Profile products are one of the most popular in many industrial and economic sectors. The organization of an enterprise manufacturing profile metal rolling is a reasonable decision, but required significant investments, even in the case of a small workshop (it’s pointless to launch a powerful line right away). The first thing that an entrepreneur should do is familiarize himself with the production technology and study the needs of potential buyers in the region.
Content
What is a profile product and what is it?
Profile pipes are made for the assembly of metal structures of various sizes and purposes: frames, hangars, temporary and permanent greenhouses. Standard metal products with a round cross section are not suitable for such purposes, just as profile pipes for water and gas pipelines are not suitable.
To make sure the feasibility of producing profile pipes, it is worth familiarizing yourself with a wide range of areas of application for these products:
- profile pipes of a standard configuration. The scope of use has been expanded to the construction of scaffolding, pipelines, the protection of cable equipment, the formation of irrigation systems or fencing.
- trunk profiles. They are used in the construction of large-sized pipelines with frequent pressure drops as supporting segments (these pipes are most often made according to the manufacturer's specifications and for an individual order).
- profile rolled metal with increased resistance to chemical compounds. It is in demand in the food, pharmaceutical and chemical industries.
- engineering profiles. They are used in the production of automobile pistons, shafts, cylinders, bearings.
The types of sections of profile products are also different. It is oval, flat oval, square, rectangular, polygonal. By a separate order, an enterprise may be able to produce profiles with a section in the form of a triangle, hexagon, etc.
There are several ways to make profiles. Depending on the production method used, the properties of the product will differ:
- Hot rolled profile products of a seamless type: used in environments requiring increased strength indicators. Usually anticorrosive, resistant to any aggressive acids and substances.
- Cold rolled profiles or standard: more resilient structures that can withstand significant pressure drops.
- Cold-rolled profiles of electric-welded type: strong and durable structures, but only subject to operating standards.
Mass production of pipes of various purposes require adjustment in the list of required equipment. Below is a diagram of the production of standard shaped pipes, which should be varied in accordance with the developed business plan.
The technology of manufacturing a profile pipe
Theoretically, the creation of profiles with square or rectangular cross-sectional shape requires the presence of only one machine - milling, capable of providing sufficient conditions for molding. This production method involves the purchase of ordinary steel pipes with a circular cross-section and their refinement on a rolling mill.
The resulting metal rolling will visually fully correspond to the consumer's ideas about rectangular profiles, but technologically such products will be considered unprofessional. The method of rolling from finished round pipes is suitable for those entrepreneurs who do not plan to launch a line of profiles for large-scale tasks (such as building frames for hangars or even residential buildings).
Important! Profiles deformed on a rolling mill can only be used as the basis for external advertising (pillars-passers), to meet the needs of private construction, furniture and decorative interior elements.
These products will be in consumer demand, but they will not at all be suitable for organizing those designs to which higher safety and reliability standards are imposed.
If it is planned to produce better products (which significantly expands the marketing options for finished products), then the most suitable option for organized enterprises will be the production of a profile pipe in a full cycle, which includes many successive stages.
Production of profile pipes in a full cycle
The production technology of profile electric-welded products in a full cycle implies the following operations:
- strip processing;
- forming and welding a round billet under the profile;
- round pipe profiling;
- quality control check;
- heat treatment.
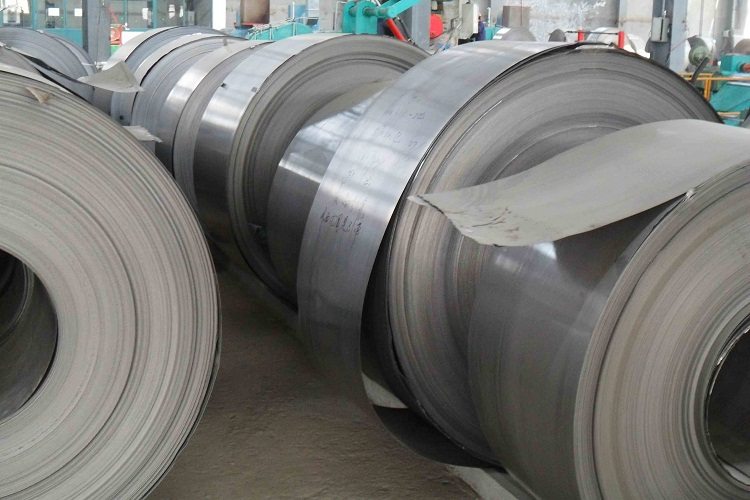
The full cycle of pipe production begins with the processing of the strip - the steel strip of the desired width
The basis for creating blanks for hire will be metal strip - steel sheets of the required grade (usually low alloyed or carbon steel), delivered to the production site in rolls. Profile manufacturing enterprises supply sheet metal directly from metallurgical plants, which allows not only to reduce the cost of production, but also to ensure quality control over each unit of goods.
