Polyvinyl chloride (PVC) pipe can be found in a variety of areas. Large and small diameter products are widely applicable in the construction of transport channels for substances in a vapor or liquid state (for example, a thick-walled structure for external sewage), cable protection (DCS products). PVC pipes are indispensable because they are of high quality and properties. Plastic products (channels, connecting nodes) in most cases are made by one set.
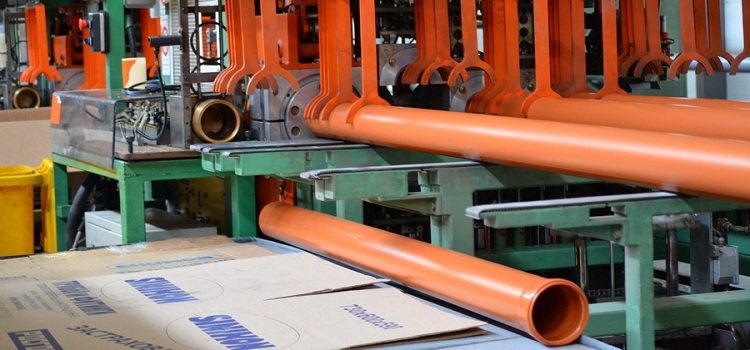
A wide assortment and high performance characteristics allow the use of PVC pipes in the construction of a variety of objects
Content
Physico-chemical features of polyvinyl chloride
Polyvinyl chloride is a thermoplastic synthetic material that has a different degree of polymerization, depending on the conditions of its conduct, and physico-chemical properties. PVC-based plastic is produced in two forms: “with” or “without” the use of a plasticizer. Accordingly, plasticized (PVC-F, FPVC, PVC-P) and unplasticized (PVC-R, RPVC, PVC-U) polyvinyl chloride are distinguished.
Externally, marketable PVC is a white powder that has no taste or smell. This plastic is insoluble in water, durable, exhibits good dielectric properties, which is important for DCS PVC pipes, resistant to alkalis, acids, mineral oils, alcohols, soluble in ketones, esters, aromatic and chlorinated carbohydrates. The material is well compatible with plasticizers, for example, sebacinates, phthalates, phosphates, practically non-combustible and resistant to oxidation.
Note! Plastic of this type has a low heat resistance and when heated above 100 degrees, it decomposes noticeably. To increase the specified parameter and improve the solubility of PVC is subjected to chlorination.
The main physical and chemical parameters of the material are given in table No. 1.
Table 1
Index | Value | unit of measurement |
Molecular mass | 40 thousand-145 thousand | |
Auto ignition temperature | 1100 | ºС |
Flash point | 500 | ºС |
Flash point | 624 | ºС |
Density | 1,34 | g / cm3 |
Bulk density | 0,4-0,7 | g / cm3 |
Decomposition temperature | 100-140 | ºС |
Glass transition temperature | 70-80 | ºС |
Raw materials for the production of PVC pipes
For the manufacture of plastic PVC pipes, polymer raw materials and special technical devices are used. Channels of various diameters are obtained by extruding the mass through a molding element.
In order to expand the application and improve the properties of the finished product, the following can be added to the mixture:
- material that minimizes the time spent on the polymer formation process;
- polymer retardant;
- material that gives the main component of the mass stability and quality of the opposition;
- additives that help prevent the occurrence of ET particles (electric current);
- substances that soften the polymer mass and give it greater flexibility;
- components that paint PVC pipes in the desired color.
In addition to these additional elements, others can be mixed into the polymer mass, for example, those that adjust the quality characteristics of the finished product.
Technical equipment for the manufacturing process of PE products
The production of pipes from polymers (PE, PVC) is based on the use of such devices:
- roomy containers for raw materials;
- a device for forcing the mass and giving the product a certain shape of the required diameter;
- installation device for measuring and cooling system;
- equipment for cutting PVC pipes (a special machine or tool with a rotating disk).
In addition, the production hall can be equipped with auxiliary mechanisms, for example, for moving and lifting loads.
Note! The technical equipment for manufacturing (PVC, PE pipes) can easily fit on an area of about 100 m2.
The production cycle consists of the following stages:
- extruding the mixture;
- measurement of product parameters (diameter, etc.);
- cooling procedure;
- pulling the product;
- trimming in accordance with the specified parameters.
Upon completion, the laying of the finished product and its labeling is carried out. The technology allows the production of both large and small diameter PVC pipes.
How to get plastic pipes
At the first stage of production, the material (plastic) is loaded into a special container, which is equipped with heating elements and a screw mechanism. During rotation, the temperature of the polymer mass increases to certain values. Next, the liquid plastic mixture is sent to a special compartment of the extrusion device.
To give the PE, PVC pipe the required shape, diameter, it is necessary to use special molding parts with certain parameters. Having passed through the extrusion mechanism, the mass takes the form of blanks. Next, the product is measured in a vacuum tank, which has the form of a closed container 3 meters long with pumping equipment.
