A metal hose for cable laying is an elastic profiled sealed product, for the manufacture of which galvanized or stainless steel tape and end connecting fittings are used. The special reliability of the protective functions is acquired due to the combination of high flexibility and strength inherent in the base material, significantly enhanced by the presence of stiffeners.
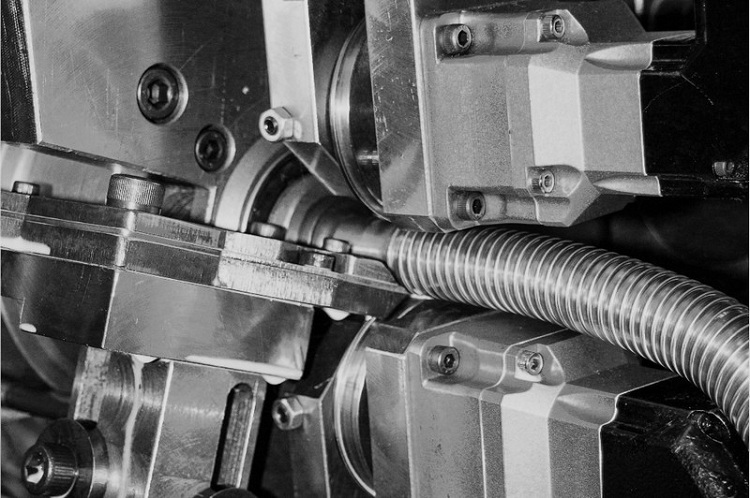
Production technology allows you to give the sleeve special flexibility, which is important when laying winding sections of electrical wiring
Content
How does a metal hose work?
The use of corrugated sheaths for cable laying is considered to be a truly revolutionary breakthrough in engineering communications equipment. The level of security of the laid lines has increased markedly, new opportunities have appeared for the implementation of covert wiring. In cases where special reliability and additional protection are required, cable networks are sheltered using durable metal as a protective sheath. A corrugated metal pipe is not without reason given an advantage over smooth-walled and plastic analogues in conditions where a combination of flexibility, highest strength and relatively low weight are required.
Laying the cable in the ground, for example, leads to the creation of significant mechanical pressure on the protective sheath. Soil pressure falling on a corrugated surface is distributed over a much larger area than if a smooth plane appeared under the load. Therefore, the level of mechanical load per unit surface is reduced.
The subtlety is that when a cable is laid in a metal hose in the soil or screed, then it is necessary to ensure a tight fit of the solution or soil to the surface of the protective structure. Otherwise, the level of its deformation will increase, since in the presence of voids, the walls of the pipe will not fully transfer a certain part of the vertical load to the surrounding space. It is proportional to the increase in its plane.
How are metal hoses made?
Corrugated metal pipe is manufactured in stages. First, a steel strip is selected that meets the conditions of the intended use, the thickness of which is 0.25-0.3 mm, rolled up into a thin-walled tube. The strips are interconnected using washers, flat-convex and flat-concave, and bolts. To create a pipe, argon welding is used, carried out by an automatic line, with a control of the reliability of the weld by a laser installation. The width of the seam does not exceed the wall thickness of more than one and a half times. Increased corrosion resistance is given by carrying out the galvanizing procedure. The use of stainless steel allows to achieve increased tightness, strength and security against the effects of aggressive environments.
The segmented surface is molded by applying pressure to the rollers, which differ in configuration and diameter.The segments of smaller diameter and wall thickness are smaller, so a certain flexibility is inherent in the metal hose. Due to the presence of such a property, it is not necessary to select fittings to the corrugated sleeve in order to make a turn, allowing to bypass the obstacle that has arisen along the proposed route of the pipeline. Bending a metal hose makes it easy to cope with such situations.
Good to know! For ease of use, the metal hose is equipped with a cable broach. To simplify your work, you should choose just such models.
Classification of metal hoses for laying electrical networks
Based on resistance to mechanical stress, corrugated metal hoses can be:
- light and flexible, with low mechanical stability. Installation of communications is allowed only in the absence of pressure on them. They are used for laying over false ceilings or under drywall boards;
- heavy, with medium strength. Spiral corrugated pipe is used to protect utilities laid by a hidden method. It is able to cope with the pressure exerted by the soil, plaster and concrete mortars;
- super heavy. Products designed for exposure to increased loads are used in case of increased safety requirements. They are used when building networks in public places with a high level of congestion - education and healthcare institutions, for example.
The above division in relation to resistance to external load is simplified, a more detailed view of the corrugation as:
- very light;
- easy;
- average;
- high;
- very high.
The value of the perceived external load can reach four thousand N / cm2.
According to the shape of the internal section, a corrugated metal hose for a cable can be:
- round;
- in the form of a vertical ellipse. Used in telecommunication tunnels.
Galvanized metal hoses for cable protection are divided into:
- ordinary. Unpressurized, durable and flexible products can cope with a temperature of three hundred degrees;
- with cotton thread seal.
Note! The maximum temperature for using products with HB thread is three times lower, but they are resistant to ultraviolet radiation and vertical drops of water droplets.