Helpful advice! The strip differs not only in grade and quality of steel, but also in thickness. The presence at the enterprise of billets of various thicknesses makes it possible to produce pipes of all levels of reliability and expand the range of products offered.
The first step in the processing of the strip will be its unwinding and cutting into segments of the required width. To cut a sheet of steel sheet into even longitudinal sections, a special cutting unit is required. It is designed for cutting metal strips with a thickness of 5 cm or more (different machines have their own indicators, they also depend on the thickness of the strip). For the convenience of carrying out further actions, the obtained segments are welded into a single continuous tape.
The tape obtained after cutting and welding is wound on a constantly rotating drum. This production principle is implemented to ensure that the rollers do not stand idle, and rolled profile continuously. A reserve of future workpieces is wound on the drum, which should also be periodically updated.
A further action will be the transfer of the metal strip to the forming mill. Here, in several stands, the rollers form a blank that is round in cross section. The workpiece has an infinite length, the molding machine continues to produce it until the tape in the drum ends.Usually this stage occurs without heating, with the participation of cold sheet steel, but sometimes the strip of steel is immediately subjected to heat treatment.
The blank with an open seam is transferred to the welding installation, where its edges are welded by means of high-frequency currents. In parallel with this process, the product continues to be squeezed by the rollers, due to which, over the entire length of the seam, both outside and inside the pipe, excess melt escapes - burr, which is immediately removed by the cutters. Workpieces that have passed the welding stage are cooled by emulsion compositions.
The principle of rental and control of a profile pipe
The chilled billet passes to the profiling stage, which is carried out in several cycles:
- Hire is sent through the rollers to give the most identical round shape along the entire length of the product;
- The round pipe passes to the profiling machine for crimping from four sides: as a result, metal is obtained with the required section shape.
The second technological stage is necessary only if it is planned to produce pipes with a rectangular (square, polygonal) section. For flat oval or oval profiles, rolling through the first control rollers is sufficient. After that, the workpiece is cut into segments of a given measured or unmeasured length, during which it is subjected to continuous cooling.
The most “weak spot” in electric-welded constructions is considered to be a weld, which is subject to mandatory tightness. The manufacture is not considered completed, and metal rolling - approved for sale, if the following verification methods have not been performed:
- Eddy current flaw detection. The flaw detector works on the principle that the electromagnetic characteristics of any metal, including steel, are affected by various degrees of stress caused by defects in the weld, internal shells and other undesirable factors.
- Visual inspection A quality control specialist inspects the seam in order to detect damage resulting from malfunctioning of the forming and profiling rollers, and welding defects. The specialist can also identify visual flaws that the flaw detector cannot detect: irregularities, mechanical damage.
These control methods can be used both in parallel and in a single order. In addition to inspection of finished products, it is imperative to carry out systematic prevention of all equipment of the production workshop in order to avoid mass rejection of products.
To improve the strength characteristics of steel, the finished product at the final stage of the cycle is re-heated. This is necessary for the reason that when the steel is deformed, internal stresses are formed in them. The hot product is left to cool completely, and then transferred to the packaging department. Hire, past this stage, has a slightly higher cost. This explains the lack of this process at some enterprises. Whether or not to include the stage of additional hardening in the production cycle depends on the concept of the planned enterprise.
Equipment for the production of shaped pipes
The amount of equipment purchased directly depends on what level of quality the company expects to receive and what possible distribution channels exist. It makes no sense to purchase high-performance equipment if the only option currently available for selling products is furniture or advertising companies, small construction companies.
The main criteria for choosing a hardware component are approximate starting capital and volumes of output. For a young enterprise, a line of small, in extreme cases, medium capacity will be enough.
The standard line on which the profile pipes will be rolled will be the following hardware:
- machines for unwinding, preparing and processing metal sheets (usually a console uncoiler);
- rolling mill for round tube molding;
- site for welding the workpiece;
- site for cutting the edges of the weld;
- cooling section;
- polygonal tube forming mill;
- cutting knife for cutting finished profiles.
Important! If a galvanizing site is planned in the production workshop, equipping the line with a special bathtub for galvanizing products will also be mandatory.
Production lines can be either fully automated or with the mandatory use of manual power. Automated lines have a higher cost, but also greater productivity. Standard lines are equipped with rectangular shafts only. To increase the capacity of the enterprise and, accordingly, profit, you will have to buy additional shafts, allowing you to give the profile a square or polygonal shape.
In addition to the purchase of equipment, it is necessary to take into account the initial costs of metal rolling, rent and salaries for staff. In the production workshop, two people can work on the same line of the profile pipe - the machine operator and the auxiliary worker. It will be necessary to invite not only the working personnel directly to the workshop, but also the technologist, if possible - laboratory assistants who monitor the compliance of the released products with the standards.
This type of metal construction, such as a profile pipe, is relevant in modern industry. Even a small, but well-equipped and well-reputed company can have a steady income and regular customers in a wide variety of production areas.