In the next step, the plastic pipe is placed in a system with a rarefied atmosphere for cooling. Using a special installation, the stretching process is carried out. At the final stage, polyvinyl chloride pipes are cut into pieces of a certain length and stacked on shelves.
Scopes of the PVC pipes
The widespread and widespread use of PVC channels is explained by their characteristics and properties. Plastic pipelines use:
- for connecting hot and cold water;
- for summing up the external and internal sewerage;
- for the device of drainage systems;
- for laying an electric cable and other communications.
PVC pipes of large and small diameters are suitable for both domestic sewage systems and industrial needs. Distinguish between rigid and corrugated models. For external networks, thick-walled PVC pipes are used, designed for significant loads.
Note! The maximum allowable temperature of the water that drains through the pipeline is 60 degrees.
If PVC pipes are used as drainage channels, then it is necessary to wrap them with geotextiles, which will protect the line from silting and clogging. Perforated products vary in diameter: 50, 100 and 200 mm. For a water supply device, choose PVC pipe pressure type. In addition, gas can be transported through such a pipeline. For this, production of special transparent options for PVC channels has been established.
A particularly important area is the use of DCS pipes for electrical wiring. Products fully comply with the requirements that apply to this kind of channels.
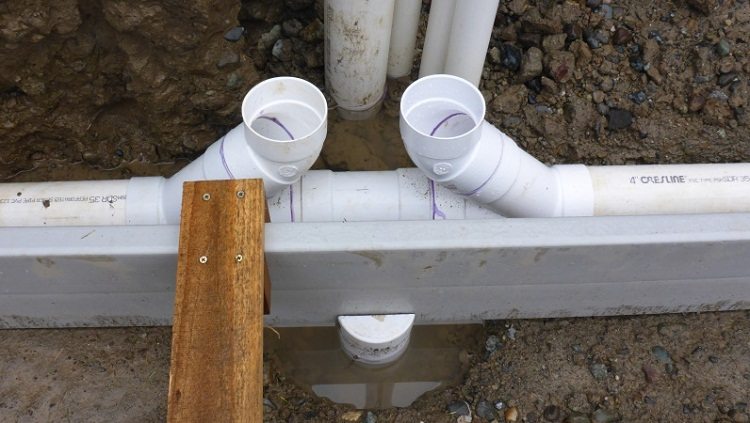
Polyvinyl chloride pipes are used for water supply systems, gas pipelines, as well as drainage systems
Corrugated Canal Production
Plastic corrugated channels are distinguished by a relief surface. The main advantages of this type of product are its versatility of use, lightness, ductility and compactness during transportation.
The production process of this type of product is similar to the technology for producing a conventional polymer pipe and is carried out using a line for the production of corrugated models, which is complemented by a special device called a corrugator. This element of the production system consists of two half-forms with a channel designed for the passage of cooling water. Half-forms merge at the working site and form an enclosed space.
From the extruder, the workpiece enters the work area, where it is pressed to the surfaces under air pressure and hardens, taking the form of a corrugation. Next, the product is ready for winding. It does not require the presence of baths, since cooling takes place directly in the corrugator. The production of large sections on such a line is limited to 63 mm.
What is a BCS pipe
DKS is an international company that is one of the leaders in the production of products for the electrical market. The range of products is very diverse and is represented by both flexible and rigid models.
DKS plastic pipes are made of polymeric materials and are intended for reliable protection of the electric cable during installation of electrical wiring. Such products are used in the construction of industrial and residential buildings, retail and storage facilities.
Note! Externally, the BCS channel is a hollow inside a cylindrical structure, not a very large section, but of considerable length. A computer, electric, telephone or television cable can be placed in it.
It is important to consider that the voltage of direct or alternating current in such a network should not be more than 1 kV. There are open, half-hidden and hidden gasket. It can be carried out in stationary household electrical installations with working conditions in open space or indoors.
Types of BCS products
Corrugated pipes DKS can be divided into 3 series:
- Series 7 - from low pressure PE.
- Series 9 - made of PVC compound.
- Series 10 - made of polypropylene.
DKS pipes made of low pressure PE are used to provide a high level of protection and can be used in various climatic conditions. Polypropylene products are characterized by high resistance to moisture, low and high temperatures, and also do not spread combustion.
Flexible corrugated PVC pipes can be divided into heavy and light. They are distinguished by a good degree of protection, durability, moisture resistance, incombustibility, a good range of working (from -25 to +60 degrees) and installation (from -5 to +60 degrees) temperatures. Light models are often used indoors, while heavy models are often used for installation under a cement screed. DCS products deserve special attention, since it is possible to produce reinforced structures that can protect the power circuit under the influence of constant vibrations.
PVC pipes are actively used in construction due to the properties of environmental friendliness, wear and moisture resistance, as well as fire resistance. Their production is automated and allows you to enhance the required characteristics of the finished product due to the introduction of special additives in the source material.