is twisted manually or using a tool.
The main advantages of HDPE fittings include:
- the connection is strong and durable;
- simplicity and high speed of installation;
- it is allowed to connect pipes made of different materials;
- non-susceptibility to corrosion;
- there is no need to carry out control of the connection and regularly tighten the nut;
- from the above paragraph it follows that it is allowed to lay piping systems fastened with HDPE fittings not only in the ground, but even in concrete.
-
Communications connected by similar fittings are laid both by ground and underground methods
Types of fittings for connecting metal-plastic pipes with products from other materials
In general, the connection of tubular products made of metal-plastic is carried out using fittings of the following types:
- detachable (threaded or collet). The cost of such parts is quite high, but the possibility of repeated use allows you to save on the acquisition of new samples. The design of the detachable fitting includes the following elements:
- the main brass part coated with a protective layer;
- crimp ring (open) for plastic pipes;
- rubber gasket;
- press fittings. After installing such products in a metal-plastic pipe, a monolithic non-separable system is formed.
Good to know! To fix the connecting element of this type, a special tool is used - a press machine. This unit is manual and hydraulic microprocessor.
The advantage of the press fitting is that the connection points are practically invisible. Among the shortcomings of such parts, home craftsmen distinguish the following moment: their joints with a metal-plastic pipe are afraid of frost. That is, there is a chance of a disconnection. Therefore, installation of a structure containing such elements is not recommended outdoors;
- compression fittings for connecting plastic pipes. These parts include a union nut, a compression ring, and a fitting.To install a compression fitting in a metal-plastic pipe product, follow these steps:
- align the pipe. Before and after the proposed cutting site, a straight section of at least 10 centimeters long must remain;
- outline the place of cutting the pipe;
- cut the pipe segment at right angles according to the marking;
- process the end face with a scan so that the section has the correct rounded shape;
- put a nut and a cut crimp ring on the pipe;
- moisten the fitting;
- put the fitting on the pipe, having achieved the stop of its end in the fitting edge along the entire plane;
- tighten the nut first by hand. Then use two wrenches: hold the fitting with one of them, and pull the nut with the other, leaving one or two threads of thread in sight. The use of a key with additional levers is unacceptable.
Connection of metal pipes by compression fittings
The use of compression fittings for metal pipes is quite a new kind of connection. It is not used as widely as other options. We are talking primarily about steel pipe products. The design of such a connecting part is similar to the structure of analogues for plastic pipes. It contains a nut, a ring, as well as a rubber gasket.
The use of crimp PND fittings for steel pipes has some features that must be considered when operating the created engineering communication line. In particular, the tightness of the joint may interfere with mechanical stress. Using force, the pipe can be pulled out of the fitting. But the use of steel pipe products is just focused on creating a strong pipeline system.
There is one more point. The presence of a rubber gasket provides that the temperature of the working medium transported along the highway should not exceed + 95 ° C. This indicator is typical for plastic pipes. The question then is, why install more expensive steel products.
Helpful information! But still, when you need a quick installation in conditions of limited access that impede the possibility of threading, the use of compression fittings will be justified.
How to choose
Fitting plays an important role. It was said above that they mount it both on branches and on turns. For this reason, it is subjected to maximum pressure. In order for such parts to be used for a long period of time without losing the main properties, when choosing them, pay attention to the following points:
- Is there a certificate of compliance with generally accepted technological standards;
- ideally shaped o-ring;
- accuracy of the geometric dimensions of the seat.
Installation of pipes with compression HDPE fittings with the right choice will not cause any special difficulties.