- with PVC insulating moisture sleeve. The achievement of tightness, increased tensile strength and protection against damage by leakage currents is accompanied by a weakening of the resistance to double the temperature increase.
The use of corrugated metal hoses for cable laying
The use of a corrugated sleeve, which is distinguished by a higher cost than plastic ones, is resorted to in the following cases:
- providing for the need to protect cable products from mechanical stress fraught with damage;
- when laying hidden wiring, which over time is supposed to be replaced;
- to provide reliable additional protection against electric shock;
- in case of laying on structures prone to fire. Use in wooden houses and over false ceilings involves the use of additional non-combustible material that separates the metal hose from the surface;
- in order to protect the cables laid parallel to the pipelines through which hot water is transported, or gas pipelines, as well as at the intersection of such utilities;
- with hidden laying in screed or dirt;
- when cable lines pass through an aggressive or highly dusty environment.
The dimensions of the metal corrugation supplied in fifty and one hundred meter coils allow it to be used in different conditions, depending on the required diameter:
- for telephone lines and wires of lighting, signaling - 16 mm;
- to the switch or socket - 20 mm;
- connecting junction boxes - 25 mm;
- passage through interfloor ceilings - from 40 mm.
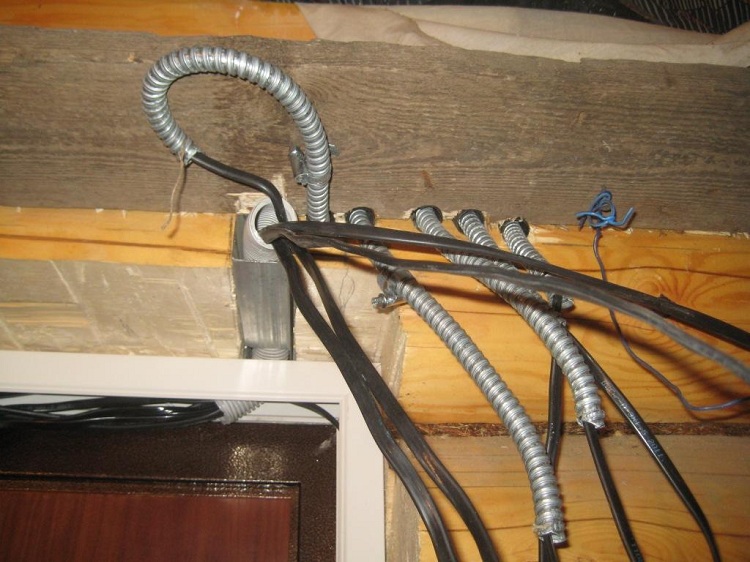
Laying wiring in a metal sleeve is especially relevant for a private house, where wires can damage rodents
Advantages and disadvantages
The use of a metal hose when laying cable networks promises such advantages:
- long-term operation of the system, which can last up to half a century;
- ease of arrangement that does not require the use of a special tool;
- the impossibility of damage by rodents;
- immunity to atmospheric precipitation and aggressive environments;
- protection against mechanical damage;
- incombustibility;
- the presence of additional protection against electric shock during grounding provided by the PUE;
- the ability to replace a section of the cable network;
- high flexibility, combined with the preservation of a given bore and not leading to the creation of internal stresses and microcracks that violate the integrity of the shell;
- ecological cleanliness.
The distribution of metal hoses for cable is constrained by the rather high cost of products, which is attributed to their shortcomings, as well as:
- extension of installation time;
- the requirement to exclude the possibility of moisture accumulation, which reduces the level of insulation.
It's important to know! Moisture accumulation is fought, providing for drainage during installation at the lower point of the structure.
Installation
Cutting off a piece of a metal hose of the required length, hold the broach when biting with side cutters, pull it out a little and bend it with a hook so that the slightly stretched cable does not slip inside. The cables marked for laying are pulled into a bundle, fastened with smooth PVC insulating tape, which does not create additional friction during pulling.
The harness is attached to the cable:
- entwined with steel wire pulled together with pliers;
- punctures of external insulation on the tow with a pull cable, followed by wrapping these points with electrical tape.
The cable bundle is usually tightened together, simplifying the operation and reducing the risk of breakage. First, the required tension is created, for which they resort to reliable fixation of the free end of the broach.
Tightening the harness, they proceed to fasten the structure, using clips corresponding to the diameter of the metal hose and able to withstand it, or an aluminum mounting strip. The uniform arrangement of the fasteners eliminates the sagging of the corrugated pipe.
Note! With hidden wiring, the corrugation is located in the groove (strobe).
It is unacceptable to leave the wires open by connecting to any device. To do this, the end of the metal hose is cleaned inside, and the device provides a rubber seal suitable for a given diameter of the corrugation. These actions are especially important when outdoor installation is underway.
The use of a corrugated metal hose when laying cable communications is certainly justified when it is conducted by a hidden method. With a closed gasket, the properties of a metal corrugation are used in the best way. In other cases, it is advisable to be guided by the rules of the PUE, choosing a protective shell from other materials, which is more expedient and economically.